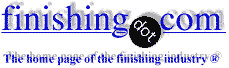
-----
Decontaminating galvanizing flux in situ. Hydrogen peroxide to reduce dross?

Q. How can I determine how much hydrogen peroxide I need to put on my flux tank during treatment?
Chris MorningstarEmployee - Philippines
March 7, 2024
A. You will need to know volume to be treated, and what you're treating it for.
Presumably you want to oxidize the Fe in there that got carried over from lack of rinsing or from pickle tanks that was depleted in HCl and high in FeCl2?
Will you also be adjusting the pH?
Start by figuring out the chemical reaction, check the stoichiometry, and then find the Fe you want to react. Calculate from there.
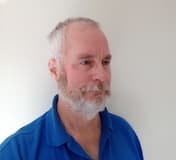
Geoff Crowley, galvanizing consultant
Crithwood Ltd.

Bathgate, Scotland, UK
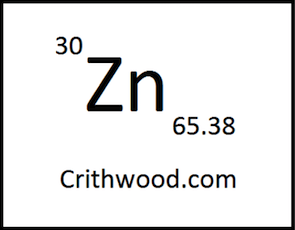
⇩ Related postings, oldest first ⇩
for Engineers, Shops, Specifiers
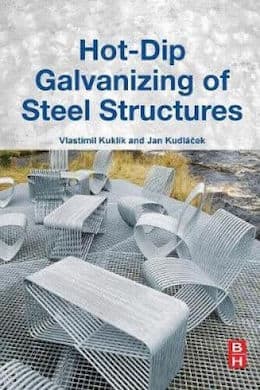
avail from eBay, AbeBooks, or Amazon
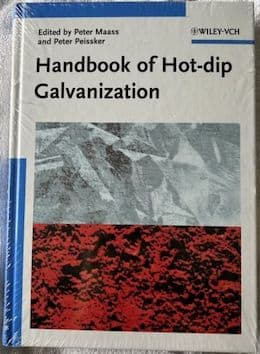
avail from eBay, AbeBooks, or Amazon
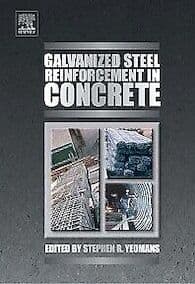
avail from eBay, AbeBooks, or Amazon
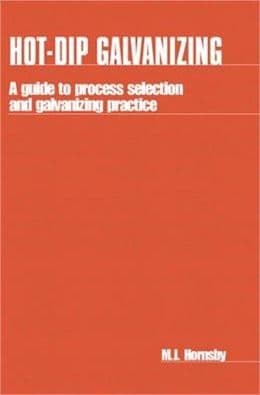
avail from eBay, AbeBooks, or Amazon
avail from Amazon
"User's Guide to Hot Dip Galvanizing for Corrosion Protection in Atmospheric Service" by NACE (1997 only rarely avail.)
avail from AbeBooks, or Amazon
(as an Amazon Associate & eBay Partner, we earn from qualifying purchases)
Q. In the use of zinc ammonium chloride preflux in jobbing hot dip galvanizing, poor rinsing before flux dipping can result in contaminated flux. This then translates to higher Fe in flux solution causing excessive ash and dross production, consuming expensive zinc. The answer is prevention - by proper rinsing. But once the flux is contaminated, rectification is expensive also. Dumping the tank and making up a new solution costs in disposal, and new chemicals.
But is there a way to remove Fe and HCl from the flux in situ (while retaining the longer term usefulness of the flux)?
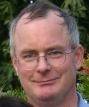
Geoff Crowley
Crithwood Ltd.
Westfield, Scotland, UK
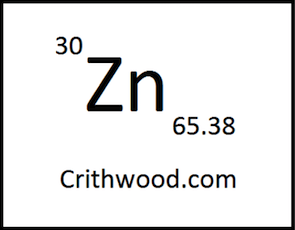
2004
A. Iron content in preflux should not be exceed 10 g/L and also the pH should be maintained within 4.0~5.5. If the pH goes below 4.0 the insoluble iron oxide is converted into soluble iron. Oxidation of soluble iron content to be done by continuous air purging or by using hydrogen peroxide treatment
Syed Kazmi- Dubai
A. It is better to take prevention action for the contamination of the flux tank from the first step of treatment.
You have to clean the surface very well before the fluxing step.
