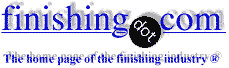
-----
Pitting on Pattern-Plated Copper Traces
We are seeing severe pitting on the pattern-plated copper traces, mostly near to the etches.
Our pretreatment process consists of acid cleaner, microetch & acid dip. ( etch rate 15 microinch ) we are not using anode bags but we have anode shield.
The fine line job is being affected by pitting issue. Ground area do not have any pitting problem. two months ago, we did carbon treatment for our copper bath. circulation pumps are all ok. ( no air leakage at the suction side ) we are using phosporised anode ball.
Oil free air supply is coming to our line.
Kindly help me to solve this issue.
Regards,
- Singapore
2000
The most likely cause, assuming the chemical parameters are all ok, is photoresist residues/incomplete development. Take a close look at the sidewalls of the resist and the copper surface after the developer. You might take a panel after development and microetch it, then look at the base of the resist sidewalls. If the surface was not etched, then you know you have an imaging/developer problem.
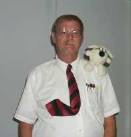
James Totter, CEF
- Tallahassee, Florida
2000
2000
Hello,
As Mr. Totter described, one part of the problem is in the developer. By creating sticky side walls of the resist, small bubbles attach to it easier. There is a lot of actions one can do to help minimize the problem.
1. Keep the last rinse in the developer under a pH of 7. (To terminate "after developing" )
2. Minimize the use of anti foam and maybe try another brand.
3. Run the circ. pumps in the plating bath only when not producing
(depends on how heavy production pressure is).
4. Introduce a wetting agent in the pre dip (leveler)
5. Check the leveler content in the plating bath. If its too low it might increase the problem.
- Sweden
Q, A, or Comment on THIS thread -or- Start a NEW Thread