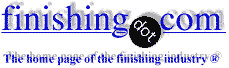
-----
Copper on Copper plating for thermal performance
February 24, 2015
Q. Hi,
I am currently working on an aerospace heat exchanger design for a client and will have a fairly standard copper tube to copper fin arrangement. As part of the design, I am attempting to get to a specific thickness & spacing (let's just say in the order of 0.05" for the fin thickness and spacing) of the arrangement and am considering first brazing the tube to the fins with a high silver type solder (like a 72Ag28Cu) and then plating to final size (the brazed arrangement is about 0.005" undersized). Once the size has been met, the part needs to be (externally) nickel plated for corrosion protection (very thin, in the order of 0.0001").
My question: is this a feasible approach (both function and cost)? What kind of Cu plating bath/process would be preferable (if possible low toxicity & RoHS compliant) and how would I specify this on a manufacturing drawing (ISO or ANSI/ASTM standards)? Anything else I should be considering?
Thanks in advance,
J
Engineer - Santa Fe, New Mexico, USA
A. Hi Joe. Acid copper plating (copper sulphate) ought to be okay. But what I would be concerned about (without seeing a drawing) is getting plating coverage. The plating goes where the current goes and the current follows the path of least resistance (a simplification, but it conveys the idea) ... so depending on the size of the fins, it may be very difficult to get the plating down onto the pipe in between the fins. And wide thickness variation will be a given.
If this were a high volume part, but it probably isn't, jet plating with the jets aimed at the pipe between the fins might work. Even still 0.0001" of nickel plating, even if it were consistent in thickness, would perhaps not be porosity-free and pinhole-free. Hopefully another reader will offer more encouragement :-)
Regards,
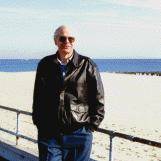
Ted Mooney, P.E.
Striving to live Aloha
(Ted can offer longterm or instant help)
finishing.com - Pine Beach, New Jersey
February 2015
A. Hi Joe
I have never seen a heat exchanger that required such precise dimensions and I doubt it will improve performance; but without much more design information, I accept the problem.
The ability of a plating process to deposit the same thickness on a surface and down holes is called its throwing power. I must disagree with Ted, a standard copper sulphate
⇦ on
eBay or
Amazon [affil link] bath has very poor throwing power. There are two options for copper plating. A standard cyanide based process has good throwing power. Toxicity and ROSH compliance are not a problem. There is nothing but pure copper in the deposit.
The other option is a modified copper sulphate bath as used by the printed circuit industry to achieve even plating in thru-hole PCBs. This requires a proprietary organic additive.
This is an advanced plating application and I would not advise trying to develop your own process. A good technical plating company should be able to advise more clearly when they see the drawings.
My preferred approach would be to stack accurate thickness fins in a jig with ceramic spacers and vacuum braze - job done.
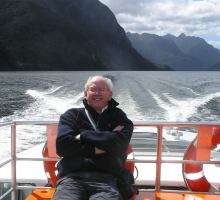
Geoff Smith
Hampshire, England
February 27, 2015
February 24, 2015-- apologies, finishing.com misfiled this reply, and didn't post it until March 7
Q. Thanks for the super prompt reply.
The part is for Aerospace, so some higher-than-usual cost items are acceptable where warranted so the jet plating may be acceptable if that is the way to go for narrow spacing. I'm quite sure the supplier has some form of agitation (air/recirculation?) available but I could perhaps request something specific/additional. The overall size is approx. 150 x 150 x 25 mm.
Regarding the nickel plating, is the thickness the issue or the spacing? I can perhaps allow for a thicker nickel layer (need to re-run the CFD for that) if that is the way to go... if so, what are reasonable values to get good coverage without pinholes? What thickness range is reasonable for copper on copper to get a solid layer of copper to go under the nickel?
Thanks again for the support.
J
- Santa Fe, New Mexico, USA
A. Hello Joe,
I agree with Ted and Geoff. For the nickel, MIL-C-26074
[⇦ this spec on DLA]E Grade B might be a good starting point. This type of nickel (phos) is used for corrosion protection. Grade B is the thinnest allowable nickel coating on copper per the MIL specification. You might get away with .0002" Ni but if you can, Grade B would be much better (.0005" min.). As for the copper, one would use copper cyanide and perhaps specify MIL-C-14550 [link is to free spec spec at Defense Logistics Agency, dla.mil]B Class 2, if I understand your questions correctly. Class 2 calls for 1/2 mil thickness copper coating but the copper plating may not have good coverage down in recessed areas and there could be dogboning and uneven deposits toward the edges of the fins.
Some of the issues can be overcome by a good technical plating shop using jigs, shields, robbers and more but if the copper plating step can be eliminated it may be of some benefit. Another thing to consider are braze joint pinholes and voids. 1/2 mil of copper plating may not be thick enough considering the braze interfaces...but selecting a thicker copper coating will likely increase the coating thickness variations.
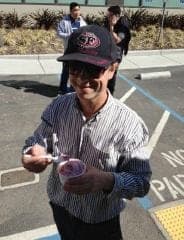
Blake Kneedler
Feather Hollow Eng. - Stockton, California
March 18, 2015
Q, A, or Comment on THIS thread -or- Start a NEW Thread