In the fluxing tank you have to add a wetting agent:
1)It dissolves light oxides that may have formed since pickling.
2)It promotes fast drying thus increasing production and stops excessive sputtering and spitting as the steel enters the molten zinc.
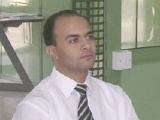
Ahmed Fouad Serag Eldin
Ein Shams - Cairo - Egypt
Multiple threads merged: please forgive chronology errors and repetition 🙂
Q. Hi,
My name is Karu I am working as a galvanizing in-charge. My query is --
I heard Hydrogen peroxide is added in flux tank to reduce the dross percentage. But I want to know how much quantity must be added to the flux.
Thanks in advance
Karu
Employee - Vizag, Andhra Pradesh, INDIA
March 23, 2009
![]() |
A. The theory is that H2O2 will oxidise the Fe in the flux, and in oxide state it will not produce dross in the zinc by reacting (Fe + Zn = dross). ![]() Geoff Crowley Crithwood Ltd. Westfield, Scotland, UK ![]() A. Hello Karu, ![]() Bill Reynolds [deceased] consultant metallurgist - Ballarat, Victoria, Australia We sadly relate the news that Bill passed away on Jan. 29, 2010. |
A. Sir:
To remove dissolved iron+2 (green in solution), you need to know what is the Fe+2 concentration (as percent or g/Liter) and you need to know the volume of the solution (Liters or US gallons or Imperial gallons). Next you need to know the two treatment chemicals which are: hydrogen peroxide and ammonium hydroxide. Also you need to know the concentrations of these treatment chemicals. Then you need to know the proper conditions for adding these treatment chemicals and the settling of the iron(+3)hydroxide (orange solid) that is formed. I have done this treatment many times in lab and in various plants. Removing iron+2 from the flux does NOT decrease dross in a "dry" kettle. It does decrease dross in a "wet" kettle. In a "dry" kettle it has been my past experience that removing iron+2 from flux reduces the zinc thickness on the product.
In more recent times we have found ways to galvanize with very high iron+2 (and high sulphate) in the flux and still get good %GZU (e.g. 5% to 6%; no credits for ash or dross). I am now studying a plant with very, very high iron+2 in the flux (e.g. 9%+), but I see ways to reduce zinc usage which may in part be accomplished by changing out the flux. Above 3% iron+2 in the flux cannot be purified (It turns to a thick orange soup with no liquid recovery; although a filter press may work with diatomaceous earth pre-cover). For a medium sized flux tank (e.g. 10,000 US gallons) it takes 3 to 5 days to do a good job. This can be speeded up with a proper flocculant, but then you must use a filter press. This last method takes 1 to 2 days. You DO need in-plant testing for Fe+2 because if you have an excess of hydrogen peroxide it will continue to give off oxygen and prevent settling. Peroxide also burns the skin very badly and ammonium hydroxide (aqua ammonia) gives off ammonia gas which is lighter than air and you MUST NOT have a guy working on your cranes during the first part of flux purification.
To change percent to g/liter (for baumé 18; e.g. density 1.14g/Liter simply multiply by 11.4.
Regards,
Galvanizing Consultant - Hot Springs, South Dakota, USA
Q. I'm not sure what is meant by a "wet kettle" and "dry kettle".
If you mean preflux dip and flux added as a crystal - that's the meaning of this term as I understand it, then a flux tank isn't a requirement in "wet kettle". So you must mean something else?
But for a prefluxing system, where a tank holds an aqueous solution of flux into which steel is dipped and then subsequently dipped in the zinc, then experience has shown that dross is proportional to Fe2+ concentration. Higher Fe, higher rate of dross production. Confirmed by 37 years data across 2 installations.
Below about 0.3% Fe there is a diminishing return, hardly worth any effort to reduce below that.
