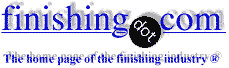
-----
Color difference in anodized parts
May 30, 2012
Q. We're baffled by this one guys. I've got two anodizing tanks both set at the same parameters. We're seeing a color difference in our type 2 class 1 coating. Parts are of the same alloy, and same lot of material. By the process of elimination, we've narrowed it down to a power supply issue, not a tank issue (we swapped out the power supply leads on the tanks) Both rectifiers are manufactured by Rapid/Dynapower. Both are 100 V 500 Amp power supplies. Both have been calibrated 2 weeks ago, and were well within specifications in current/voltage readout, and ripple. Ramp times are identical. The only difference that we know of is the age of the rectifiers, the one that is producing the undesirable color (lighter) is approx. 6 years older. During side by side runs there is only a 2 micron difference between the 2 power supplies, which shouldn't produce any notable color difference at all. Even after re-ramping to get the additional 2 microns on the lighter part, the difference was still there.
Any thoughts as to what may be going on inside of the power supply that would cause us to see this notable color difference, besides current/voltage and ripple? We did note that the part that is lighter in color ran at a lower voltage (approx. 2 volts lower) than the "good" part, but yet the amperage settings were the same. In the picture, the part on the right (darker) is the desirable result, the part on the left (lighter) is the issue.
Thanks in advance for any insight.
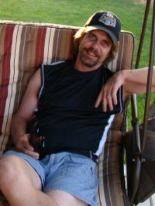
Marc Green
anodizer - Boise, Idaho
A. Let's disregard the accuracy of the ammeters and use high quality amp tongs on the rack. Next let's consider pore size. The pore is made larger by (1) higher temp, (2) higher free acid, and (3) lower current density. So after that is balanced between the two tanks, let's balance the dissolved aluminum.
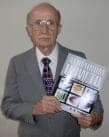
Robert H Probert
Robert H Probert Technical Services

Garner, North Carolina
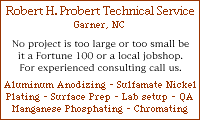
May 31, 2012
June 2, 2012
Q. Thanks Robert. Most of this we've already done.
The free acid concentration on the tanks were within 3 gr/lt of each other.
The tank temperatures were within 1 degree F of each other.
Current density was exactly the same on both parts, albeit we have not verified that with a clamp voltmeter/ammeter at the rack.
There is a 3-4 gr/lt difference in the dissolved Al content between the two tanks. Both tanks were operating below 8 gr/lt of dissolved Al.
Again, let me explain to you our methodology/steps we took in trying to determine the problem, so that you can clearly see it's not a chemistry/tank/racking issue. Keep in mind that tank #2 produces the desired color. Material is 5052 H32
#1. Tank #1 is producing a lighter colored/tinted coating than tank #2, at the same coating thickness.
#2. During side by side simultaneous runs (so that both parts went through the same pre-treatment, at the same time), we anodized 2 individual parts. Both parts were racked on identical Ti racks, with Al hooks as the contact at the buss bar. 63 amps (approx. 15 ASF) were applied to each part, after identical ramp times.
#3. We noted after the ramp, that tank #1 was showing a voltage of approx. 14-15 (unfortunately, this rectifier control panel has an analog voltmeter), while tank #2 had a voltage of 16.5 (digital voltmeter)
#4. After 41 minutes the part in tank #1 had a coating thickness of 18 um-19 µm (slightly out of the coating thickness spec which is 19um-25um), and the part in tank #2 had a coating thickness of 20um-21um. Color difference was evident. Part in tank #1 was re-ramped for an additional 5 minutes to get the same thickness as the part in tank #2. Color difference was still evident.
#5. As we noted a difference in the forming voltage, I ran another part in tank #1, this time adjusting the current so that the forming voltage matched the forming voltage in tank #2 during the previous test (16 volts). This produced a current of 73amps. Part was ran for 41 minutes, and this time the coating thickness was within the 19um-25um thickness spec, but the color difference was still very evident. There was no difference at all between the color produced during the first test, which surprised me a bit, as I expected it to be slightly darker.
#6. To determine if we had a tank issue, or a power supply issue, the rectifier on tank #2 (good color), was hooked up to tank #1 (bad color), at the buss bar/cathode contact points, and another part was ran using the same aforementioned parameters. After 41 minutes, this part was a perfect match.
So unless I'm completely missing something here, we've clearly demonstrated that we do not have a tank/racking/chemistry issue going on.
