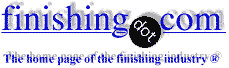
-----
Validated hydrogen embrittlement test failure (chromium plating with HF/H2SO4 anodic pickling pretreatment)
Q. Hi guys,
I could really use some expert opinions about the following. It is quite a story so thanks in advance for taking the time to read it.
FYI we are a Nadcap accredited aerospace company with quite some knowledge about the phenomenon of hydrogen embrittlement. We've done a lot of literature research, including scanning the many topics on this forum for relevant information. All of our processes are well within specification requirements.
Recently we've experienced two HE test failures. One with AMS2460 chrome plating and one with AMS2404 EN plating both with 3% HF / 50% H2SO4 anodic pickling pretreatment. Fracture surface analyses (SEM/EDX) proved HE to be the cause for the failures (intergranular de-cohesion but also segregation of alloying elements Mn and S). Type 1a.1 test specimens per ASTM F519, purchased at Green Specialties with all CoC's conforming the spec.
With the EN plating failure our conclusion was an operator having mixed up 2 sets of bars when removing one from the oven and putting the other one into it. No hard evidence so we decided to scrap the lot of parts ($$$).
Two months later however we experienced the same failure with chrome plating. A similar mix-up could not be possible since we only chrome plate bars once a week instead of several times a week with EN plating (with each lot).
We also perform AMS2460 chrome plating without pickling with three tanks. One of these tanks is qualified for production with the anodic pickling pretreatment however and is therefore tested with and without pickling every four weeks. We've never experienced test failures with the regular chrome plating so far, so the pretreatment is our main suspect (this same pickling tank is used for the EN process, strengthening our suspicions).
Facts:
-The bars were baked within 10 minutes after leaving the chrome tank (AMS2750 375±25 °F) for 40 hours.
- negligible time between pickling and chrome plating.
- test failed after 160 hours. Incremental step load test per ASTM F519 on remaining 3 bars failed as well.
Conclusion:
-hydrogen having entered the bars during anodic pickling (current-less time - however very short - and chrome plating - 4 hours - wasn't baked out enough afterwards.
-this can only be caused by some sort of barrier (?)
Strange observation during anodic pickling:
-It seems like an electric barrier is building up during the anodic pickling (60 seconds, 35A/dm2). Oxygen is formed at quite a rate and deceases to a minimum after half a minute or so (voltage of rectifier going up at the same time) and then voltage goes down again and oxygen is formed in line. Looks like some cyclic event. We've seen this with a different rectifier as well and can not explain it. Smut is formed which is not allowed to be removed per customer requirements.
Does anyone recognise this strange observations or have a clue what direction we should go to find the root cause?
I've blocked both processes and obviously pressure for deliveries is building up in the mean time.
Hope someone has an idea. James, Ted, others?
Thanks in advance!
Jeroen
Chief of plating dept. - Helmond, The Netherlands
July 11, 2013
Q. I'm posting additional information that we've just discovered.
We use rubber caps to mask the threads of the 1a.1 type bars. They have a little hole in the center for the fixture to make electrical contact. It appears that the operators don't always pay attention to make the caps fit very tight. This leaves a small open space between the cap and the bar where acid from the pickling tank can accumulate. Rinsing after pickling takes place by submersing in a deionized water tank. But this will not guarantee the complete removal of potential acid remains underneath the cap. These traces of acid could stay there during the 4 hour chrome plate process at elevated temperature and could cause extra hydrogen absorption in the base material.
Two questions arising from this hypothesis:
- Is it possible to "overload" these test bars with hydrogen so that baking at 375 °C for 40 hours is not sufficient to remove all of the hydrogen?
- Is it likely that hydrogen migrates through the base material towards the notch during a 160 hours period of testing under 75% of UTS?
I've read several times that minutes of pickling causes more risk for HE than hours of plating...
- Helmond, The Netherlands
July 14, 2013
![]() |
A. Hi Jeroen, Aerospace - Yeovil, Somerset, UK A. Hi Jeroen, - Cañuelas, Buenos Aires, Argentina |
Q. Hi Brian,
What do you mean with a ratio imbalance? Sulphate/Fluoride? No ratio is specified, neither could I explain from a chemical point of view what impact this would have on HE.
Hydrogen is formed when they test bars are put in the tank and the current hasn't been switched on yet and also when the current has been switched off and the bars are still in the tank.
Rectifier is calibrated once a year. No deviations there.
We're not allowed to remove smut per customer requirements. After anodic etch the bars are rinsed and enter the chrome tank.
Hi Daniel,
The bars are made of AISI 4340 (0.38% C incl. alloying elements) heat treated to 260-280 ksi as per ASTM F518 [ed. note: inactive].