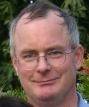
Geoff Crowley
Crithwood Ltd.
Westfield, Scotland, UK
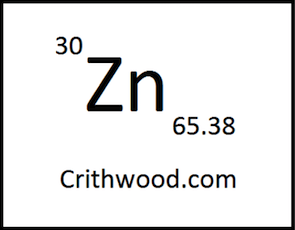
A. Geoff:
"Wet kettle" and "dry kettle" refer to the molten zinc in the galvanizing kettle. In a wet kettle there is a portion of the zinc surface covered by black, bubbling, molten "top flux," which is primarily the monosalt with globules of molten zinc mixed throughout. In the 1970's in North America perhaps 1/3 of all galvanizers were wet kettle. Today there is likely only a small number of wet kettles in North America, primarily on product like pipe fittings and chain link fence. A wet kettle can be operated with or without a flux solution prior to entry into the molten zinc. In practice, the pickled and rinsed steel (and in some operations fluxed steel) enters the molten zinc through this layer of molten top flux floating on the zinc surface. The product is then tractored side-ways and exits the molten zinc where the top flux has been skimmed back.
In a dry kettle there is no molten top flux. The pickled, rinsed, and water solution fluxed product enters the bare zinc surface. The flux is cooked off, the zinc surface skimmed and the product is withdrawn.
I aided several wet kettle operators to convert to dry kettle over the years. Use of flux was greatly lowered, as was zinc consumption. A wet kettle normally produces around three times the dross of a dry kettle, however the dry ash skimmings of a wet kettle are lower than a dry kettle.
You have your experiences and I have mine. I have purified many, many fluxes in the early days. Many times a galvanizer will say to me:
"After the iron (+2) is taken out of the flux, then the dross will be reduced." My experience with the dry kettle is that dross remains nearly the same, but the zinc coating thickness on the product is greatly reduced. I do NOW have data to indicate that the orange solid Fe(OH)3 at the bottom of the flux tank as a sludge may well increase dross in a dry kettle. A galvanizer told me that he produced 20,000 pounds of dross each month, whereas when he desludged his flux tank of the iron(+3) hydroxide he obtained only 10,000 pounds of dross each month. I asked him are you sure about this and he replied: "Well yes we did it three times."
In a dry kettle my experience is that the Fe+2 becomes a part of the coating and is not deposited into the zinc to cause dross. In a wet kettle the floating top flux dissolves the Fe+2 in the flux and then at the top flux zinc interface dross is formed. The last idea is supported by the practice of frequently changing top fluxes and having the dross production decrease.
Another consideration is that FeCl2 is not volatile and its presence in flux causes longer cook off times with resultant thicker zinc coatings on the product. My estimate is about a mil of zinc for each minute in the zinc. Thus: "A mil a minute." A mil is 1/1,000 of an inch and 25.4 microns equals one mil.
Regards,
Galvanizing Consultant - Hot Springs, South Dakota, USA
Q. This forum was really useful. I want to apply this on the galvanizing plant where I work. What I would like to know is if it's possible to do the same process by injecting air to the flux solution instead of adding H2O2 (hydrogen peroxide).
Thank you!
Hot Dip Galvanizing - Cochabamba, Bolivia
April 11, 2012
A. Yes oxygen in the air can be used to oxidize iron Fe+2 to Fe+3. Normal procedure is:
1)Adjust pH to about 4.2.
2)Calculate appropriate NH4OH to add via chemistry/math formulas based on Fe+2 in flux solution and volume of flux solution, and add the NH4OH solution.
3)Calculate appropriate H2O2 to add to flux based on Fe+2 in flux solution and volume of flux solution. Dilute H202 3 water to 1 H2O2 solution. Add H2O2 solution.
4)Keep flux solution hot at about 70 C. Keep airlines in flux for several hours. Cut off air. Keep heat "on" in flux solution 24 hours to "digest" Fe(OH)3 (makes smaller particles dissolve and grow larger particles of Fe(OH)3. Decant and shovel out Fe(OH)3 sludge.
