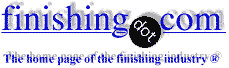
-----
Electroless nickel plating in through-hole structure
October 23, 2014
Q. Hi,
I am currently doing research on electroless nickel plating for through-hole structures (with hole size around 40 µm x 1 µm in rectangular shape), I have tried to use copper super filling method (with additives PEG or SPS independently), but it doesn't help much. It will have a seam in the middle (around 1 µm) as nickel film approaches from both sides.
It would seem the additive leveling agent would help in copper plated through-hole (i.e., JGB), any suggestion for which leveling agent is good for electroless nickel plating? And any comment about getting rid of the seam (may be due to narrow restricted area, lower mass reactant, and product transfer) in the middle as nickel film approaching from adjacent sides?
Anything helps. Thanks.
- san jose, California
![]() |
October 24, 2014 A. I do not think that there is any silver bullet additive for this. - Navarre, Florida October 24, 2014 A. Hello Kevin, Process Engineer - Phoenix, Arizona USA |
October 24, 2014
Q. Thanks for replying and providing useful information for my project.
I still have few more questions:
Would the additives used in copper electroplating such as SPS or PEG (both slow down plating rate in copper electroplating) work for electroless nickel plating or electroless copper plating? As well as other additives such as leveler JGB or BTA and others.
So additives won't work well in electroless plating in comparison to electroplating?
Thanks so much for help.
- san jose California
October 26, 2014
A. I have never used it and have no knowledge of its makeup, but there is an electroless copper made for thru the hole plating of printed wiring boards.
You might try to come up with the EN book from several years back by Hajdu and another big name in EN plating.
Ted might put a link to it here.
- Navarre, Florida
----
Ed. note: Will do, .
July 24, 2018
Q. Electroless nickel plating small 316 stainless steel parts, approx. 1/4" square and .025 thick. There is a .037 hole in the part. We are getting really bad edge build-up but only in the hole. The hole closes up to .035 or less. The plating thickness measures .0003" on the flat surfaces.
Do you think the solution is not flowing into the holes, but is forming a small bubble that dries in the holes? I cannot think of any other cause for such a large edge build-up.
Designer - Elizabethtown, North Carolina USA
Q, A, or Comment on THIS thread -or- Start a NEW Thread