Regarding the oven: AMS2750 continuous furnace. SAT every two weeks, TUS every 3 months. No deviations.
Chrome thickness minimum of 51 microns (AMS2460) and 39 microns for nickel phosphorous (AMS2404). No deviations.
Time between pickling and baking is a little over 4 hours for both plating processes, since the bars have to be in the chrome / EN tank for about 4 hours.
Thank you for your replies.
Without knowing the root cause yet, we've decided to minimize all contact with hydrogen (within spec limits) like immediately turning on current in the etch tank, quickly removal of parts out of it afterwards and immediate very thorough rinse. We also got rid of the masking caps and use lead tape instead to minimize inclusion of acid.
Together with minimizing hydrogen charging we maximize the opportunity for embrittlement relief bake. ASAP in the oven for at least 30 hours, which is standard practice anyway but emphasized again to the operators.
At this moment we're requalifying the processes with these parameters optimized. We've trained the operators in this new procedure and have our fingers crossed during the 200 hours test period. In the mean time the root cause analysis carries on.
Thanks,
Jeroen
- Helmond, The Netherlands
A. Hi Jeroen,
Don't worry about the ratio, rather than putting the parts into the tank and then starting the current try putting the parts into a live tank, have a trickle of current running when putting the parts in then turn up to working current, this will help prevent exposure to hydrogen. Also remove your parts from a live tank, reduce the current to a trickle and then remove parts. This way there should be no exposure to hydrogen.
You are using some very high tensile steels. My company actually prohibits the use of acid pickling (anodic or otherwise) on steels above 180ksi. We even prohibit some forms of plating on steels of the sort of strength you are talking about because of the susceptibility to hydrogen embrittlement.
Aerospace - Yeovil, Somerset, UK
Hi Brian,
Thank you for your advice. We'll go and have a look at it. We produce landing and arresting gear which is made of ultra high strength steels heat treated to these strengths. This kind of pretreatment is prescribed by our customer to provide for maximum adhesion. We're aware of the risks involved with respect to HE.
thanks,
Jeroen
btw: requalification of both processes with optimized parameters is running at this moment. 29th of July will prove if our hypothesis is correct. In the meantime we're investigating the root cause.
- Helmond, The Netherlands
Q. One of my engineers came up with a very interesting and plausible hypothesis.
Our main suspect til now was H2SO4/HF potentially staying in contact with the test bars for a considerable amount of time, "overloading" them with hydrogen. The big question mark with this being the direct cause is that the bars were baked immediately for an extensive period. Why wouldn't this be enough to free the bars from hydrogen absorption?
The engineer's theory is that all hydrogen may have been baked out, but remains of highly concentrated sulfuric acid may have remained on the threads, since the boiling point of H2SO4 is significantly higher than the baking temperature. During the testing delay after baking, moisture from the air may have diluted the traces of acid still present on the threads of the bars and continued to produce hydrogen.
We're now trying to replicate the test failure with this in mind.
I'll keep posting the results of our investigation to ensure this topic will be of value for others experiencing these same problems in the future.
to be continued...
- Helmond, The Netherlands
A. Hi Jeroen,
As Brian said, that are very high tensile strength bars, you must be very careful and hydrogen release is not assured 100% in these cases by baking... There are some mechanisms HE appears that are unclear.
The H2SO4 accumulation in the rubber protecting the thread and continuing producing hydrogen is not a bad theory. The sulfuric acid could dissolve iron even without moisture, thus generating hydrogen. It may be the cause you are looking for, but you should have some experiments to have this hypothesis validated.
You seem well guided in this search for root cause, so when you have some results, please share them with the community! You could may help others that could use this information to solve their own issues :)
Good luck and regards,
- Cañuelas, Buenos Aires, Argentina
Q. Hi guys,
It's been a while since my last post and since the last test failure... Unfortunately we've recently experienced another test failure, again with the above mentioned pickling tank involved (chrome plating). Thankfully Nadcap procedures did their work again and no affected parts were sent to customers but quarantined in house.
Since we've minimized hydrogen charging during the process and maximized facilitating baking out hydrogen after plating (both within specification requirements of course), our main focus now is on the bars themselves in combination with this rigorous pretreatment.
Tensile stresses in the bars prior to plating may contribute to in-process hydrogen embrittlement. The 1a.1 type bars are stress relief baked by the supplier. However, this stress relief bake rises question marks with us. 191 °C (375 °F) for 4 hours minimum will have negligible effect on potential stresses incorporated due to machining of the bars, as we've learned from metallurgical specialists we're in contact with. You need 30 °C below tempering temperatures for that we were told. Almost any plating spec prescribes 191 °C however, which is far below this temp.
