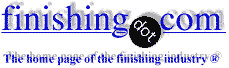
-----
Black Anodizing for Space Usage
2000
I'm an OEM that wishes to properly specify a black anodized aluminum surface on my drawings for parts that will be fabricated at an outside vendor. This part will be going into space, so low outgassing and high IR emissivity are important. This 6061 aluminum alloy part will also have selectively nickel plated areas and helicoils / Keenserts installed. Those areas not plated will receive black anodizing. The helicoils / Keensert holes will be bare aluminum except that these threaded inserts will be installed with wet zinc dust
⇦ on
eBay or
Amazon [affil link]
. Otherwise, I want no exposed aluminum surfaces in order to prevent corrosion from causing flaking of the nickel plating edge. I've heard that this is best prevented by anodizing after the plating, but if you disagree please let me know and why.
Please critique this note for the anodizing:
Black anodize the specified areas per
MIL-A-8625 / MIL-PRF-8625
[⇦ this spec on DLA] Type II Class 2 Color black no. 37038 per FED-STD-595. IR emissivity 0.85 minimum per
?. Total mass loss (TML) 1% maximum and Volatile Condensible Material (CVCM) 0.1% per ASTM E595.
You'll notice I also need a suggestion for the proper spec for emissivity.
Thanks,
aerospace - El Segundo, California USA
Highland Plating is currently working with a variety of Raytheon Divisions creating specifications for plating and or anodizing for space use. We have our own lab and can measure emissivity, reflectivity and absorption. We have just recently run a variety of tests for one of your sister divisions and have the revelent measurements and results on aluminum: we are awaiting a sample of beryllium for further testing. Feel free to contact me for more information regarding our results.
James Mayfield- Los Angeles, California, USA
2000
Q, A, or Comment on THIS thread -or- Start a NEW Thread