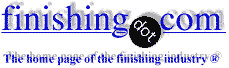
-----
Spotting on aluminum parts with chromate finish
March 1, 2021
Q. Hello,
While looking on the internet I came across a thread from a few years ago, it's a problem we are experiencing today so I thought I would reach out? I am looking for someone that can verify what foreign substance is on some product we produced and had Chromate Treated (MIL-DTL-5541F Type II, Class 3 Clear).
I have attached a picture of the defective part:
We have several parts that exhibit this condition, it is not a common issue but relegated to a point in time which pointed me back to the supplier (not a very good supplier). I am sure we have solved the issue by switching suppliers to a (NAPCAP) supplier with much better process controls in place. My question is this:
The parts in question are used in a medical application, our customer would not be concerned about the visual but has asked me questions such as "What are the stains/black spots?, Can they migrate? and What could have caused this?"
Do you have a way to test parts in this condition? I ultimately need to convince the customer that all is OK and that what we are seeing is a visual surface issue and not anything we are introducing (for example) into the air? My initial comment to them was that I believe this could be a reaction to Machine Coolant that perhaps was left on the parts too long after manufacture but I am really not sure. At the end of the day I need to understand what is on the part (scientifically) and to determine if it?s under the coating or on top of the coating?
Can you help, if so what is the cost to test ?
Lou MautoneElk Grove Village, Illinois
? 1. What is the alloy?
2. Has it been heat treated. How hot?
3. Do you have any info on the sharpness of the cutting tools, expected dull.
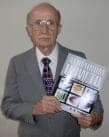
Robert H Probert
Robert H Probert Technical Services

Garner, North Carolina
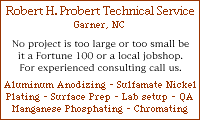
September 5, 2021
A. Hi Lou,
Late to the game here, but first off, yes switching to an accredited supplier was a good call.
I've seen very similar defects develop from parts that have been contaminated with iron residue in the machining or initial-op steps. My current headache ... I traced back to a dirty waterjet. Yuck.
Yours may well be shared mills that weren't properly cleaned between runs of differing materials, with dull tooling that smeared the foreign matter into the substrate. The fact that some surfaces, cut with a different tool, or a different cutting surface of the same tool, look clean- it's not a material defect from the mill.
The cost of sending a couple parts out for salt fog testing to see if it's functionally compromised, not just visually, isn't that bad. I've never had to send out RoHS chromate for this, but identical visual defects on yellow chromate do fail salt fog.
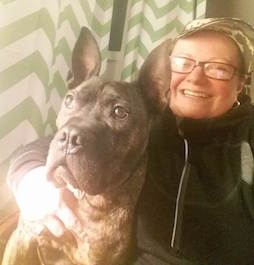
Rachel Mackintosh
lab rat - Greenfield, Vermont
September 30, 2021
Q. There is white corrosion spots/pits are getting developed after 1-2 month on chromatised aluminium alloy surface.
Please suggest some remedy.
- India
September 3, 2021
A. Hi N. We appended your inquiry to a previous thread on pretty much the same subject, so it should give you food for thought if not a solution. But as you see, a lot of data is needed in order to offer specific advice. Please give us some facts like the alloy, the process sequence, the general type of parts, the exposure situation, whether you have chromated aluminum before without this problem, etc.
Imagine an employee has come to you with the problem and you must personally do the research for it. What you would probably require to be told we probably require to be told :-)
Luck & Regards,
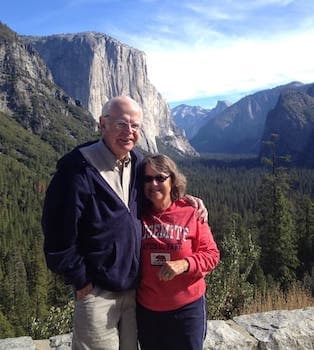
Ted Mooney, P.E. RET
Striving to live Aloha
(Ted can offer longterm or instant help)
finishing.com - Pine Beach, New Jersey
September 2021
