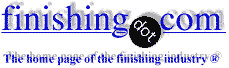
-----
Potential Uses for Gold Scavenger Chemistry?
August 21, 2015
Q. My name is Mahmoud Ahmadi, and I am a PhD student in Chemical engineering. We developed a new technology (patent app in process) for tuning a metal scavenging chemistry to cost effectively capture high value metals in low ppm and ppb concentrations from aqueous solution (gold, palladium).
To validate our technology we need to get input from industry experts. Since gold electroplating and refining cause gradual loss of gold in waste effluent, I wanted to ask if it would be possible for experts to share their thoughts and advice regarding where our technology might fit in .
Thank you for the time and help,
Regards,
- Buffalo, New York, USA
A. Hi Mahmoud.
What I can perhaps do is tell you what is often done in gold plating shops so that you can see where/how your chemistry fits or doesn't. The most common approach in gold electroplating is probably to have recirculating rinses following the plating step, with the rinsewater recirculating through canisters of ion exchange resin. When the resin capacity is exhausted, the canisters are usually shipped to a refinery to be burned to recover the gold values, and a new canister with fresh resin fitted up. So, as food for thought, you can see the cost & waste involved in this approach, but the simplicity & practicality as well.
Sorry, but I removed your e-mail address and request for private contact; the site is for public discussions, and we would drown in spam overnight if we did differently. Apologies. Good luck.
Regards,
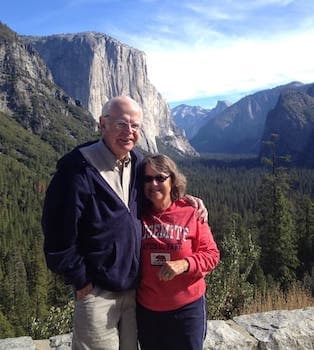
Ted Mooney, P.E. RET
Striving to live Aloha
(Ted can offer longterm or instant help)
finishing.com - Pine Beach, New Jersey
August 2015
August 21, 2015
Q. Dear Ted,
Thanks for the reply and help. I have been searching this topic for last 5 weeks and here is what I have learned; process: after the plating bath (to which almost all using a cyanide complex), there is a "drag out" bath (also called a "dead rinse" bath) that contains about 10% of the metal in the primary plating bath. A "gold bug" elecrowinning process is then used here to reduce the gold content of the bath to 5-20 ppm (the recovered gold is being sold to a metal refiner). Then the waste steam is exposed to a "running rinse" which dilutes the gold content to ~ a quarter of the concentration in the drag out tank. Ion exchange is used to then collect the cyanide-metal complex. For gold, the saturated ion exchange resin (filled with the gold-cyanide complex) is not regenerated but instead the saturated bed is sold to a refiner who incinerates the resin and collects the gold. With gold, this process is profitable such that the refiner can obtain money for the gold waste provided to the refiner. However, for silver, the process only allows about a breakeven prospect. After ion exchange, the remaining stream is pH adjusted basic to generate metal hydroxides which are then filtered out and sold to other refiners or smelters. But still 70-100 ppb gold remain into drain stream.
So, I am wondering if industries are interested to upgrading this process by adding a supplementary unit to maximize their recovery or not; something like a final polishing-step to reclaim gold or remove metal to meet EPA regulation.
Thanks,
- Buffalo, New York, USA
A. Hi again. There are sulfite and citrate gold baths and other specialty gold plating baths, and also electroless gold baths and immersion gold baths, especially in the electronics field. So, while I think it is true that most are cyanide based, "almost all" is perhaps an exaggeration.
The Gold Bug or other electrolytic recovery systems are indeed common as a first step, but I don't think I agree about a "running rinse" being the next step. Usually, the rinse water is constantly recirculated through the ion exchange rather than being a once-through running rinse.
I hope that some other readers will jump into this discussion to flesh out the operations and the opportunities and explain how their operation may differ from what we've described, and to fill us both in on how they perceive their needs.
Meanwhile though, everybody everywhere is interested in maximizing their recovery if you offer a practical and cost-effective solution, but I think you need to enunciate how that would be done, rather than just soliciting general interest in maximizing recovery & saving money. I was away for 4 days last week and came home to 1,476 e-mails with offers to save me money -- and I'm sure everyone else encounters similar stuff. So if I ran a gold plating shop I probably would not pull teeth to investigate no. 1,477 but might be willing to read a quick synopsis :-)
Best of Luck, and Regards,
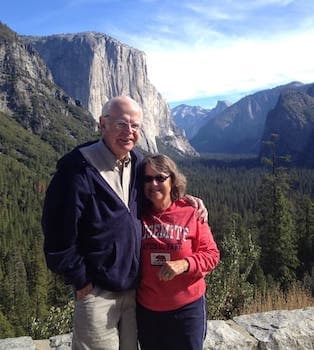
Ted Mooney, P.E. RET
Striving to live Aloha
(Ted can offer longterm or instant help)
finishing.com - Pine Beach, New Jersey
August 2015
Q, A, or Comment on THIS thread -or- Start a NEW Thread