DO NOT work on cranes while NH4OH is being used as NH3 gas goes upward and can make crane worker overcome and pass-out.
Air can be used rather than H2O2 but it takes about one week to purify in this way. Air cannot be used continuously because purification is done above pH 5 whereas working pH is about 4.2.
Regards,
Galvanizing Consultant - Hot Springs, South Dakota, USA
April 14, 2012
Q. Hi --
When we use of NH3 and H2O2 for refining of flux, which one is better first step to be added to the tank? And what is their reaction?
Thanks
- iran-khorasan-mashhad
May 30, 2013
A. Dear Friend,
Normally hydrogen peroxide 20% V/V is added to aqueous flux when you intend to filter it. The iron present in flux solution is in ferrous & ferric state, which is soluble. It converts to its Hydroxide and gets precipitated at the bottom of flux tank. After addition of H2O2 it is recommended to leave the solution for 8 hours to settle down the iron hydroxide. Now you can take out the solution from top, leaving the iron hydroxide in the bottom.
This not only reduces the iron from flux but also neutralizes the acid contents. Hence, ultimately reduces the dross formation.
- Sana'a, Yemen
Multiple threads merged: please forgive chronology errors and repetition 🙂
Q. What are the most likely contaminants that could build up in batch galvanizing flux? We find variable performance in our flux which according to the simple analysis done seems in spec. Sodium chloride suspected.
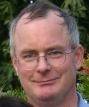
Geoff Crowley
Crithwood Ltd.
Westfield, Scotland, UK
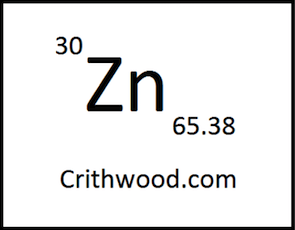
August 22, 2018
Q. Geoff,
The elements are: calcium, magnesium, manganese, potassium, and sodium. One of my clients has (all expressed as respective chlorides):
calcium chloride (CaCl2) = 3,601 ppm
magnesium chloride (MgCl2)= 1,893 ppm
manganese chloride (MnCl2) = 190 ppm
potassium chloride (KCl) = 300 ppm
sodium chloride (NaCl) = 3,480 ppm
Total NTNVs = 9,464 ppm in the working flux solution.
This client has periodic pimples on his product. My experience is that non-traditional, non-volatiles above 7,000 are a problem.
I have another client who has a total NTNVs of 3,189 who thinks that iron (+2) above 0.5% causes pimples.
What do you think Geoff?
Galvanizing Consultant - Hot Springs, South Dakota, USA
A. I suspect Na as the most common.
The others are not so commonly available, though this depends a lot on water quality. We have relatively pure water, with low Ca, Mg, Mn, K, but Na is in the process already in NaOH degreaser. So it can much more easily react with Cl to form NaCl and stay soluble in the flux solution.
The others could be problems where there's harder water.
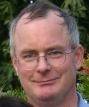
Geoff Crowley
Crithwood Ltd.
Westfield, Scotland, UK
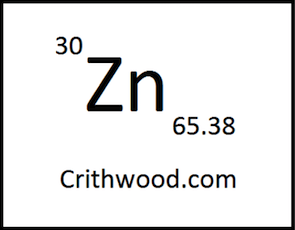
A. Geoff,
Mn comes from the steel and is prevalent in fluxes following HCl. Many fluxes from Europe are made from secondary sources like galvanizing plants and all five that I have mentioned are prevalent.
Why not have your "working" flux solution tested for the five elements that I posted?
To get a correct result the testing company needs to "spike" the flux with a known addition (for example sodium) to determine recovery and make a proper correction. Most testing companies do not do this and results are usually NOT correct. AA, AE, and ICP are "fooled" because they are non-linear and are affected by matrix effects.
Caustic is not the only source for sodium ion. Some flux companies put sodium in flux, either to make "non-fuming" flux or use cheap secondary starting materials. Thus you may want to have your new incoming flux tested also.
At one time I thought you told me you use a magnesium compound to neutralize your acid rinse water?
At present, I think calcium or magnesium may cause flux on the product to collect moisture from the air and cause zinc spatter at the kettle.
