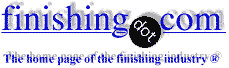
-----
Anodize did not penetrate scratches of brush finish
March 11, 2015
Q. 6063 aluminum extrusion with brush finish was anodized using two-step electrolytic anodizing process whereby the colorant is an inorganic metal salt, not an organic dye. This is a sulfuric acid process that includes sealing using nickel acetate. No etching was done beforehand, although the part was cleaned beforehand, as is always done before anodizing. As can be seen in the photo, the anodizing did not penetrate the scratches that constitute the brush finish. What went wrong?
Thank you.
Sincerely,
Robert
Customer of local anodizing shop - Victor, New York, USA
March 26, 2015
A. We used to have similar problems while anodizing brushed panels and later dyeing in black or any other color. Our solution is rather low tech. We do a light degreasing in a caustic solution, anodize for 3-4^minutes at room temperature, do a light caustic wash again, neutralize and then proceed for either Type II or Type III anodizing and dyeing. Never faced a problem again. I hope it works for you too.
Only make sure the aluminum surface is brushed using an Aluminum Oxide belt. Brass or steel buffs are a strict no-no as the particles embed into the soft aluminum surface and are difficult to remove if not impossible unless the surface is milled again.
Anodizing and re-anodizing might slightly vary surface dimensions and luster.
- Mumbai, Maharashtra, India
March 27, 2015
Q. Hi Winston,
Thank you for your very informative reply.
One question though: what do you mean by "anodize for 3-4 at room temperature"? Anodize for 3 to 4 minutes at room temperature?
Thanks.
Robert
- Victor, New York, USA
![]() |
A. Hi Robert, let me educate you a little bit about anodizing. It's aluminum oxide that is "grown" under a controlled process. Like most coatings, sharp edges are detrimental to coating continuity and uniformity. In a sense, what you're creating with a bushed finish is long grooves with very sharp edges. Anodizing grows perpendicular to the surface substrate, so in the bottom of those grooves, you are not going to get a very good coating. If you were to put a cross section of your part under a S.E.M microscope, you would see that the light colored grooves that appear not to be coated are going to be deeper that the ones that did coat. ![]() Marc Green anodizer - Boise, Idaho March 28, 2015 March 28, 2015 A. I am sorry for the confusion. Yes, I meant 3-4 minutes of anodizing time in Type II. Winston DSouza- Mumbai, Maharashtra, India |
March 29, 2015
Q. Hi Marc and Winston,
Thanks for your messages.
By the way, at the factory that produces the extrusion in question, the extrusion is brushed and then either: (i) painted, which is what I started out with; or (ii) bright dipped, then anodized. In the case of (ii), the anodizing looks great, i.e. it seems to go all the way down to the bottom of the grooves, and so there are no white silvery lines. I suppose that the bright dipping rounds the edges of the grooves sufficiently.
By the way, I wonder if the grooves' sharp edges result in high current density such that the electric field is altered so that very little electrolysis (and thus very little anodizing) takes place in the bottoms of the grooves...
Robert
- Victor, New York, USA
Q, A, or Comment on THIS thread -or- Start a NEW Thread