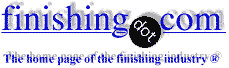
-----
Is a yellowish/greenish (sodium dichromate) appearance on galvanized structures a process defect?
[an error occurred while processing this directive]Q. Hi.
Reading Mr. Chen Sian Teck's question:
Is, The yellowish/greenish color a process defect?
In terms of AS/NZA 4680:2006 would this be visually acceptable in terms of inspection?
- New Zealand
August 9, 2021
August 10, 2021
A. The yellowish stain left after passivation (the act of dipping in the sodium dichromate) isn't a process defect. But it should not normally be used at such a strength to be green.
Not all galvanizers do this passivation. It doesn't last that long (4-6 weeks), and the main reason is to avoid "white rust" or "storage staining" - that white deposit referred to earlier in this thread (good explanation the galvanizer gave).
But be aware that this chemical is under severe environmental pressure. Chrome 6+ is, in its strong form as purchased, and before massive dilution by the galvanizer, a nasty substance, and requires careful handling. As such there are moves in various countries (eg EU) to ban it, and under current EU rules it has only a few years to go until a total ban. Galvanizers and others have a temporary exemption to continue its use.
There are other ways to stop white rust - and its other name "storage stain" gives the clues. Store new galvanizing either dry or not in contact with other galvanizing. It only forms when freshly galvanized steel is wet and touching.
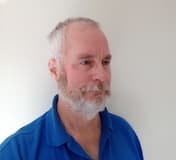
Geoff Crowley, galvanizing consultant
Crithwood Ltd.

Bathgate, Scotland, UK
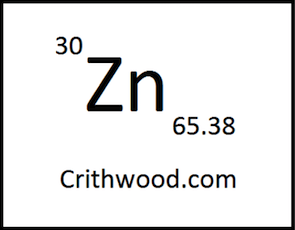
⇩ Related postings, oldest first ⇩
Q. I discovered during inspection of galvanized carbon steel structures the appearance of yellowish/greenish color. I approached the galvanizing shop and they replied:
"Sodium Dichromate is a chemical used as passivation. This chemical is used at the end of galvanizing process whereby it is used in quenching tank. Galvanized steel can form white rust whereby water (H2O) and zinc reacts quickly to form zinc hydroxide, a bulky white and relatively unstable oxide of zinc. This happens when freshly galvanized steel is exposed to water (rain, dew or condensation), in an oxygen deficient environment, the water will continue to react with the zinc and progressively consume the coating.
"The most common condition in which white rust occurs is with galvanized products that are nested together, tightly packed, or when water can penetrate between the items and remain for extended periods. The common solution by galvanizers for preventing white-rust is by re-passivation of the surface by treating the surface with a solution of 5% sodium dichromate.
"The appearance of galvanized steel after quenching with sodium dichromate will be yellowish in color but sometimes it look greenish. The color variation depends on the dilution of the solution. This layer can be easily removed because it doesn't have any chemical bond on the product.
It acts as protection layer from humidity. The layer can be removed by wiping it or clean it with high volume water jet."
Now my question is, is the yellowish/greenish color a process defect? How to eliminate the yellowish and greenish color? Cleaning with pressure jetting won't help me to remove the stains? How to explain to my client (oil company)?
Chen Sian Teck- Kuala Lumpur, Malaysia
April 4, 2012
April 6, 2012
A. Sir:
5% sodium dichromate is 50,000 ppm sodium dichromate. The usual sodium dichromate concentration of my clients is between 100 ppm and 500 ppm sodium dichromate. Also the pH of the dichromate tank MUST be held between about pH 4 and pH 4.5 or it will not properly function (adjust pH downward with very small amounts of HCl). The appearance of the SOLUTION is a very light yellow NOT ORANGE.
