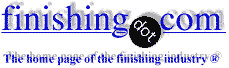
-----
Can anodized parts outgas corrosive sulfur vapors?
Q. Hi,
re: Aluminum part which is Black anodized in sulfuric acid bath.
I would like to know is there any chance that Anodized aluminum can outgas/Evaporate sulfur.
I am seeing some Electrical components/LEDs are getting corroded due to exposure to sulfur. Am suspecting the source of sulfur can be from Anodized aluminum
Regards,
Manju
Product designer - Bangalore , India
February 17, 2016
A. Hi Manju,
Probably need a little more information about the anodizing process, but if you are anodizing castings or welded assemblies it is possible to get sulfuric acid trapped (in pores of a casting or crevices in weldments) and this may be leading to your corrosion issues.
Aerospace - Yeovil, Somerset, UK
February 17, 2016
Q. Hi Brian ,
Thanks for your reply.
Component is extruded aluminum, there is no welding. Component has 4 holes (drilling operation).
Anodising tank consists of sulfuric acid with 20% concentration and 80% balance is water.
Before anodising the surface of the article will be thoroughly cleaned, normally using a detergent based process, and etched with a solution. After anodising the surface is coloured by dipping the article in dye tank using appropriate anodising colours and then sealed by placing it in boiling water.
- Bangalore , Karnataka , India
February 18, 2016
![]() |
A. Analyze (EDX) any anodized coating, and you will find sulfur. Personally, I don't think there's any way to avoid it, only minimize it. This is obviously accomplished with adequate and thorough rinsing after anodizing. Proper rinsing is often overlooked when designing an anodizing line. I'm pretty sure rinsing is what Brian was zeroing in on when he asked you questions about your process. If it were me, that would where I would look first, along with the environment that the part is exposed to as an end product. ![]() Marc Green anodizer - Boise, Idaho February 20, 2016 A. Hi Manju, Aerospace - Yeovil, Somerset, UK February 22, 2016 |
A. Any pre-drilled, especially blind, holes in a part can potentially carry sulfuric acid as drag out. A good rinse, then blowing out the holes, then rinsing again before dyeing is important to negate any possibility that unreacted sulfuric acid is present. I have even known line runners to use a very dilute Nitric rinse and then another DI rinse between anodising and dyeing to assist in prevention of sulfuric drag-out and resultant color bleed-out around holes.
If you find that the pH of your black dye tends to drift down over time, rather than up, you're dragging in sulfuric acid.
Also, have you considered doing a mid temperature Nickel acetate seal after dyeing? This is an excellent choice for dyed parts.
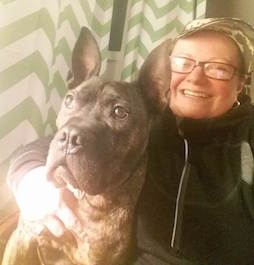
Rachel Mackintosh
lab rat - Greenfield, Vermont
April 29, 2016
Q, A, or Comment on THIS thread -or- Start a NEW Thread