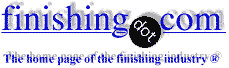
-----
Producing functional acid copper electroplating solution from vinegar
December 13, 2013
Q. Hello,
I'm a French hobbyist who just got started with electroplating, and am attempting to produce a functional plating solution from vinegar
⇦in bulk on
eBay
or
Amazon [affil link] , which has 14% acetic acid , or with a more concentrated solution
⇦ on
eBay
or
Amazon [affil link] , easily found at the chemist's.
The sooty deposit is probably the result of a combination of factors - low acidity, unstable concentration of ions, and too high a current for the ion concentration. Mark, what you say about very low currents not being enough to dissolve ions in the solution because of the lack of chlorine might explain another of my observations - that for a given experiment, the start current (i.e., what I get with a reference voltage), is always lower than in the previous experiment. It seems to indicate the solution cannot replenish itself properly.
I'll continue experimenting -- once again, as a hobbyist, I'm not after industrial quality, and it's much easier to deal with everyday products than to manipulate sulfuric acid [sulfuric acid on
Amazon, affil link]
when you haven't got a proper workshop to start with :)
I'll keep you posted on the next experiments.
Thanks again for your help and explanations, and since we're almost there, Happy New Year!
Cheers,
J
- Paris, France
Hello again Jeremie,
Thank you for your last comment, Happy New Year!
Process Engineer - Malone, NY USA
December 24, 2013
A. Old Weils potassium sodium tartrate bath:
150 gms potassium sodium tartrate
⇦ on
eBay
or
Amazon [affil link]
30 gms copper sulphate
80 gms NaOH
1 lit water
copper anodes
According to Ktehismus der Galvanoplasteik u.galvanostegie,Leipzig 1888.
Hope it helps and good luck!
- Zagreb,Croatia
Q, A, or Comment on THIS thread -or- Start a NEW Thread