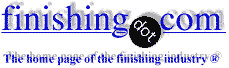
-----
Burning of 2024 Alloy During Anodizing
We have experienced two recent failures with 2024. One with hardcoat and one with type II. In the first case the parts were thin (.030) rings for hardcoat, which didn't build in size and began burning at a thin coating. We use a 25% sulfuric bath with about 1.5% oxalic at 30 deg. using pulse rectification with a two minute ramp time. The second, and more baffling situation was a typeII requirement for a very thin deposit. We got the deposit, but the parts became smaller. This bath is a 25% bath @ 68 deg., going in hot @ 17 volts. Should the voltage be started low and brought up slowly, as in a hardcoat situation? I suspect that the ramp time in the hardcoat was too aggressive, and that the 17 volts in the type II was too high. Am I on the right path, here?
Peter Faxonplating shop - Oxnard, California
2000
I suspect that the 0.030 part had too much area for the thickness of the metal, could not carry the load with the contact area and arced. It might possibly have worked if the ramp had been a little slower for this particular part.
Type 2--25% bath. A whole lot strong, especially if it was 25% by volume and not by wt. At your temp, you were eating off the anodizing nearly as fast as you added it. If you had used the normal 15 volts, you probably would had had very nearly zero anodizing and a little more metal loss.
I have not personally heard of anyone using 25%, but I sure do not know everything about anodizing.
- Navarre, Florida
2000
To James: The higher acid concentrations obviously help with defeating a "burning" in the material, but you're pretty much right,
25% is too high. 20% (which we use) is even in my opinion a tad bit overkill 17-18% might be optimum, to allow build up, and still prevent burning of the hard to anodize materials. Thats the only logical reason I could see for going with a 25% bath, but its a matter of diminishing returns, you can only go so high before the negatives will be equal to, or outweigh the positives.
To Peter: For the Type II bath, 17V might not have been too high, but considering the point you mentioned about going in hot, do you mean electrically hot, or temperature hot? Because entering a part that came from a 140F solution to a 68F solution can cause it to burn because you don't allow the temperature of the part to regulate to that of the bath. If you're talking electrically hot, I'd warrant against such a thing. You have too immediate of a spike in voltage/current to the part in my opinion. I've never went into an anodize tank that was live. Others might, and can, but I don't, and I've never had a problem doing it that way.
All in all, I'd say lowering the concentration on both anodize baths will give you better results.
- Toledo, Ohio
2000
Q, A, or Comment on THIS thread -or- Start a NEW Thread