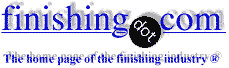
-----
Reduce damage to parting line faces of aluminum molds
Q. I am looking for an economic and relatively simple method to restore dents, pits and other flaws around the parting line surfaces of aluminum slush molds and provide a better surface to reduce the normal damage and wear that is produced during the operation. The molds produce plastic containers and are made of cast aluminum. During process they are filled with resin, closed, put into a furnace (740F) and rotated to melt and spread the resin. Then, they come out of the furnace and are cooled by a water mist. The proposed solution must survive thermal fatigue, corrosion caused by water and resist moderate shock and wear. Actually, they are only TIG welded to fill damages and erosion, re-machined or hand dressed to proper fit and put back to service again.
Some ideas I am considering and plus/cons:
1- Steel inserts (safe, replaceable/complex geometry, 3-D machining of molds to allow space for insert)
2- HVOF of WC, 0.005" (very hard, adequate thickness/expensive, prone to cracks due to lack of support and ductility)
3- HVOF of WC+softer sprayed material (reduced risk of cracking due to impact/expensive, multilayers prone to delamination)
4- HVOF plus a mid-hard plating (reduced risk of delamination and cracks/expensive, slow, limited thickness)
5- Electro spark deposition mid-hard alloy (Excellent adhesion, reduced risk of cracks or delamination/Expensive, very slow, limited thickness)
6- Plating (No heat distortion, several metals available/zincate necessary, slow, limited thickness)
7- Organic hard resins (unknown)
I would appreciate any inputs,
mold engineer - Monterrey, NL, Mexico
June 7, 2014
Q, A, or Comment on THIS thread -or- Start a NEW Thread