You say your water is "good." What is the TDS of your tap water? Is there a reason you think the flux makers have good tap water?
Some new fluxes have substantial potassium chloride in them, which causes galvanizers to use a higher concentration of flux and results in excessive "dry" ash.
TESTING of the flux is what needs to be done.
Geoff what do you think about pimples?
Respectfully, Tom Cook
Galvanizing Consultant - Hot Springs, South Dakota, USA
Thanks for input on this.
We typically run about 1000 ppm total dissolved chlorides in flux in the tank. Tests on bought flux (mostly German manufacture)don't show any concerning trends of contamination, but I know there are suppliers whose flux is rather poor in this respect.
Yes in one of two plants we used a bed of mangnesia to neutralise acid in rinse water (in the first only of two rinses between aid and flux), and in the other plant this is not done. There's no significant Mg contamination of that plants flux compared to the other.
We're really lucky in Scotland with very pure towns supply water. Out of the tap conductivity (a different way to measure TDS) is typically 20-30µS/cm. (in our powder shop we further clean that down to <5µS/cm). In galv this is pretty good. In the south of England they have poor water full of Mg, Mn, Ca, etc.
I have no information on flux manufacturers water supplies, but have reason to believe that its either good or that they clean it - to get such low contamination levels in the liquid flux they supply and we purchase.
We operate a zinc recovery system from the kettle ash, and this is the point where any changes in flux chemistry are first noticed, being far more sensitive than the at kettle observations.
While we've not used so called "low fuming flux", I've seen it used in several plants. In most cases it's K they use rather than Na. That is they substitute potassium chloride for ammonium chloride, that latter being the major source of fume in that operation.
On "pimples": that's a rather generic term for several issues. I've seen them resulting from reactive steels, from poor flux, from excessive immersion time, and perhaps other causes. I think reactive steel is the most common cause I've seen.
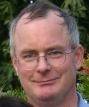
Geoff Crowley
Crithwood Ltd.
Westfield, Scotland, UK
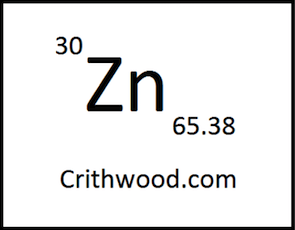
Q. In batch hot dip galvanizing it is normal to use a flux, and today most of this fluxing is done by dipping steel into a heated aqueous solution of the flux. Most commonly that flux is ammonium chloride and zinc chloride mixed. The proportions of the two constituents give rise to the labels "double salt", "triple salt" "quadraflux".
One problem with ammonium chloride is the amount of fume produced. The higher the ratio of this component, usually the more fume is produced.
Some galvanizers use so called "low fuming flux". This substitutes potassium chloride for the ammonium chloride.
Does anyone have experience of using this type of flux, and if so how does it perform? Do you find it difficult to maintain the chemistry? Any quality effects? Any other effects either good or bad? Is temperature of the solution important?
We're considering it for a new plant, as it seems that those using it don't need a filter to remove the particulates from the fume.
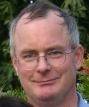
Geoff Crowley
Crithwood Ltd.
Westfield, Scotland, UK
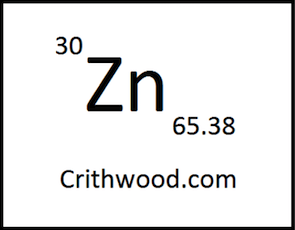
February 27, 2019
A. Geoff,
The US patent number 3,936,326 (1974) by Wolfgang Muller is likely the inventor of the smokeless flux that you are considering. Because this flux has not been widely commercialized in the last 45 years it is likely not very good. You can easily get a copy of the patent off the internet. It requires 15 minutes drying at 180 °C. This flux depends on a eutectic and is likely hard to maintain sufficient purity. For example, what happens to the melting point as the iron +2 builds in the flux and how to remove iron when required? In one example the flux is used at 33° baumé which would likely give a very large amount of skimmings. I doubt that an MZR machine could recover zinc from the skimmings. In this example the zinc is 1% in lead and the zinc is also 0.2% in aluminum. Such high aluminum is okay because there is no ammonium chloride in the flux. On non-reactive steel I wonder if enough zinc can be on the steel.