Sodium dichromate has hexavalent chrome in it which causes lung cancer. Thus if the dichromate tank is used to quench the product (cool it) then when the work is raised and is still hot MUCH hex chrome is released into the air. The situation in that galvanizing plant is quite bad. I did a full research study on this and video taped the results and there was 17,000% more hex chrome released (3 feet above the hex chrome tank) than allowed by OSHA. This was when the product was at 200° C.
Regards,
Galvanizing Consultant - Hot Springs, South Dakota, USA
A. Dear Sir,
A solution of 5% Dichromate (carcinogen) is a big health hazard to everyone, including you and your customers. Not to mention the colour stain it causes on your product. In a diluted solution, the colour stain will be minimum, and it is possible to wipe off the stain using just a wet cloth.
In recent years, there are many passivation products in the market which do not contain Dichromate. However, they are not popular in Malaysia due to availability, cost, effectiveness as well as the ease of maintenance.
It will be hard to explain to your client that their product is covered in carcinogen. If you are a big client of the galvanizer, request them to rework the product, and use a lower Dichromate concentration. If they refuse, then it's time to find another galvanizer. This time, make sure to indicate your terms on yellow stain prior galvanizing.
- Selangor, Malaysia
April 20, 2012
April 23, 2012
A. Sir:
On my recent trip I have come to realize that galvanizers within 1 mile of a salt body of water have an increased problem with "white rust." I am working on this problem.
Another question that I have NOT documented is whether using hydrochloric acid or sulfuric acid is more likely to produce white rust. I know with certainty that the time after fluxing until the product must be galvanized is about 1 hour in an HCl operation and as much as 12 hours in a plant using H2SO4.
Regards,
Galvanizing Consultant - Hot Springs, South Dakota, USA
April 25, 2012
A. Sir:
To quantify my previous response, I have evidence showing the major causes of white rust are:
1) The galvanizing plant is a short distance and down wind from a salt water body. Certainly within one mile can likely cause much white rust.
2) If a quench is used, allowing the dissolved contaminants to reach "high" levels like 3,000 to 5,000 ppm likely causes white rust. A cloudy quench (non-dissolved materials) is said to cause white rust.
3) Too high of aluminum in the zinc, for example above 0.003% likely causes white rust. Perhaps even 0.003% aluminum may cause white rust.
4) Levels around 0.1% bismuth likely causes white rust.
5) Low ACN and high baumé of the flux (European fluxing methods) likely cause white rust due to flux carry-over (e.g. excessive zinc chloride; "butter of zinc" which is a liquid at the galvanizing temperature) carries through the kettle to the quench tank or (in the case of no quench) remains on the product to collect moisture from the air.
6) Perhaps excessive tin in the zinc, which has been documented by Bablik as causing white rust and early corrosion.
7) Early exposure to rainwater which does not allow the galvanized coating to form a protective surface coating.
Not exposing the product to rain for 48 hours is said to prevent white rust.
8) Road salt or ocean transport are said to cause white rust.
9) Periodic heavy rain.
10) Air pollution.
11) Enclosing the product in air tight containers, especially packing the product (nesting) and not allowing the product to dry properly is said to cause white rust.
Currently there is no documentation that using HCl versus H2SO4 causes more or less white rust. After fluxing the maximum dwell time before galvanizing is about one hour for an HCl operation, whereas dwell time for an H2SO4 plant is in excess of 12 hours.
If readers have additional comments relating to white rust, please post them.
Regards, Dr. Thomas H. Cook, Hot Springs, South Dakota,USA
Galvanizing Consultant - Hot Springs, South Dakota, USA
![]() |
Hi. I know little about galvanizing, but regarding your mention of corrosiveness of HCl vs. H2SO4, please remember that HCl is not really a liquid, but a gas dissolved in water; it's vapor pressure is hundreds of times higher than that of H2SO4. HCl gas is readily released to the atmosphere upon agitation. Imagine it being champagne or ginger ale, and keep it quiescent to the maximum degree possible. Regards, ![]() Ted Mooney, P.E. RET Striving to live Aloha (Ted is available for instant or longterm help) finishing.com - Pine Beach, New Jersey |
Q. What would be an unacceptable solution for Passivation after galvanizing? What makes a post-galvanizing passivation solution acceptable or unacceptable?
