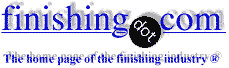
-----
Skipping HCl before Galvanizing
October 1, 2015
Q. I have a technical question and am hoping to get some feedback from here.
Basically, zinc Electro-Galvanized (EG) steel coil is being used to produce steel pipe. The EG coil is roll-formed and then goes through high frequency Electrical Resistance Welding(ERW) welding to form pipe.
Then the formed pipe goes into the galvanizing bath.
My Question is:
Theoretically, the hydrochloric acid pickling process is not needed?
I do not want to use hydrochloric acid in galvanizing the already electro-galvanized steel metal surface. But the reality is when not using hydrochloric acid, the "electrical resistance welded area" will not be galvanized . There is a line of "bare spot" as the welding line is not galvanized.
I have tried using the wire brush to clean the welding line before galvanizing but the "bare spot" of the line is still there. At the end of the day, hydrochloric acid is needed to pickle for the electro-galvanized steel surface to be galvanized again.
Anyone can share their opinion? Really appreciate it. Thanks.
- Butterworth, Penang, Malaysia
A. Can you explain what you mean by "electro galvanizing"?
Do you mean galvanizing or electroplating? Or something else?
Generally the HCl in galvanizing cleans the steel of oxides. Other acids can also be used. The acid reacts for iron oxides (several different forms) to form iron chloride. The acid has an inhibitor to prevent (or greatly reduce) the tendency of the acid to dissolve the steel also.
Galvanizing is an alloying reaction between zinc and iron to form alloys of iron/zinc. If the zinc cannot get to the clean iron surface, then there's no reaction. Oxides will prevent galvanizing.
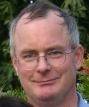
Geoff Crowley
Crithwood Ltd.
Westfield, Scotland, UK
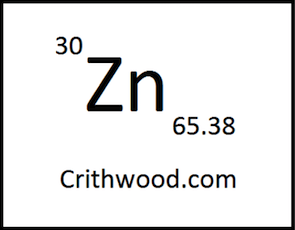
October 26, 2015
Q. When I mentioned "electro galvanizing ", I meant the coil used for making the pipe were already "coated with zinc by the electrolytic galvanizing process .
It simply means that the coil (steel strip) has already been galvanized once, by "electrolytic galvanizing process".
I am not sure if "electrolytic galvanizing process" is equal to "electroplating"?
Regardless, in my mind, I am thinking that since the coil(steel strip) has already been galvanized (electrolytic galvanizing process) before. Why is HCl needed to clean the surface before it goes into zinc bath for galvanizing?
Can the HCl be skipped ?
- Butterworth, Penang, Malaysia
October 27, 2015
by NACE
[only rarely available]
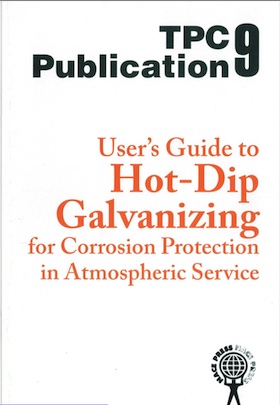
on eBay or Amazon
or AbeBooks
(affil link)
A. Hi John. I understand that you use pre-galvanized strip, that you roll into a cylinder and weld the seam to make it into pipe. But are finding that along the weld lines the hot dip galvanizing isn't taking properly unless you dip the pipe in HCl. So you are asking how to make the process work without the HCl dip, if possible.
It is possible to electroplate onto steel without an acid dip if you sandblast it first; although I don't know much about galvanizing, I think that would work. But wirebrushing does not get the surface clean enough for metallurgical operations like electroplating or hot-dip galvanizing: you need clean bare metal.
For that reason I do not like the idea of trying to hot-dip galvanize your pregalvanized surface without an acid dip because the process does not strike me as robust. It has apparently delivered acceptable results for you in your limited testing, but I think that from time to time you will encounter steel that is dirty or inactive and you will start having splotchy rejects. But it you are convinced that the process is good except for the weld line, you could try sandblasting that weld line in lieu of the acid dip. Good luck.
Regards,
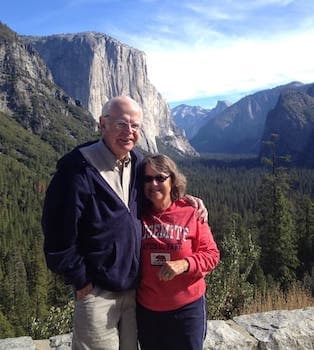
Ted Mooney, P.E. RET
Striving to live Aloha
(Ted can offer longterm or instant help)
finishing.com - Pine Beach, New Jersey
October 2015
October 27, 2015
A. Hi John
I am rather puzzled why you start with galvanised strip. Unless I have missed something,starting with bare steel would be cheaper, avoid zinc fumes in welding and not add any additional stages to the hot dip process.
