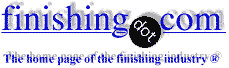
-----
Calculating required aluminum anodizing time

for Shops, Specifiers & Engineers
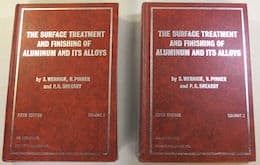
avail from eBay, AbeBooks, or Amazon
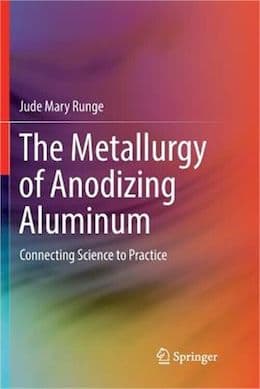
avail from eBay, AbeBooks, or Amazon
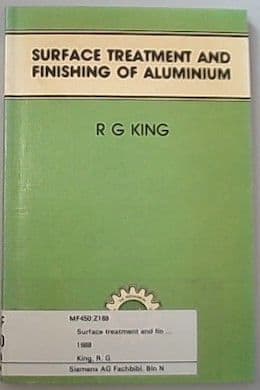
avail from eBay, AbeBooks, or Amazon
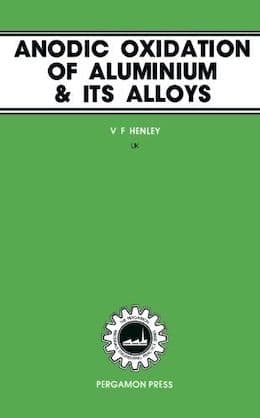
avail from eBay, AbeBooks, or Amazon
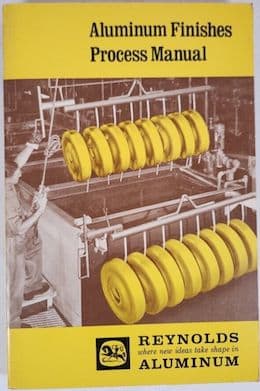
avail from eBay, AbeBooks or Amazon
(as an Amazon Associate & eBay Partner, we earn from qualifying purchases)
Q. Marc,
Let me start out with what will become obvious with this question, the fact that I am very much a novice to this.
Curious if you are using an Eddy Current Meter
⇦ on
eBay
or
Amazon [affil link] to measure the thickness of an anodized surface how does that help with determining the initial time needed to create a particular thickness? If you're anodizing an object (say a lower receiver on a rifle) and you pull it from the anodizing process to check the built up surface at a given time, if it is not the desired thickness at that point can you just re-submerge the object and continue the process?
- Charlotte, North Carolina
January 4, 2024
A. Hi M,
You should not have to pull a part to check thickness often or repeatedly if you do the calculations that have been discussed. I suspect from the question that you don't know the surface area of the component; measuring the thickness to scale up to how much anodizing time to employ is bad practice because the anodizing film can build differently at different current densities. Rather, what you want to do is determine the area and apply the right current density, not fly blind and see how far you've traveled.
But as long as the part doesn't get dirty, or sit out long enough that it begins to seal itself or the coating have time to morph in some way it should be no problem to do a thickness check in basic anodizing. But recognize that some people use pulse anodizing, and rather exotic current density vs. time programs, so you should try not to form a bad habit.
Readers should recognize that we are talking about anodizing of aluminum though; there are many cases where removing components that are being electroplated (as opposed to being anodized) can create problems.
Luck & Regards,
Ted Mooney, P.E. RET
Striving to live Aloha
(Ted can offer longterm or instant help)
finishing.com - Pine Beach, New Jersey
Q. I get what you are saying, so say I have an object let's say it's 7.7 inches in length with a height of 3.9 inches a width of 1.4 inches. You have roughly a rectangular opening that is roughly .898 wide by 2.553 long on that part. The thickness of the walls of the opening are .0175. How would one arrive at the square inches. Yes I'm not good with math.
M Threlkeld [returning]- Charlotte, North Carolina
January 5, 2024
?
