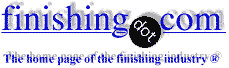
-----
Electroless nickel for EMI/RFI shielding on aluminum
April 22, 2014
Q. I am a technician working on a balloon-borne physics experiment. As part of the experiment, we require our electronics enclosures to be EMI sealed up to 2 Ghz or so. I am not very familiar with electroless nickel and had a few questions. We will be coating aluminum alloys. For a lot of our parts we use the chemfilm/Iridite/Alodine conversion coating, Class 3, but the nickel coating has more wear resistance and we would like to use it on areas where we are extra concerned about a seal. Some of the housings we use come from the supplier with a nickel coating, but we will be custom manufacturing some components and I would like to know what specifications I need to be concerned about.
1) Are there any recommendations on thickness or phosphorous content for this application? We fly our experiment over Antarctica, so I don't believe we are too concerned about corrosion. I don't know if a thicker coating is worse for EMI purposes.
2) I have read that some people recommend first coating the aluminum with copper, is that common?
3) What about electroless nickel and fine threads? One of our panels is about .16" thick with tapped 4-40 through holes in it. Are there any concerns about the threads getting excessive nickel depositing? Should we use an oversized tap first? We also may construct some housings with 2-56 blind holes, does electroless nickel work for those?
Thanks you,
Brian
Student Technician - Honolulu, Hawaii
A. Brian,
1. Why not use copper instead of nickel? That is more common for EMI shielding. P content doesn't matter much but high P (10%) would be fine. For example, airplane landing gear sometimes has very high P content to protect against environmental conditions.
2. Yes, that is common.
3. In my experience, an EMI shielding layer is fairly thick so, yes, the threads should be taken into consideration. One idea is to not plate the threads.
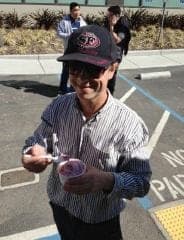
Blake Kneedler
Feather Hollow Eng. - Stockton, California
May 13, 2014
Q, A, or Comment on THIS thread -or- Start a NEW Thread