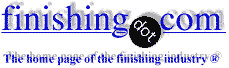
-----
Do possible residuals prohibit running parts from multiple customers in same line?
Q. I am looking for information on the residuals and citric passivation. We have a citric passivation tank that we use to passivate Stainless steel parts. We have validated the line for a certain product line. There is a need to use this same line for multiple product lines, some of which are not manufactured in house. The question is, do we need to be worried about the manufacturing agents used on the various products that would go through this passivation line and the potential for cross contamination? So for example, if we purchase a component from McMaster Carr (no idea of their manufacturing process or agents used) and then passivate it in our validated citric line do we need to worry about potential residuals of manufacturing agents from the McMaster Carr parts cross contaminating with the parts that would be run through the line normally?
Carrie Mauryamanufacturing - Upper Saddle River, New Jersey, USA
November 18, 2015
A. Hi Carrie. That is an interesting question. Some manufacturers contract for metal finishing shops to operate dedicated processing lines for them, and in that case no other parts should be processed in that line. But in the general case of job shops who do contract processing, unless covered in the P.O., I do not think that there is any expectation at all of dedicated process lines.
And, although a measure of concern for cleanroom parts or medical parts might possibly be warranted, the general case is that such process lines contain many steps including cleaning stations which are able to deal with all common contaminants.
I'd love to hear second and third opinions :-)
Regards,
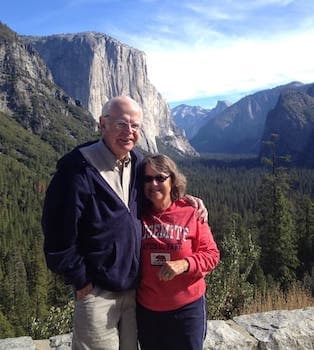
Ted Mooney, P.E. RET
Striving to live Aloha
(Ted can offer longterm or instant help)
finishing.com - Pine Beach, New Jersey
November 2015
November 19, 2015
A. Good day Carrie.
As Ted has indicated,
"process lines contain many steps including cleaning stations which are able to deal with all common contaminants."
We process cadmium plating, bushings, etc....
These items require lubricants to manufacture, and from lot to lot, I am having difficulty removing the lubricants.
Some are simple mineral oils, some contain paraffin waxes (which is difficult to deal with), and some are really exotic.
Regarding a cleaning process, I request the MSDS of the particular lubricant, in order to discover the nature of the beast.
Hope this helps.
Regards,
Aerotek Mfg. Ltd. - Whitby, Ont., Canada
![]() |
Medical Device - Upper Saddle River, New Jersey, USA November 19, 2015 November 20, 2015 A. Since by definition parts need to be quite clean when entering a passivation bath, if there is any legitimate concern over unknown residues mucking up the bath you should add a precleaning stage. ![]() Ray Kremer Stellar Solutions, Inc. ![]() McHenry, Illinois ![]() |
Good day Carrie.
Ray has given some some insight on cleanliness.
I tend to rely on the water break test for "residuals", to validate the cleaning process. Bear in mind, any alkalinity in the water will show absence of water break. I use a dilute acid to remove the alkalinity, and observe presence/lack of water break. This works for me.
I tend to concentrate on the compositions of the substrates, and monitor the iron content of the baths.
You can get iron from a leaking heating coil, if you are using steam. The copper sulphate
⇦ on
eBay or
Amazon [affil link] test and salt spray testing will also "validate" the process.
Hope this helps.
Regards,
Aerotek Mfg. Ltd. - Whitby, Ont., Canada.
Q, A, or Comment on THIS thread -or- Start a NEW Thread