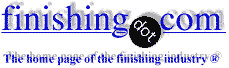
-----
Tin-Silver Electroplating over Copper Pillar Bump
Current question and answers:
Q. I am in the business of electroplating very fine geometry patterns on silicon wafers for use in the electronics industry. Recently, we have been exploring the concept of plating up copper "pillars" which will then have a "tin cap" on top of the pillar. The manufacturer of the tin electroplating chemistry (it is actually a tin-silver alloy) recommends depositing a specific type of nickel layer as a barrier between the copper and tin.
My questions are:
Is this nickel layer necessary, and if so, does it have to be the special sulphate nickel that is specified?
What is the best way to remove a copper seed layer after the nickel and tin-silver metals are plated on top? Our traditional seed removal chemistry damages the tin-silver.
Thank you!!
- Minneapolis, Minnesota
January 18, 2021
⇩ Related postings, oldest first ⇩
April 1, 2012
Q. Hi, my company is a European semiconductor company in which we just started electroplating of material such as Tin-Silver.
I carefully read the topic about the effect of Sn4+ on precipitates and bath monitoring (letter 1185).
Actually, my concern is not completely related to the plating of Tin-Silver but more especially to the process which consist to remove a copper seed layer after the plating process.
I have been using for years a sulfuric-peroxide mixture and facing for a couple of months some issues because my Tin-silver (0.98/0.02) deposition tends to lift from the surface when using Sulfuric-peroxide mixture.
I am pretty sure that the plating bath is mainly responsible as at the beginning of the lifetime we don't face any issue. We also demonstrated that using only a sulfuric, it is not enough to dissolve Tin-Silver from my deposition. An oxidizer added to sulfuric seems mandatory to reveal the issue.
We evaluated some other chemicals to etch the plating seed copper and noticed that, for example, a phosphoric-peroxide mix was efficient to remove copper while any affect the integrity of the Tin-silver deposition.
It looks like a Sulfuric sensitivity to my issue but only when oxidizer is adding.
I read that SnOx which can precipitate in bath is insoluble in Sulfuric.
Any help would be appreciated to understand why, once the full Tin-Silver deposition done, the material could still be etched or removed when using a sulfuric-peroxide mixture.
Thanks.
- Grenoble, France
April 4, 2012
A. The precipitate is actually a hydrated tin oxide of variable composition = SnO2.xH2O. There can actually be a significant amount of Sn+4 that is soluble before precipitation occurs.
Resorcinol is another common anti-oxidant used in acid tin plating baths at a concentration of 3-4 g/L.
consultant - Cleveland Heights, Ohio
April 5, 2012
Q. Thanks Lyle!
Maybe I do not explain correctly my concern. If I well understood your answer, you mention a reaction between Sulfuric acid and MSA bath.
If it is the case I agree with you because we perform a trial by mixing a few ml of sulfuric in a sample of MSA and after a couple of hours we noticed 2 phases in the beaker with precipitates at the bottom. This confirms the large amount of Sn4+ in my plating bath.
Actually, my concern is after deposition on wafers.
In the process flow after plating, a photo-resist is removed and then the copper seed is etched.
During this step, the use of Sulfuric/Hydrogen peroxide makes the Tin-Silver lift from the surface. The TiN-Silver consumption does not only occurs at the interface with copper but can happen in the bulk solder.
A oxidizer like peroxide needs to be added for copper etch. Diluted sulfuric only could not removed the copper seed.
We tested Sulfuric only and notice no damage of the solder bump but adding a oxidizer is critical for the Tin-Silver which is strongly attacked.
I guess there is a link between the Sn4+ in my bath and the solder lift after sulfuric/peroxide etch but could still not understand the reaction.
Regards,
Mike
- Grenoble, France
A. It sounds like the copper etchant that you are using is too aggressive and is undercutting the solder. Can you use a less aggressive etch formulation? Also, in case that there is still some etchant under the solder bump edges, it may be necessary to rinse quickly and thoroughly once the copper is removed.
Lyle Kirmanconsultant - Cleveland Heights, Ohio
April 9, 2012
April 23, 2012
Q. Good morning everybody,
We've been running some Copper pillar process for a couple of years in my European company. The stack is made of Copper + Tin-Siver.
I face a big issue at this moment during the reflow process which consists of consolidating the Inter Metallic Compound (IMC).
At the end of the reflow, we notice that the solder has been totally removed from the copper surface. We can find some rest of Tin-Silver out of the Cu pillar on the substrate.
It looks like a very bad wettability of the solder once the liquidus reached.
This bad copper wettability finally leads to the total removal of the Tin Silver solder.
Did anybody already face such concern?
Any help would be welcome.
Regards,
Mike
Wet & Plating process expert - France
Q, A, or Comment on THIS thread -or- Start a NEW Thread