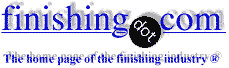
-----
Passivate stainless steel after black oxide?
Q. I have a SS 416 part that's ~8" in size that requires passivation on all surfaces, and black oxide on all but 2 smaller, flat surfaces that require electrical conductivity in the final product. There are 2 options that I can think of, but I'm not sure how they would work w/ these finishing processes.
Processes:
PASSIVATE IAW AMS2700. METHOD 1, TYPE 1, 2, OR 3
BLACK OXIDE AFTER PASSIVATION IAW MIL-DTL-13924
[⇦ this spec on DLA], CLASS 4. DO NOT OIL
Option A: Passivate and black oxide entire part, then machine off the black oxide from the 2 surfaces. Problem is, how can these surfaces be re-passivated since most of the part would need to be submerged to cover them in a tank. The black oxide needs to remain a very "black-looking" consistent color.
-- Can passivation be performed on these small areas with a paintbrush (similar to Alodine for Al)?
-- Or, can the black oxide surface be masked and the small surfaces be passivated normally? I'm imagining using a plastic bag to cover the majority of the part and taping up to the interface that needs passivation...
Option B: Passivate the entire part, then mask the 2 small surfaces and black oxide the remainder of the part. Is this possible with the black oxide process, even if it's time-consuming or not "easy?"
Any advice or insight would be much appreciated!!
Thanks!
- Landon
Engineer - Arizona
March 26, 2024
A. Hi Landon.
Option B would involve masking an area with a maskant capable of protecting against an extremely caustic and very hot mixture. Option A allows either brush passivation (which should be very practical), or masking the part against a relatively innocuous citric acid.
Option A sounds better to me.
Luck & Regards,
Ted Mooney, P.E. RET
Striving to live Aloha
(Ted can offer longterm or instant help)
finishing.com - Pine Beach, New Jersey
A. Landon,
I try to not be too obnoxious on this point, but given the difficulty of your situation I will again say that I do not understand why anybody wastes the use of stainless steel by coating it. Regular steel is protected from corrosion via coatings, while the entire point of stainless steel is corrosion resistance without a coating. Stainless steel costs more in order to gain this benefit, but the use of a coating renders that advantage moot.
However, I know that you are just following customer requirements and have no control over the part design. I agree with Ted here, and there are citric passivation paste products that would make your spot passivation/brush passivation task much easier.
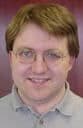
Ray Kremer
Stellar Solutions, Inc.

McHenry, Illinois
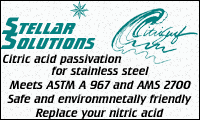
⇩ Related postings, oldest first ⇩
Q. Hello,
I feel foolish asking this question but here it goes. I'm having some 303 stainless steel parts sent out for black oxide. Though the parts have gone through this process is safe to say that passivation is no longer needed? Further more what would be my end result if I were to passivate parts that have been black oxided? I'd like to try it out but then again why waste time and money when I can get an expert's opinion.
Student - Manhattan Beach, California, USA
October 1, 2013
A. Jay,
I'm not a black oxide guy but my general understanding is that a proper black oxide coating should already be passive. You may want to ask the question of the shop that will be doing the job for you.
If any passivation were to be done after black oxide, I suspect that citric acid would be better as nitric acid would have a stronger potential to eat right through the black oxide coating.
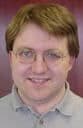
Ray Kremer
Stellar Solutions, Inc.

McHenry, Illinois
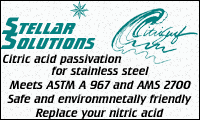
Q, A, or Comment on THIS thread -or- Start a NEW Thread