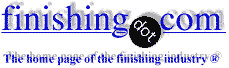
-----
Neither Solder nor Copper Plating Adheres to Nickel Silver
Q. Hello people, the actual problem I'm facing is trying to solder (for electronics) onto a nickel silver piece (the metal clip in breadboards). After lightly cleaning the surface (acetone and IPA), the solder absolutely does not wet. "Prepping" the surface by abrasion/acid dip does not make a difference.
I then attempted to plate copper onto the piece which would hopefully improve the solderability. I cleaned the surface with acetone
⇦ on
eBay
or
Amazon
[affil link] Warning! Flammable!
and IPA as before. Using copper anode in dilute sulfuric acid with the nickel silver piece as the cathode (with hot entry), the copper does not adhere strongly (soldering takes the copper right off). I've tried this at various voltage and current settings, with similar effects.
Is there something that can be done to improve the copper adherence or the solderability of the piece?
Electronics Engineer - London, United Kingdom
March 19, 2016
March 19, 2016
A. Hi Bo
Nickel silver is often called German silver. It is a copper/nickel alloy with possibly some zinc. I have never seen it plated.
Electroplated nickel silver EPNS is a very thin plated layer of silver over nickel.
I have never seen either of these used on standard electronic components.
I would guess that you have a very common nickel plated finish.
Cleaning with solvent will do little to overcome the invisible oxide surface (passivation layer)
Soldering is simple BUT requires a stronger flux than the rosin based types common in electronics. Your solder supplier should be able to provide the answer or you could try B&Q for something stronger.
These fluxes are corrosive if left on the joint so it is usual to wash them off after soldering. Water is usually sufficient.
The passivation layer is also the reason why your plating will not stick unless you use an activation process beyond amateur use.
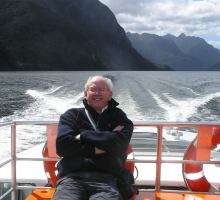
Geoff Smith
Hampshire, England
Q. Hello Geoff,
Thank you for responding. I actually also considered the possibility that the piece is simply nickel plated, and the problem was a layer of oxide. I attempted to dissolve the oxide by dipping the piece in sulfuric acid, but this didn't help.
- London, United Kingdom
March 21, 2016
A. Good day Bo.
Geoff raises a good point about the flux.
Try 7 parts glycerine and 3 parts hydrochloric acid.
I have used this to solder costume jewellery as a variety of base metals.
Hope this helps.
Regards,
Aerotek Mfg. Ltd. - Whitby, Ontario, Canada
March 22, 2016
March 27, 2016
Hello Eric and Geoff,
Thank you for your responses! Instead of trying to make my own flux, I ordered a small amount of flux and it solved my problem.
For reference, the composition given on the flux bottle is:
ZnO: 24%
NH4Cl: 30%
HCl: 6%
C3H3COH: 30%
H2O: 12%
Surfactant: 3%
(Yes, it adds up to 105%...)
- London, United Kingdom
Q, A, or Comment on THIS thread -or- Start a NEW Thread