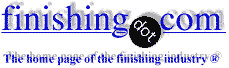
-----
What thickness of zinc from electrogalvanizing to be appropriate for chromate conversion coating
Q. Dear Sir,
I am a student in a university in the Bangkok. I want to know about, What is the thickness from electrogalvanized process that can be appropriate for chromate conversion coating? Why?
Regards,
student - Bangkok,Thailand
January 25, 2016
January 2016
A. Hi Suvanit. I think chromate conversion coating is appropriate for any and all thicknesses of zinc electroplating. Why would we think different? Please reveal your thinking on the subject instead of posing it so abstractly, and we may be able to flesh out the answer for you. Thanks.
Regards,
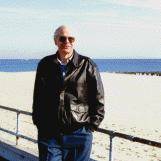
Ted Mooney, P.E.
Striving to live Aloha
(Ted can offer longterm or instant help)
finishing.com - Pine Beach, New Jersey
A. I (for one) am not comfortable with the term 'electrogalvanizing.' The implication is that it is the same in some way as hot dip galvanizing. That is not true; it has significantly less thickness and therefore significantly less corrosion protection than zinc electroplating. Ted is right to call it electroplating, because that is what it is.
"Conversion coating," however, is a meaningful term. It means that the process CONVERTS zinc to a passivate. Therefore, there needs to be enough zinc for the conversion process not to consume all of the zinc. So some conversion processes convert a lot of the zinc, and some convert very little. In general, the more zinc is converted, the thicker the film and the greater the corrosion protection. To give a few examples:
(1) Old hex blue-bright chromates converted very little zinc and offered little corrosion protection. 'Commercial zinc' (i.e., all surfaces were plated) would tolerate a blue-bright.
(2) Black hex chromates (silver black) required a fairly high thickness of zinc; some platers wouldn't do black unless they had five tenths.
(3) Newer 'thick film' trivalent passivates require more zinc thickness than thin film trivalent passivates.
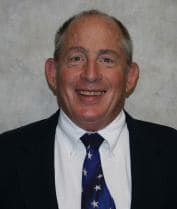
Tom Rochester
CTO - Jackson, Michigan, USA
Plating Systems & Technologies, Inc.

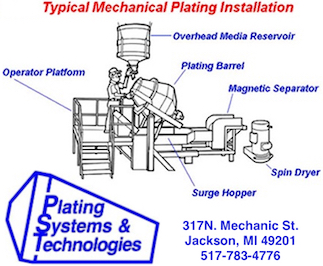
February 18, 2016
Hi Tom. Thanks for the insights that I never thought about and didn't realize! My response to Suvanit was just a reflection of my belief that zinc electroplating is invariably chromate conversion coated regardless of its thickness.
I agree that the term "commercial zinc" was widely used, but I never liked it :-)
Hopefully we're moving completely away from 'commercial zinc' and towards a minimum of ASTM B633 5 micron zinc even for mild exposure. Are you suggesting that if one uses thick film chromates, 5 micron might not be sufficient? -- similar to how it was insufficient for silver-based black chromate (another thing I didn't know!)
Regards,
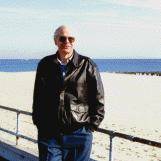
Ted Mooney, P.E.
Striving to live Aloha
(Ted can offer longterm or instant help)
finishing.com - Pine Beach, New Jersey
February 2016
February 26, 2016
Q. Hi Ted Mooney & Tom Rochester
Thanks for the great information! I had more of a question regarding the zinc plating solution with conversion coating.
In my thesis, study of zinc plating on steel prepared from non-cyanide zinc bath and acid zinc bath, when compared with acid zinc solution by salt spray test 24 hours about 2 case.
The first case, sample without conversion coating found that sample from non-cyanide bath has white rust occurrence resistance better than plating by acid zinc bath. Sample that plating by non-cyanide found the white rust at time 1 hour but for the sample that plating by acid zinc found white rust at 30 minutes.
But in the second case, sample that zinc plating with conversion coating solution pH 1.8 has the timing of white rust occurrence of acid zinc plating and conversion coating is more than 7 hours but for the non-cyanide and conversion coating The timing of white rust occurrence is about 4 hours. So acid zinc bath with conversion coating has corrosion resistance more than non-cyanide bath with conversion coating.
I would like to know why pH of coating solution of conversion coating, which came from zinc plating by different plating solution, are different ? And what range of pH of conversion coating solution that suitable for zinc plating from non-cyanide ?
I apologize if there are any errors.
Regards,
- Bangkok,Thailand
Q, A, or Comment on THIS thread -or- Start a NEW Thread