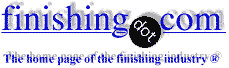
-----
Problems in Electroless Nickel Plating
May 11, 2016
Q. Dear Sir ,
First of all let me introduce myself. I am Joseba Ibañez and I am a young Spanish process engineer. I am suffering big problems in our actual electroless nickel process. In order to explain briefly, we use SiO2 to mask from the nickel. Thus the nickel will only deposit in the areas where there is not oxide at all.
As we work with rough surfaces, I cannot measure the oxide of the surface to know if it maskable. The problem is that the nickel deposits on some oxide wafers and not on others. When I remove the nickel in nitric acid, then I can see the oxide lines (visually they are identical to the ones that really mask the nickel, but unfortunately there is no way to measure the thickness in our actual reflectometer as it is a rough surface). Once it is nickeled there is nothing we can do, no reworks are possible anymore.
Have you ever heard of such a problem?
I would greatly appreciate your opinion on this.
Thanks a million! Have a nice day,
Joseba
Process Engineer - Spain
A. Hello Joseba, If you have had success using this maskant in the past and this is a new dilemma, I would first examine the maskant under magnification to see if there are any voids in the mask. Electroless nickel needs a host site to deposit. I would also make sure that the EN bath is not too active. High bath activity can result when improper ph, elevated temp, or bath chemicals are out of whack. You will also see very high bath activity if the tank needs leaching. Getting back to the mask, if there is a way you can perform a cross section to verify you have full coverage of the mask. Even with rough surfaces you can focus in and out on the microscope. Hope this helps and good luck.
Mark BakerProcess Engineering - Phoenix, Arizona USA
May 12, 2016
Q. Thanks a million because of your fast answer...
First of all, I did not see any big changes in the pH of the bath. Actually it is running at 10,02. Would it make sense to make it lower to have lower rates?
I have also precipitation problems in that tank, meaning it is generating a lot of Hydrogen. Is this related to the pH also, am I right? Furthermore, I use ammonia
⇦ on
eBay or
Amazon [affil link] like a buffer and this is basically which gives the pH values, as other reactants are acid. I use Sodium Hypophosphite for the reaction. Working with less sodium Hypophosphite (I cannot see different lectures on the pH as it is much more acid than the ammonia ) I can see the reaction goes lower... AS the dosification of the other tanks are same and I have most of the problems in this located bath, could it be related to the bath itself? Could the bath be damage ? I can see this bath also gets dirtier than the other and this of course does not help me in anything. Does it make sense to change the bath itself to another quartz bath?
Please give me your opinion.
Thanks again and have a nice weekend!
Joseba
- Bilbao, Spain
May 13, 2016
Hello again Joseba, As I mentioned in my first response, if there is a host in the tank such as nickel appearing on tank walls and or heaters it's time to leach the tank to remove that Ni build-up. Ni baths have a certain amount of MTOs (metal turnovers) that limit bath life. Consult your tech data sheet to see what the MTO limit for the bath is. If your bath looks dirty, it most likely is. From your question it sounds like you have another bath on line that works well. When I worked with EN, we would transfer the bath to a newly leached tank every other day, and dump the bath just before we reached the MTO limit.
Mark BakerProcess Engineering - Phoenix, Arizona USA
May 16, 2016
Q, A, or Comment on THIS thread -or- Start a NEW Thread