M Threlkeld [returning]- Concord North Carolina
January 10, 2024
A. Hi again M.
You can use a cad program to determine surface area; or if you want to invest in expensive equipment, there are electrical devices that will calculate it for you. But the most basic answer is to buy or borrow from the library a book on surface area of common geometric shapes as I tried to imply by posting a link to Tom Rochester's book. Surface finishing is so completely about surface area that you're just not allowed to not be good at this type of math :-)
As you've seen here so far, and as you'll see from scanning numerous other threads on the site, asking people to do surface area arithmetic for you unfortunately is usually the kiss of death to your thread :-(
Apologies & Regards,
Ted Mooney, P.E. RET
Striving to live Aloha
(Ted can offer longterm or instant help)
finishing.com - Pine Beach, New Jersey
Q. Thanks Ted! Any specific recommendations on good books to get? Thanks again!
M Threlkeld [returning]- Charlotte North Carolina
January 11, 2024
A. Hi again.
If, as an individual and a novice, you are willing to buy a book on the subject then I think Tom's is the best you'll find anywhere because it was written specifically with surface finishing in mind. But if you'd rather avail yourself of a public library first, I'm sure a librarian can point you to a book on surface areas of common geometric shapes. And just googling "find surface area" will lead you to several free on-line sites. Good luck!
Regards,
Ted Mooney, P.E. RET
Striving to live Aloha
(Ted can offer longterm or instant help)
finishing.com - Pine Beach, New Jersey
⇩ Related postings, oldest first ⇩
Q. Hello all,
Not sure why my first posting hasn't been posted yet, but I'll try again.
First, I guess a little about myself... I am a custom painter and hydro-printer. I'm looking to expand my horizons with powder-coating and anodizing, anodizing being in the forefront. I have been trying to do my due diligence with researching stuff first, but I did still manage to come up with some questions that I may have either over-looked, or misunderstood.
Please excuse my sporadic-ness I have several questions and I want to get them down before I forget. I will TRY my best to post all questions together, but info or a statement may work its way into a question.
I'm trying to wrap my head around the 720 formula, (I'm having a brain fart for some reason or perhaps just over-analyzing things as usual), alas the power supply I'm looking to use is a 110V, 0-10amp, 0-30V unit.
I've done quite a bit of reading and seem to have come across either conflicting info, or info with insufficient supporting data.
Questions:
1. I've seen several posts/videos of people anodizing for an hour or 2 hours at a time... is that necessary? Whereas I've seen posts regarding the 720 rule where anodizing can be done in as little as 25 minutes. If I'm anodizing a 13" barrel and say a 2"W x 8"L milled alum frame/housing (think of a pistol) what would be my appropriate time to anodize with my proposed power supply, (0-10 amps, 0-30V)?
2. What is the purpose / benefit of building the different microns/mils of oxide? What purposes/factors constitute the varying thickness?
3. My main object/s I'll be anodizing would be tubes or barrels and gun parts, with other small parts and am wondering what would be the "correct" or "ideal" mil build that I would want for said parts. Again, almost all of my projects would be for show purposes, and I plan to dye most of these parts.
4. Can tanks (HPA, CO2, Scuba) be anodized? Unpressurized of course, but I've seen bits and pieces of info regarding strength fatigue, but would a simple 1-time anodizing and dyeing application really jeopardize the strength of a tank that much? Granted the tanks I'm personally referring to would be in the 3000-4800 psi range.
5. How long can I expect my anodizing solution to keep? Assuming I'm using a 5 gal bucket, or 18 gal tub? More than likely the 18 gal tub, and doing perhaps 1 to 2 guns a week.
6. Lastly, I've read several times where the anodizing solution should be kept rather cool, in the low 70F's, assuming this is correct how do you propose I keep the solution cool without using a chiller? Can cold water be safely added to the solution? Perhaps pumped in cool air? Are you guys using something different?
Thanks in advance for all you advice, and guidance, I have done LOTS of reading and watched many videos, but sometimes a question still arises.
Hobbyist - Clearwater, Florida
August 13, 2015
A. Hi Patrick or "Rodger": your first letter was not posted because you used a fictitious name, declined to provide your city, and mistyped your email address -- our reply mail bounced and there was no way to reach you about it :-)
1. The reason for varying anodizing times is chiefly to obtain varying anodizing thickness as addressed in your next question. But tell us the surface area you want to anodize, and remember that it may be inappropriate to anodize that barrel and milled frame simultaneously if they might be a different alloy. Also note that some hobbyists anodize at a lower current density than professionals employ, which is usually about 12 ASF. Voltage will depend upon the alloy and will likely be between 12V and 20V.
2 & 3. There are many reasons for different anodizing thicknesses. In addition to corrosion resistance and wear resistance issues, you might need thick anodizing of maybe 0.0006" to get dye saturation for black and very dark colors (you can't get enough dye into the pores of a thin coating for good saturation) and you might want thin anodized coatings of 0.0001" if you are trying to retain high reflectivity. But I imagine that 0.0002" to 0.0003" would be typical for your needs.
4. Our search engine will find you a few threads about scuba tanks; but I doubt that they can be safely anodized.
5. One of the marks of most professional anodizers is that they seek "equilibrium processes", i.e., processes that can be run continuously and are never dumped nor exhausted. Although not always fully obtainable, the aim is for the anodizing solution to last forever.