K Kannan- Dubai, UAE
August 19, 2013
A. Hi K. I guess my answer is that an acceptable passivation solution deters white rust effectively while being relatively non-toxic, highly affordable, very easy to control, and without affecting the aesthetics. If you can provide context, a more carefully targeted answer may be possible. Good luck.
Regards,
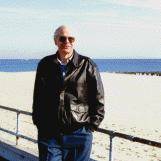
Ted Mooney, P.E.
Striving to live Aloha
(Ted is available for instant or longterm help)
finishing.com - Pine Beach, New Jersey
August 21, 2013
August 21, 2013
A. Most galvanizers in Europe passivate after galvanizing using sodium dichromate.
I have never heard of anyone using 5% strength in production situation. Under these conditions the galv would go dark brown. (have tried this under lab conditions)
Typical strength in a passivation tank which is also a quench tank, and operating at between 70 and 95 °C, is 0.02%
Tests by accredited testing regime shows no detectable Cr in the vapour (steam) above the tank.
Most galvanizers are seeking an alternative to Cr, but none that works is commercially available in Europe yet; though most international chemical suppliers say they are working hard to develop one. There are several on the market that do not work.
There appears not to be any known and generally used system to prevent white rust that does not use Cr.
There are many "old wives tales" of how to prevent white rust without passivation.
Galvanizing will form white rust if put into storage conditions that promote white rust, even after 1 year from galvanizing date.
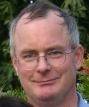
Geoff Crowley
Crithwood Ltd.
Westfield, Scotland, UK
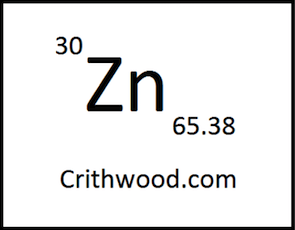
The color of the sodium dichromate passivation layer
Q. Please tell me if the color of passivation layer with chrome can be from yellow to brown. The dark color is a damage of passivation or is normal ?
The dark color of passivation provides increased protection of zinc coating against white rust?
It is some international references to this problem (color of passivation on zinc layer)?
Thank you for your answer
- Bucharest, Romania
January 16, 2014
January 20, 2014
A. There should be hardly any colour visible on finished galvanizing.
I'm assuming you are passivating hot immediately after galvanizing?
I remember many years ago, when we first passivated, the strength of the passivation chemical was added (by the supplier) at about 10x the required strength. The steel went brown. Subsequent dilutions got it right, and it's almost colourless, occasionally a just detectable yellow.
This helps prevent white rust, and is effective in our climate for about 6-8 weeks. It also preserves the bright shine that otherwise goes dull quite quickly.
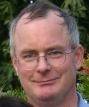
Geoff Crowley
Crithwood Ltd.
Westfield, Scotland, UK
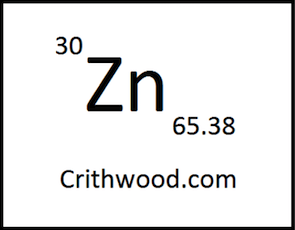
Q. We make handicraft products out of galvanized sheet and it goes without any further finishing. we just clean them and pack them.
Many times we face yellow staining on the sheet and we use Brasso
⇦ on
eBay
or
Amazon [affil link] to remove those stains. Although the stains get removed or come down, it takes lots of time. Is there any simple & faster process to make surface spot free? Just to remind we would not like that the spangle formation goes away or fades in the cleaning because the crystallized formation is required on our products
- NOIDA, UP, India
July 17, 2015
Q, A, or Comment on THIS thread -or- Start a NEW Thread