I need to clarify something in my original post as to the color difference, which is hard to see in the picture I provided. It's not so much a light/dark issue as stated, but more of a tint issue. The desired part on the right has a yellowish tint, to where the part on the left has a grayish tint.
Another interesting thing to note. Earlier during the process of determining what our problem could be, I ran 2 coupons (one in each tank) using the same parameters that we use for the parts in question. The only difference being is that the coupons were 6061 T6 material. After identical run times, the coating thickness, and color were the exact same. So whatever issue is that we have, is being magnified by the actual part alloy.
We've still got a thing or two to try next week, but at this point we are truly stumped.
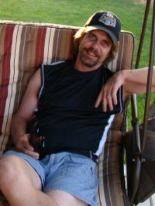
Marc Green
anodizer - Boise, Idaho
A. Is there any reason to suspect there is more iron in Tank 1 than in Tank 2 that may have dragged in from the deox?
Was the make-up sulfuric acid in tank 1 yellowish and the make-up water in Tank 2 clear?
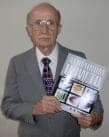
Robert H Probert
Robert H Probert Technical Services

Garner, North Carolina
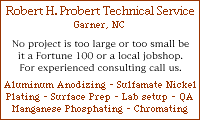
A. Can you process all of the parts in one tank? While that won't solve the mystery, it will solve the problem.
Since it may be alloy related, it might be worthwhile to take a look at the desmut step using slightly longer or shorter times.
And, I'd try to get the dissolved aluminum closer between the two tanks, perhaps by transferring some solution back and forth between them.
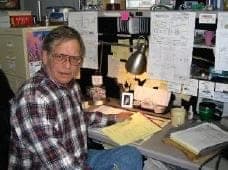
Jeffrey Holmes, CEF
Spartanburg, South Carolina
June 5, 2012
Q. Robert: No, no reason to suspect Fe would be higher, albeit that is something we haven't looked at. DI water is always used in our make-up. If we strike out on the power supply (update at bottom) we'll look at that. Good suggestion.
Jeffery: We have limited production of these parts to one tank. However, production demands have significantly increased, hence the need to use both tanks when necessary. We've also seen the difference in color when both tanks were at very close dissolved Al content. I just posted what the current operating conditions were for our very controlled testing to solve this problem.
Rectifier update: After yesterdays testing (making sure the cables, to the tanks were not giving us resistance, and also checking line input voltage to the rectifiers), we looked inside both rectifiers. The rectifier that produces the desired color (and also the older rectifier) has a bank of capacitors inside that rectifier #1 does not have. We suspect this may have been a cost cutting measure that Dynapower implemented when they bought out Rapid. However, we're not sure if this would be the cause of the issue we are seeing, and if so, why capacitors would have a change on the final color of the parts. I'm really thinking we have some type of power wave form issue. My knowledge in this area, and how it relates to end product, is non-existent.
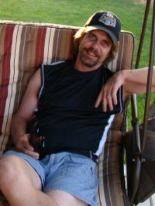
Marc Green
anodizer - Boise, Idaho
June 6, 2012
A. Hi Mark. It is possible that rectifier #2 was ordered with an anti-ripple filter choke. You can easily see the wave form on an oscilloscope. These days I believe high quality hand-held units with an LCD screen are available and inexpensive.
Regards,
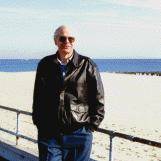
Ted Mooney, P.E.
Striving to live Aloha
(Ted can offer longterm or instant help)
finishing.com - Pine Beach, New Jersey
June 6, 2012
Q. As we learned Wednesday, that is exactly the deal Ted. The rectifier producing the lighter/undesirable color does not have the ripple filter that the other does. Both rectifiers were specified at time of order to have less than 5% ripple, which was verified during the calibration of the 2 rectifiers a few weeks ago, however we only looked at one amperage to verify the ripple, when we should have looked at the entire range. I wasn't involved too much in the calibration, so I'm not sure what amperage we looked at to verify the ripple.
We're definitely narrowing this sucker down. We would like to verify the issue by bypassing the filter on the "good" rectifier to see if we can reproduce the undesirable color with that rectifier, prior to spending $6k on a filter for the other rectifier. However, we're a bit gun-shy as we certainly do not want to harm the "good" rectifier.
Does anyone see any potential harm in bypassing a ripple filter to a rectifier for some testing?
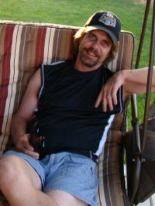
Marc Green
anodizer - Boise, Idaho
June 7, 2012
Q, A, or Comment on THIS thread -or- Start a NEW Thread