6. Probably 68-70 °F rather than low 70's. A chiller is the right way to go, but some people use ice. And if you use a large tank, small parts, and thin coatings, you might be able to get away without a chiller or cooling coil. Good luck.
Regards,
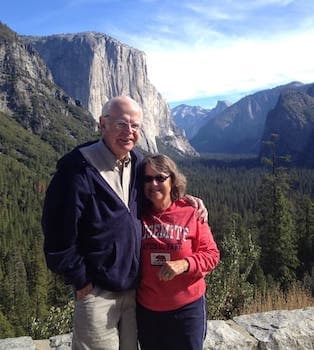
Ted Mooney, P.E. RET
Striving to live Aloha
(Ted can offer longterm or instant help)
finishing.com - Pine Beach, New Jersey
Q. Thanks Ted, I will search for the scuba tanks thread when I have a free moment. Can you please help me understand the 720 rule for my application with the listed power supply and projects that I am working on? What would I need for the 3 mil application and the 6 mil application for black?
Patrick johnson- Clearwater Florida usa
![]() |
A. To expand a little on what Ted has said, and to help you out a little using the 720 rule (which should be used as a guideline), let's use just your 13" gun barrel as an example. For the sake of ease, lets say it's a big gun, and the diameter of the barrel is 1". ![]() Marc Green anodizer - Boise, Idaho Q. Thank you Ted, - Clearwater Florida USA |
A. Hi Patrick. Hopefully someone will review your questions and help. In fact, Marc's response, which crossed in the mail with your question, answers nearly all of it for you, but ...
1. Not at all.
2. Sorry, don't know offhand, but doubt it: aircraft grade often means stronger alloys like 2XXX and 7XXX.
3. Anodizing is done at about 12-18 volts but because I don't know answer 2, I can't suggest 3.
4. Please do a calc on 10% by volume vs. 16% by weight and let me know how far off we are, as I think that's the explanation.
5. I'd have to get back to you. But do you have a good anodizing book? A forum like this can point you to good resources, and can also provide answers to highly specific questions, but it is not organized in tutorial fashion like books are, and it makes for a poor imitation of a book. Most of your questions are surely already answered somewhere in the 50,000 pages of this site, but not in anything even resembling a proper tutorial way :-)
6. Re. aluminum cathodes vs. lead cathodes, the question has already been asked in this forum a half dozen times and received several dozen perspectives, try the search engine. I could answer "aluminum" only by disrespecting a half dozen of my betters, or I could say "lead" and insult a different half dozen of them :-) You need to find those threads and decide for yourself.
In the meantime happy searching, but you'll learn the basics faster by leafing through a book than by searching the site, because bouncing back & forth between info you already know and have read dozens of times, and info you don't yet have the grounding to understand is an inefficient way to learn.
Good luck and regards,
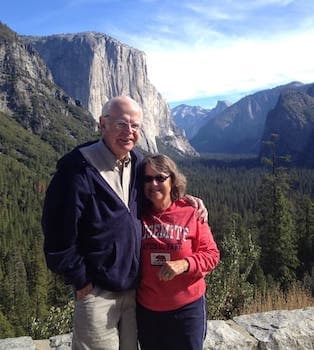
Ted Mooney, P.E. RET
Striving to live Aloha
(Ted can offer longterm or instant help)
finishing.com - Pine Beach, New Jersey
A. 1. Ted is correct: "not at all". Keep in mind, you're adding cathode plates, not anode plates. In anodizing, your work is the anode.
2. Typically aircraft grade is a 7000 series, and a lot of gun parts are as well ... but that is not for certain.
3. You should not need more than 25-30 volts for what you're trying to achieve. Hard anodizing would require more voltage.
4. Higher acid concentrations tend to lead to larger pores, which in turn, would accept dyes a little better. You should play around with different concentrations to see what works best for you.
5. In industry a 3:1 (your work surface area to your cathode surface area) ratio is used. You'll want to place your cathode bars on both side of your "tank" for even coating thickness.
6. General consensus is that Al cathodes are better. They are a better conductor than lead. The downside to Al is that they will eventually need to be replaced, due to the fact that they will erode over time. You can extend the life of them by removing them from your acid solution when not in use. And no, they will not anodize. I think either one of the materials would work just fine for your application.
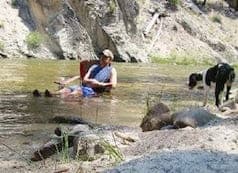
Marc Green
anodizer - Boise, Idaho
Q, A, or Comment on THIS thread -or- Start a NEW Thread