September 6, 2021
Q. Thanks sir for response,
The aluminium alloys which are chromatised are 6xxx, 2xxx & 7xxx.
The process sequence is Acidic Degreasing - Etching in hot caustic soda ⇦liquid caustic soda in bulk on
Amazon [affil link]
- Desmutting in dilute Nitric acid - Chromating in yellow chromating bath - Drying.
After every step, Rinsing in water is carried out.
As shopfloor environment has acidic/alkaline fumes, we release the chromated items out of shopfloor, immediately after drying.
It is observed that graphical white corrosion spots/pits are developed after about 1 month while keeping the components in open environment.
Since we are doing chromating as per above since long, but no such issues was occurred.
Requested for remedy.
Regards,
- India
A. Hi.
Since you did not have the problem in the past, we probably cannot blame the environment the parts are exposed to, or the process sequence, although alkaline etching of some of those parts is probably not recommended.
Since the problem extends across 6xxx, 2xxx, and 7xxx, it seems quite unlikely to be a material problem.
To me, that leaves poor chromate chemistry as the most likely cause of the problem. Is it practical to make up a new bath, or to run some parts through a bucket of fresh chromating solution, or to run some coupons and have them salt spray tested?
Luck & Regards,
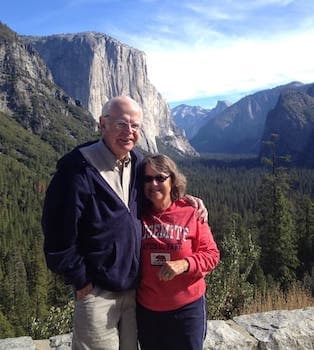
Ted Mooney, P.E. RET
Striving to live Aloha
(Ted can offer longterm or instant help)
finishing.com - Pine Beach, New Jersey
September 2021
⇩ Related postings, oldest first ⇩
Q. We make a 6061 aluminum part that is clear chromated.
The customer has complained that the chromating is turning dark under the washers used for mounting (steel, yellow zinc)
What would cause this and how do we prevent it.
sheet metal fabrication - Kernersville, North Carolina
July 8, 2008
![]() |
A. Use cadmium plated fasteners instead of zinc. If they have a cow about that, have them try stainless steel, 18/8 and not 400 series. James Watts- Navarre, Florida July 11, 2008
A. It is simple galvanic corrosion. "Clear" chromate is the most overrated and mis-used title in our industry. Use heavy yellow chromate on the zinc plated washers and heavy yellow chromate on the aluminum surface. Eventually with temp and humidity cycling, that too, will fail. ![]() Robert H Probert Robert H Probert Technical Services ![]() Garner, North Carolina ![]() July 11, 2008 |
Multiple threads merged: please forgive chronology errors and repetition 🙂
Single top light
Top light & LED side light. Note some areas appear white where before it was gold. Also some of the black seems textured.
Q. I'm looking for some help narrowing down what it is and the source of black spots on some chromated 7075 Al parts. I am the quality manager of the machine shop working with the plating shop to eliminate this issue.
Extruded 7075 T651 is milled then tumbled with ceramic media. From there it is sent to a vendor for "chemical conversion coating class 3 per MIL-C-5541" Most parts seem fine, but we find some with small black spots, or lines that generally follow the mill marks. In a few bad cases it looks like there is some tiny clear or white crystals forming in the area of the spot.
Photos thru a 20x microscope and handheld camera. Roughly 0.1" x 0.1" view
Dale Puch
Quality Manager - Orlando, Florida, USA
August 6, 2012
A. 1. I do not know how hot is T651, but any heat on 7000's moves the zinc out of alloy into the grain boundaries as molecular zinc (which forms white compounds with chemicals like sulphates, acetates, and others)
2. You mention "tumbled", well the media must be designated "aluminum only", and if any steel has been run (even on the night shift) with the same media, you will pound iron particles into the soft aluminum - which turn orange and brown.
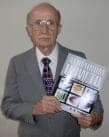
Robert H Probert
Robert H Probert Technical Services

