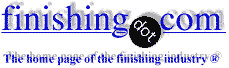
-----
Corrosion Protection for Steel Hub Running in a Bronze Bushing
Q. My application is an 1.5" diameter Steel Hub Rotating in an Oil Impregnated Bronze Bushing. The environment is a golf course which includes water, salt, sand, fertilizer chemicals, and sun. The steel hub is growing enough rust in between uses to fill the void between the bushing and hub which seizes it solid. I need a coating or plating for the steel with great corrosion protection but that won't flake or gum up the pores of the bronze bushing. If coating is too soft it will load up bushing and not allow the oil to wick out when needed. Growth or buildup of the coating is not a problem as long as it is consistent. We make the hubs in house and can shrink or grow the diameter of the steel to compensate for the plating/coating thickness. We are using 1215 steel for the hub, so if there is a recommendation for a better steel that is machinable, I am willing to try. However, Stainless is not recommended because it clogs pores in the bushing. Once we get this figured out, our annual usage will be 1,500 to 2,000 per year. Willing to consider any type of metal plating/coating/epoxy/or heat treating available. Looking forward to your ideas!
Brad EverettProduction Manager - Missouri
August 11, 2016
A. Hi Brad. You are trying to find something that is resistant to abrasive wear from sand and chemically corrosion resistant, and which won't galvanically corrode despite salt, fertilizer, and dampness. Although electroless nickel plating might suffice, I think it might be more practical to exclude the environment from the rotating joint areas rather than trying to make the rotating joint materials resistant to such an environment; so ... are you sure a sealed bearing or seals of some sort are impractical?
Regards,
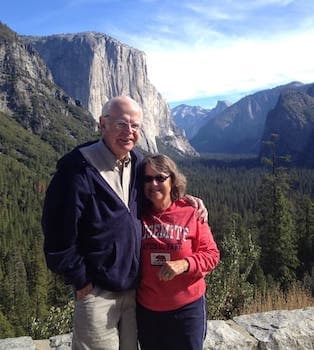
Ted Mooney, P.E. RET
Striving to live Aloha
(Ted can offer longterm or instant help)
finishing.com - Pine Beach, New Jersey
August 2016
A. Sealed bearings is certainly one way to go.
I would take a look at some of the engineered plastics. One company that I am familiar with and has an engineering staff is IGUS. A German company with offices in the USA. I am sure that there are others out there, but this is the only one that I am familiar with. They have a large web site.
- Navarre, Florida
August 12, 2016
Q. Thank you for your input. I really appreciate any and all help/advice with this.
Originally, we added a grease zerk to the bushing to make it re-greaseable. As long as the customer daily purged the bushing with clean grease, it would help immensely. However, that was very messy and courses do not want spots of grease on their golf greens where the equipment is used. Even food grade grease is not good on golf turf. So most people did not purge the grease enough. Then the grease holds the sand in and creates a rubbing compound which causes excessive wear counteracting the purpose of the grease.
We looked into dry applications with various materials. We tested hubs made of 6061 Aluminum, Hard Coat Anodized Aluminum, 1018 and 1215 Steel. We tested those with greased oilite bronze, dry oilite bronze, and 2 different IGUS recommended plastic bushings. The plastic bushings had excessive wear. The best results were with non-greased oilite bronze bushing and steel hubs. We also tried several different methods of sealing the area from sand and debris including up to triple lip seals. However, water and sand always made its way in. All golf course are different. But some of them have extremely corrosive turf due to chemical fertilizers, salt, water and sand. Plus the equipment induces some vibration which seems to help let debris in even the smallest areas. Because of this we went with this configuration hoping that since we can't stop debris from getting in, at least we can let if flow or fall back out and not get trapped causing more wear.
Testing has shown this method works well as far as wear, but still have the corrosion issue. Please hit me with any questions or advice. thanks
- st. louis, Missouri usa
August 12, 2016
A. Good day to all.
Just came to my mind what about using Babbitt or silver bushing?
Good luck
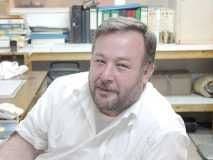
Khair Shishani
aircraft maintenance - Al Ain, UAE
August 29, 2016
Q, A, or Comment on THIS thread -or- Start a NEW Thread