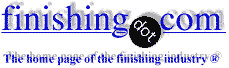
-----
Removal of Tantalum coating (1 mm thickness) from Aluminum process kit
November 30, 2015
Q. Hi, I have some Aluminium process kit which is coated with Tantalum. The thickness range of tantalum coating is from 0.1 mm to 2.5 mm. I have tried various methods to remove the tantalum without much success.
I am only keen to recover the Ta and will sell away the based aluminum as scrap.
Each process kit weighed approximately 11 kg.
Thanks for your suggestion.
Chemist - Singapore
A. YH
Have you tried melting away the aluminum?
- Colorado Springs, Colorado
December 1, 2015
Q. Hi Willie, thanks for your suggestion. I have tried to melt them. Aluminum start to melt at around 700 °C but the Tantalum tend to mix and go to the molten aluminum as well. Putting up a sieve clog the melting process especially the thinner layer (0.1 mm thickness) portion.
I have quenched the process kit ie heating at 500 °C and quenched it immediately in the cool water. Only a fraction of them managed to pealed off from the process kit.
Some guys were suggesting using ultrasonic. What is your opinion?
Thanks again and have a nice day.
Poh
- Singapore
December 2, 2015
A. YH
Your articles look like bowl guards, and if so they are probably textured which makes de-laminating challenging.
If it were me and there was sufficient Ta present, I would strip the aluminum with a caustic solution where melting the aluminum was not a viable option. It would depend on how much Ta is present on each article; if little, the Al value might exceed the Ta.
- Colorado Springs, Colorado
December 3, 2015
Q. Hi Willie
I should be able to get between 2.5 to 3.5 kg of Ta/Al flake per process kit. I think even if the purity of Ta fall to below 80%, it still worth the effort.
All the while I thought Ta also dissolved in caustic soda ⇦liquid caustic soda in bulk on
Amazon [affil link]
or I am wrong.
I put up a simple experiment on the reactivity next week.
Thanks for your suggestion.
Poh
- Singapore
December 4, 2015
A. Perhaps some warm HCl (muriatic acid) cut with one or two volumes of water? This ought to dissolve some of the Al and the Ta will flake off and fall to the bottom.
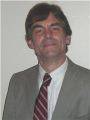
Dave Wichern
Consultant - The Bronx, New York
December 15, 2015
Q. Hi Dave
Thanks for your response.
I have tried to soak it into a 50% NaOH solution and it worked pretty well. All the Ta drops to the bottom of the sink. But I realised that the concentration is too high as the reaction is "explosive" (I mean react violently!) and presently I am playing with the concentration of NaOH just to make it right.
I will try the warm HCl method once I manage to get some HCl. BTW may I know the right concentration to start?
Regards
- Singapore
December 17, 2015
A. Hi. NaOH is widely used to dissolve aluminum without dissolving other materials, and it doesn't have the corrosive fumes of HCl. As long as it works and doesn't dissolve the tantalum, I think it's the better approach. But, since you would like to sell the scrap aluminum rather than completely dissolve it, perhaps you can do cathodic cleaning/dissolution. Try applying 50 ASF current to generate scrubbing hydrogen bubbles to accelerate the tantalum flaking off with less need for dissolving as much aluminum.
Regards,
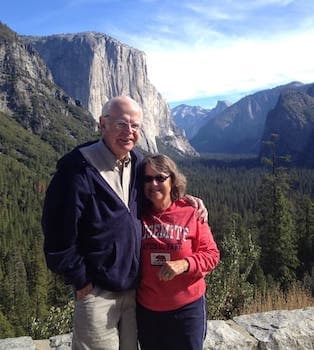
Ted Mooney, P.E. RET
Striving to live Aloha
(Ted can offer longterm or instant help)
finishing.com - Pine Beach, New Jersey
December 2015
Q. Hi Ted
Thanks for your suggestion. To a analytical chemist, cathodic dissolution/cleaning look interesting and I must admit I am totally NOT familiar with it.
Can you tell me or lead me to gather more information on the process? Is the process similar to reversed electroplating (deplating process)? What is the suitable medium and the concentration to start with.
Really appreciate your assistance on the above.
Regards
- Singapore
December 21, 2015
A. Hi again. In the electroplating industry, it is common to do "soak cleaning", which means putting the work into a caustic & detergent mix (there may be various other chemicals in it as well) to remove dirt, oil, and grease. But the effectiveness of the cleaning process can be greatly improved by changing it to "electrocleaning", i.e., applying a (probably 6-12 Volt) DC current of about 50 Amps/square foot to the work, which causes the water in solution to electrolyze into hydrogen gas at the cathode and oxygen gas at the anode. The rapid evolution of hydrogen gas is very effective in scrubbing the dirt away.
So it just strikes me that if you are removing the tantalum by dissolving some of the aluminum and waiting for it to fall off, that the speed of that separation should be greatly accelerated by applying a similar DC current to your caustic soda ⇦liquid caustic soda in bulk on Amazon [affil link] solution.
Regards,
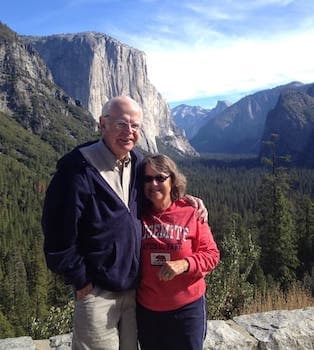
Ted Mooney, P.E. RET
Striving to live Aloha
(Ted can offer longterm or instant help)
finishing.com - Pine Beach, New Jersey
December 2015
Q, A, or Comment on THIS thread -or- Start a NEW Thread