Let me know what you think after you read the patent.
Galvanizing Consultant - Hot Springs, South Dakota, USA
A. Geoff,
Two short stories.
An employee of a major USA automatic pipes galvanizer told me that when his flux had sodium chloride (NaCl) in it that the iron push down arms were dissolved by the molten zinc in a few days. When he got flux without sodium chloride then the push down arms had a normal lifetime of years.
In about 1985 in South Africa I saw workers put a "potassium chloride" flux which looked like miniature flying saucers (1.25 inches diameter by 3/8 inches thick) onto a pipes galvanizing kettle as a top flux. It melted without much smoke and the workers liked it because it lasted a long time and did not smoke much. I stayed in South Africa a few more weeks, and interestingly that kettle burned out at the corner where the "KCl top flux" had been put. There was some talk that the top flux may have overflowed the kettle and went down the outside. My stay had ended and I do not know what caused the kettle wall to burn through.
Likely wet kettle fluxes have NaCl or KCl or both to make them smoke less and last a long time, however it would explain why wet kettle galvanizers have more dross than dry kettle galvanizers. In the USA we are now having kettles last up to 20 years. I do believe that NaCl in flux increases the reaction between molten zinc and steel to form more dross.
I am now feeding my rainbow trout at -12 °F.
Regards,
Galvanizing Consultant - Hot Springs, South Dakota, USA
Q. Low fuming fluxes seem to come is several varieties, and my research so far uncovers that perhaps 25% of UK galvanizers (15 plants) are using one or other of these fluxes, with no bag filter for fume filtration. There is extraction, but this vents to atmosphere and apparently still meets environmental limits (15 mg/m3).
Not all of them contain potassium chloride in place of ammonium, but I'm not sure yet of the actual formulation. One supplier is TIB Chemicals from Germany, who have offered Low Fuming Flux for over 30 years they claim.
At least 5 of these are also using a zinc recovery device (MZR or similar - others are available).
I have only heard of one general galvanizer running such high Al (0.2%) as quoted above, and that was an accident. Very often high Al% results in black spots. A more normal level is 0.001 - 0.002%.
I asked about non-reactive steel, and no one had thought about this at all, suggesting this isn't an issue. But then Si killed steels are far more common here than Al killed, so perhaps we don't see so much non-reactive steel.
On kettle life: there are two determinants on life:
1. Erosion of the kettle wall so that it eventually gets thin enough to be mechanically unsafe and needs to be changed. This is what everyone focuses on.
2 Increased risk of cracking due to thermal cycling. This used never to be an issue, with typical life being 10-12 years, but now with kettles going beyond 12 years, that risk increases and can be the determinant of end of life. While examples of severe cracks have been seen, I haven't heard of a failure yet due to cracking, though when one happens it will likely be dramatic. Unlike a wear hole (leak), where the flow of zinc out the kettle through the hole, is typically small, a crack could open up huge holes and the loss of zinc containment could be "very exciting".
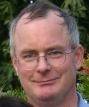
Geoff Crowley
Crithwood Ltd.
Westfield, Scotland, UK
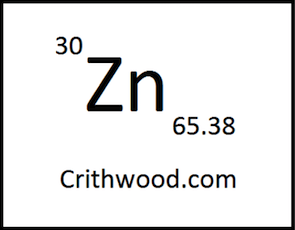
March 5, 2019
A. Certainly I was NOT Recommending 0.2% Aluminum in the zinc. I was merely stating what is in the patent, showing that the inventor did not know hot dip galvanizing well. Your figures for Al in zinc are the same as mine. I have located a galvanizer using 2% KCl in his otherwise regular flux. I am trying to get more details. It may be that he has 1% or 2% HCl in his flux which equates to pH 1 or 2.
Regards,
Galvanizing Consultant - Hot Springs, South Dakota, USA
Q, A, or Comment on THIS thread -or- Start a NEW Thread