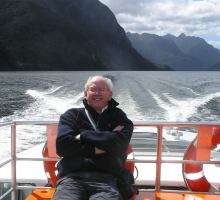
Geoff Smith
Hampshire, England
Q. Dear Geoff Smith,
Sometimes, bare steel (raw materials) would not arrive on time .
Dear Ted Mooney,
Yes, you rephrased my situations perfectly. To just sand-blast the weld line is a good idea which I might test.
Having said that, I am just wondering if anyone could explain maybe in term of metallurgy why the weld line has to be pickled by HCl?
Is it because of the high frequency welding that melts the steel and sort of creating "new grade of steel" which requires the process of HCl pickling to make galvanizing work?
- Butterworth, Penang, Malaysia
October 27, 2015
October 2015
A. Hi John. Welding greatly raises the temperature of the metal such that it destroys the pre-galvanizing, and the underlying steel reacts with oxygen and moisture in the air to form a rust/oxide/scale on the surface. HCl is usually used not just for welded areas, but on the whole surface, to dissolve rusts/oxides/scales so the kettle zinc can react directly with the steel. The alloying process at the zinc-to-steel interface does not work if there is a layer of scale in between them; and even if it did marginally work, you would not have proper adhesion.
Regards,
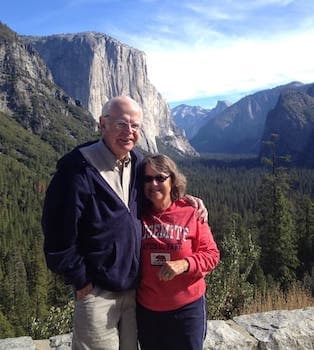
Ted Mooney, P.E. RET
Striving to live Aloha
(Ted can offer longterm or instant help)
finishing.com - Pine Beach, New Jersey
October 28, 2015
I don't think there is any such thing as "electrolytic galvanizing", (but I could be wrong)
Welding after galvanizing always burns off the galv in the heat affected zone of the weld.
You cannot galvanize onto zinc coated material. Galvanizing is a metallurgical alloying reaction between zinc and iron. It doesn't happen between zinc and zinc.
Its not like painting where one layer can be added onto another layer.
I suspect that if you are trying to weld pre-galvanized sheet which is formed into tubes, then trying to galvanize it after forming, that the HCl is stripping off the old galv left after welding, and re-galvanizing the newly cleaned steel.
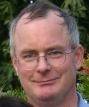
Geoff Crowley
Crithwood Ltd.
Westfield, Scotland, UK
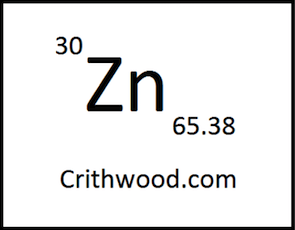
October 29, 2015
Q. Dear Ted,
You are suggesting that scale is formed at faster rate which requires HCL pickling or sand blasting. Understood.
Dear Geoff Crowley ,
You are correct in saying I am galvanizing the pre-galvanized sheet (or known as coil). In terms of how well or the effectiveness of zinc-to-zinc bond together metallurgically, I am unsure .
For "electrolytic galvanizing", you could research more. But my understanding is the process utilizes electrons to somehow galvanize the steel, but the zinc coating is quite thin.
One more question:
Is it not possible to have zinc to zinc bonding metallurgically? Even If I go for hot-dip galvanizing for a steel product, I could hot-dip galvanize again, right?
- Butterworth, Penang, Malaysia
A. Hi John. Yes, the term "electrogalvanizing" has been used by some people to mean zinc electroplating. I personally dislike the term because it is so often used in consumer industries for the purpose of obfuscation -- i.e., people want to offer fasteners with cheaper and much thinner zinc electroplated coatings but get away with having them confused with the more expensive and corrosion resistant hot-dip galvanized fasteners ... so they call them "electrogalvanized" or "galvanized" :-)
Dipping zinc plated steel into a hot-dip galvanizing tank is not how galvanizing is traditionally done. I think you have found that you can make it work well enough to get away with it in the short term. But whether you can reliably provide good coatings this way is another issue. I'd like to hear from others about whether they've tried it, but in the meanwhile I continue to lean towards believing that it is not a robust process. But good luck with it.
Regards,
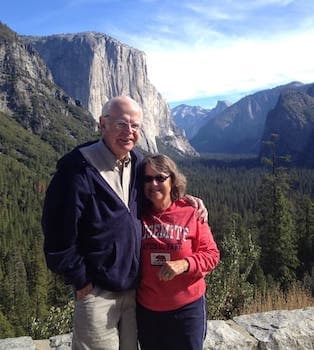
Ted Mooney, P.E. RET
Striving to live Aloha
(Ted can offer longterm or instant help)
finishing.com - Pine Beach, New Jersey
November 2015
Q, A, or Comment on THIS thread -or- Start a NEW Thread