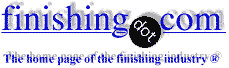
-----
Coating for Heat Radiation from Molten Metal
Q. I intend to construct a panel which can absorb high temperature radiation from molten metal. The panels are to be held within 3 meters of heat source. Panels are to be made of steel. What is to be used as high absorptivity and low emissivity coating? The coating should withstand temperature above 450 °C and abrasion of fumes and gases.
Sudhindra Senguptaproduct designer - Kolkata,West Bengal, India
June 26, 2016
A. Perhaps you should look into what they use to coat solar panels. The requirements seem similar.
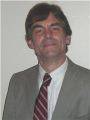
Dave Wichern
Consultant - The Bronx, New York
June 28, 2016
A. I would suggest first sand blast to reduce reflectivity followed by black oxide finish.
Remember that anything that absorbs heat will also emit.
I don't know of any one-way coatings. Unless you remove the heat from the back of the panel it will simply get hot.
Is this a heat shield or are you aiming to use the heat absorbed?
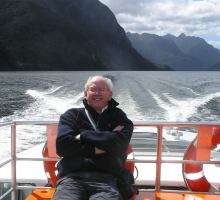
Geoff Smith
Hampshire, England
June 29, 2016
Q. Thank you Dave. I have heard of Thermalox 250,coating used for solar application but do not know whether this will peel off from steel surface at 450 °C. Information is requested.
Thanks Geoff. It is not a heat shield. The device should absorb heat for reuse. Flow channels will be formed on the plate by welding steel tubes for Thermic Fluid circulation. If the coating stays at 450 °C, the tubes will also be quoted and will be welded to front side of plate otherwise the tubes will be on back side. Hot Thermic Fluid will be stored in insulated tank and be pumped to point of reuse, i.e., jacketed pitch melting tank. Thermalox has much lower emissivity compared to its absorptivity.
Regards,
Sudhindra
- Kolkata,West Bengal, India
June 29, 2016
![]() |
A. I second what Mr. Smith said. ![]() Dave Wichern Consultant - The Bronx, New York June 30, 2016 It is not clear as to what exactly you are trying to do though your application appears to be similar to concentrated solar collectors where the the collector can attain pretty high temperatures. Plenty of published literature is available for such collectors. Generally incident radiation would be at lower wavelengths corresponding to source temperature while the collector emits at longer wavelengths corresponding to its temperature which would be lower than that of the source. Coatings are designed to have high absorption at lower wave lengths and low emission at longer wavelengths. Adhesion, temperature stability etc are other important issues. Such coatings are generally applied by PVD techniques. H.R. PrabhkaraBangalore Plasmatek - Bangalore, Karnataka, India June 30, 2016 Hi Sudindra ![]() Geoff Smith Hampshire, England June 30, 2016 |
Q, A, or Comment on THIS thread -or- Start a NEW Thread