At this moment we have had Barkhausen Noise analyses tested on 52 untreated bars of the same lot and discovered a significant variation between the highest and lowest readings. Next step is to perform X-Ray Diffraction analyses to quantify the compressive and tensile stresses.
The idea is to expose the bars with maximum tensile stresses to the pickling process and see if there is a relation between the Barkhausen signal and the exposure to this process. Unfortunately we cannot find any relevant literature online regarding this theory (i.e. tensile stresses due to manufacturing of the bars that can cause hydrogen traps where accumulated and recombined hydrogen atoms will cause greater tension as a result of pressure build up in the bars up to embrittlement and subsequent crack initiation and propagation, prior to embrittlement relief baking).
We've also learned that one sustained load test result will not provide exclusive evidence on a suspect parameter. Only statistical analyses of many (how many?) test results will give an answer due to the complexity of HE and the many factors influencing this phenomenon.
Expert opinions on our approach are very welcome.
Thanks,
Jeroen
- Geldrop, The Netherlands May 2, 2014
A little remark to my previous post. AISI 4340 heat treated to 260-280 ksi has a tempering temperature of about 225 °C. The stress relief bake therefore at 191 °C ± 14 °C is in the right range. 300M however and PH13-8Mo are different stories.
Jeroen Visser [returning]- Geldrop, The Netherlands
Hydrogen embrittlement test (ASTM F519) failures on notch test bars
Q. I am experiencing difficulty in getting hydrogen embrittlement notch bars (ASTM F519, type 1a) to pass the 200 hrs at 75% NFS load test in my hard chrome solution.
The problem started a few months ago, the notched bars comply with ASTM F519 according to CoC, the process of plating has not changed as far as I can tell. The failures occur at random intervals and in different tanks and I did a deep investigation into the whole process and didn't identify any discrepancies.
I have been doing this test for 10 years and this is the first time I have had this many failures without being able to identify the root cause.
All steps of the process were accomplished including the Hydrogen Embrittlement relief for 23 hrs at 190 °C.
I appreciate any kind of help.
MATERIALS ENGINEER - AEROSPACE - SAO PAULO, BRAZIL
February 9, 2020
A. Hi Alessandro. This is probably obvious, but I wouldn't look anywhere else before triple checking or quadruple checking the thermocouples/gages/thermometers regarding baking temperature. Then I would make sure the specimens with failures were not delayed on their way to the oven.
Regards,
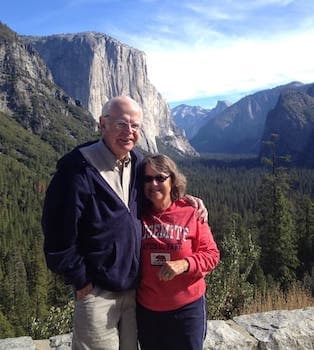
Ted Mooney, P.E. RET
Striving to live Aloha
(Ted can offer longterm or instant help)
finishing.com - Pine Beach, New Jersey
Q. I have the registers of delay time between the end of chromium process in the tank and the embrittlement relief on the oven, the data showed that thee specimens had 3 hours of delay time. We performed the TUS and SAT monthly and no discrepancies were found.
Do you know if possible we have foreign chemical agent in the bath that can contribute to promote more hydrogen during the chromium process inside the tank?
Do you have experience that specimens shall be processed together with parts? The standard AMS2460 doesn't specify that. A curious point is that the operators had difficulty to reach specified current to plate the 4 specimens in the tank.
MATERIALS ENGINEER - AEROSPACE - SAO PAULO, BRAZIL
Hi, Alessandro.
Q1: Do you know if possible we have foreign chemical agent in the bath that can contribute to promote more hydrogen during the chromium process inside the tank?
A1: Check chloride concentration in the plating solution. The ideal is below 20 ppm, when 50 ppm is excessive. Also perform metal impurities search by ICP or equivalent method.
Q2: Do you have experience that specimens shall be processed together with parts? The standard AMS2460 doesn't specify that. A curious point is that the operators had difficulty to reach specified current to plate the 4 specimens in the tank.
A2: In my opinion, it is extremely important to plate the HE specimens with thoroughly controlled parameters - both current and time. 4 specimens have plating area of 0.05 sq.dm each, 0.2 sq.dm all together, so they should be plated at 1.5 A per piece, 6 A for the four together. Try to plate to a minimum thickness required - 0.003". It should take about 5 hours. Also try to minimize the transferring time from the bath to the oven. We did it for 15 minutes.
Good luck!
- Lod, Israel
Q, A, or Comment on THIS thread -or- Start a NEW Thread