Garner, North Carolina
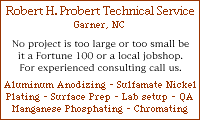
August 7, 2012
Q. We only tumble 6000 and 7000 series aluminum in that tumbler and media.
Is there a good way to confirm this is caused by the zinc? You indicate this is a material issue. Do you mean the material may be out of spec, or just problematic?
Assuming zinc is the reason, what steps in the chem film process are most likely to be causing or able to control this. Especially since 90% of the parts seem fine. I can not change the material specification, but is there something I can request of the extruder for future material orders?
- Orlando, Florida, USA
August 8, 2012
A. Since it is only occurring on 7075, then that points to the possibility that the zinc has moved -- not necessarily because the metal is inferior, but naturally because of having been heated (has it?). What kind of deoxidizer? Let's look at a piece with a 10X loop after the deox and see if we can notice a raise or a pit.
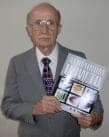
Robert H Probert
Robert H Probert Technical Services

Garner, North Carolina
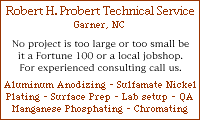
August 9, 2012
August 25, 2012
Q. No heating of the part other than 120 °F or so during parts of the chromate.
Lab test results for several locations on the same part
"The results of SEM-EDS analyses indicate that contamination during the conversion coating process is a likely cause of the spots. Analysis has not provided any evidence of coating rupture; therefore it is possible that deposits of Zn and Cu have later undergone reactions with the environment. The levels of Zn, Cu and O detected in certain areas suggest that both zinc and copper oxides may be present."
Table 1 -Semi-Quantitative Chemical Composition in Wt. %
Location O(%) Cr(%) Fe(%) Ni(%) Al(%) Zn(%) Cl(%) Cu(%)
Scraped off Dark Material 39.4 16.4 1.7 0.4 35.5 4.3 -- 2.3
Darker Spot 13.6 4.2 -- -- 77.4 4.8 -- --
Lighter Spot 10.6 1.2 -- -- 81.4 4.2 0.6 2.0
Scraped Area 5.5 1.0 0.2 0.1 86.4 4.9 0.2 1.5
Clean Area 5.9 2.4 -- -- 85.4 4.8 -- 1.4
- Orlando, Florida, USA
A. Keep bringing us more data. I have two more thoughts. (1) Ask the chromater to increase the alkaline etch to remove the work hardened streaks where the metal pulled thru the extrusion die, and (2) be sure he is using a "mixed acid deoxidizer based on Ferric sulphate" and also sulfuric acid, fluoboric acid, and nitric acid (this may help remove the zinc and copper from the surface before you get to the chromate. See if his deox is air agitated because ferric changes to ferrous unless air agitated, and ferrous does NOT deoxidize. Note that we chromate "aluminum" only and the aluminum chromate formulation makes copper black and makes zinc a dark dull gray. You see all that zinc and copper in your analysis, 7075 is usually over 5%/wt zinc. Earlier I asked how hot temper 651 was because if it was heated at the mill, then the zinc walked ("migrated") out of alloy and into the grain boundaries as molecular metal. Laying on top it reacts badly with the "aluminum" chromate formula.
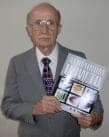
Robert H Probert
Robert H Probert Technical Services

Garner, North Carolina
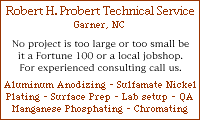
August 28, 2012
Q. I have an electronic product manufactured from Aluminium, and chromated after that. When the product is delivered in a European country from India, small black spots on them were observed which has led to severe customer dissatisfaction.
Please help me to understand what could be the black spots in the aluminium extrusions which are having chromated.
Arun Kumar- Kochi, Kerala, India
October 15, 2012
White powder in Alodine body
Q. Dear All,
We have an issue of white powder in Alodine process on aluminum body at inner surface, holes and edges. I have tried many ways like altering conc. of degreasing and activation, increase in time and flow of water washing, extra water washing after degreasing but still not found good result. Requesting for suggestion.
Plating engineer - India
February 9, 2017
White spots - chem film?
Q. Does anyone know what would cause white blurry spots on class 1A gold chem film? Could it be porosity in the material (aluminum casting)
Karie Foster- Santa Ana, California, USA
November 14, 2017
![]() |
A. Hi Karie, ![]() Rachel Mackintosh lab rat - Greenfield, Vermont February 12, 2018 A. "Silicon" on the surface will give a gray spot. There is no "silicate" in aluminum alloys 7000s but there is about 5% zinc which makes white salts. ![]() Robert H Probert Robert H Probert Technical Services ![]() Garner, North Carolina ![]() February 12, 2018 |
A. To clarify, if I may, since my wording was not that great; silicon only in its pure form is an alloying constituent of AL 7xxx. I of course acknowledge that silicates as such do not come from the metal. I start calling it that when it becomes "gross crud in solution/suspension that is interacting with other gross crud in same and messing up my nice tanks". Not too scientific. That's simply a general term for many Si-and-O-bearing, rather insoluble, substances and once a deox tank with plenty of oxygen has built up a ton of, well, gross crud in it you've got all the ingredients... settleable solids in a strongly acidic deox tank do happen when it's dirty enough. Free Si still in solution is the problem for later processing.
Please do take Mr. Probert's advice to heart. He's got more experience teaching this stuff than just about anyone!
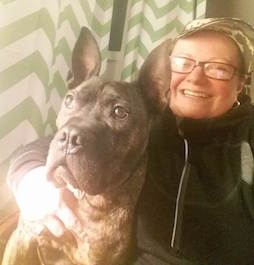
Rachel Mackintosh
lab rat - Greenfield, Vermont
February 13, 2018
![]() |
Clear Zinc Chromate has 'burn mark'September 11, 2020![]() Q. Hi all, I am a quality engineer working in Singapore. What will be the most possible for such defect occur? - Kallang, Singapore A. Hi Gray Luck & Regards, ![]() Ted Mooney, P.E. RET Striving to live Aloha (Ted can offer longterm or instant help) finishing.com - Pine Beach, New Jersey September 2020 A. First exactly what Ted says above. But the color is brown like iron oxide and I suspect it is the plating rack mark that dug into the steel leaving a bare spot which then oxidized to the brown color of rust. ![]() Robert H Probert Robert H Probert Technical Services ![]() Garner, North Carolina ![]() September 11, 2020
I guess I need another coffee :-) Regards, ![]() Ted Mooney, P.E. RET Striving to live Aloha (Ted can offer longterm or instant help) finishing.com - Pine Beach, New Jersey September 2020 |

Q, A, or Comment on THIS thread -or- Start a NEW Thread