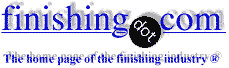
-----
Pitting of 2000 series aluminum from type II sulfuric anodize
March 15, 2012
Q. I really could use help determining root cause of a pitting issue during Type II sulfuric anodize of 2000 series aluminum (2014, 2024, and 2219 specifically).
Lately (the last 6 wks), we've had several lots of parts get scrapped out by one of our suppliers due to pitting (please see attached pictures). They claim nothing has changed in their process, and our manufacturing department says the same here. Where do I go next to find root cause, and stop this recurring issue? I'm familiar with the anodize process, but not enough to troubleshoot issues. Is there some way to identify what the brown stains are (chemical swab & reaction or spectro)?
Some parts have pitting only on specific surfaces, others are all over. One lot (according to the plating house) had one PN get pitted, and a different PN in the same bath turn out OK. We do not use cotton buffing wheels with compound, only Burr-tex or Scotch-brite wheels for light deburr, or die grinders [adv: die grinders on
eBay
or
Amazon [affil link] with various inserts. No sandpaper. Typically carbide inserts during CNC machining. I can investigate raw material certs, but have never seen something like this before.
Thanks for any help.
aerospace supplier - Hartford, Connecticut, USA
A. Racked on titanium with a stainless steel dye tank? Nitric Dip between anodize and dye? Chlorides? Free Acid? Dissolved alum? Current Density? Ramp Time to current? Tell us more.
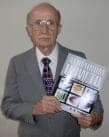
Robert H Probert
Robert H Probert Technical Services

Garner, North Carolina
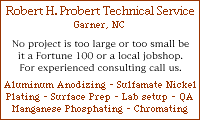
March 19, 2012
March 22, 2012
Q. Mr. Probert,
From our supplier:
Titanium racks
polypropylene tanks
no nitric dip between
chlorides - no
free acid - 170-180 g/L
dissolved alum - 4-10 g/L
current density - 12-13 ASF
ramp - 3 min
Thanks everyone for the help. I'm stumped.
aerospace supplier - Hartford, Connecticut, USA
A. The 2000's respond to a 5% nitric acid dip as in - anodize, rinse, 5% nitric,rinse, dye. Try it in a bucket. Also, because of the galvanic current between the titanium and (?) the stainless steel heater in the dye, remove a couple parts from the titanium rack and hang on stainless steel for dyeing. One or both of these two special requirements for 2000's should fix your problem. Sorry for being late getting back, had a gig out-of-state and did not hook up for a week.
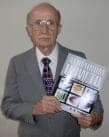
Robert H Probert
Robert H Probert Technical Services

Garner, North Carolina
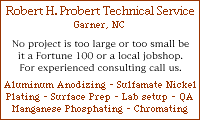
March 25, 2012
A. Especially for the 2000's and particularly for the 2014, you need a 5% nitric acid dip; anodize, then rinse, then 5% Nitric Acid 90 seconds, then rinse, then dye.
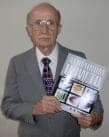
Robert H Probert
Robert H Probert Technical Services

Garner, North Carolina
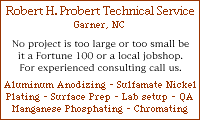
March 25, 2012
Q. Mr Probert,
Thanks for your response. I've forwarded it to our plater, and he thought stray current would be affecting other parts as well. There seems to be something about the sodium dichromate seal. Is that what you mean by "dye", as there is no additional dye step.
Thanks again.
Andris
- Hartford, Connecticut, USA
March 28, 2012
A. OK, so there is no "dye". Now go back and check the pH of the dichromate seal, look for chlorides in the make-up water and drag-in, and look for galvanic current between the titanium rack and the stainless steel dichromate tank.
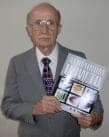
Robert H Probert
Robert H Probert Technical Services

Garner, North Carolina
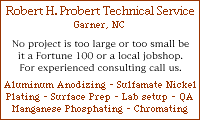
March 29, 2012
Q. Thank you again for your response. Our supplier tried it in their lab with fresh solution using a polypropylene tank with the same results.
We're also preparing test pieces from the same lot of material using the same machines -- raw bar, turned OD, turned & buffed, turned & tumbled. I'll share how that turns out.
- Hartford, Connecticut, USA
April 2, 2012
A. Hi Andris,
I am currently seeing the same problem, specifically with 2014 (strangely even 2024 and 2219 are not affected, just this one alloy).
We are looking at several potential causes, but the favourite theory at the moment is stray current, as Robert has suggested. We are currently seeing if isolating the titanium jigs will help or whether we may even go down the sacrificial metal route and use a bit of magnesium to potentially mop up any stray current. I have done this with dye tanks before, but never with a seal tank so it will be interesting to see what happens.
Another theory is that we may have a batch of 2014 with a higher than usual copper content, toward the 5% end of the specified range rather than the 3.9% and that the higher copper content is what is causing the problem.
Something else I have seen recently, as our cleaning and degreasing solutions have become less effective due to legislative changes is that tiny particles of aluminium have been left on the surface of the parts and caused a spark erosion effect. For us it meant having a much more robust cleaning regime, which solved that particular little problem. I just mentioned this one as your pictures look quite similar to the effects we saw.
Aerospace - Yeovil, Somerset, UK
April 4, 2012
Q. Very interesting. I'm battling a similar problem with small aluminum parts but 6000 series material.
How cleaning or degreasing process can affect the pitting?
We use ultrasonic cleaning 20% detergent, 80 % DI water, for 5 minutes at 30° C.
Could this formula be ineffective?
Please advise
- Goleta, California, USA
May 1, 2012
A. Richard
If you have not done so already, check the thickness of the coating on good vs. bad parts. The spots are somewhat characteristic of cut-outs (lost contact).
- Colorado Springs, Colorado
May 2, 2012
Q. Thank you for the feedback.
Would you willing to elaborate a bit more on what that really means. I'm on the receiving end of defective parts. I'm assuming the anodizing shop failed to control certain process parameters.
- Goleta, California
May 8, 2012
A. Richard
The 2 pitted parts appear to have a slight iridescence to them which to indicates to me that they lost contact during the anodize process; to anodize, the processor must make and maintain electrical contact with the part as the coating is an insulator. If the part moves on the rack during the process, it loses (likely) electrical contact and the anodize formation stops. When it stops, the acid (electrolyte) starts attacking the surface.
Parts that have lost contact will have a coating thickness less than those that did not. The processor should be able to measure the coating thickness in accordance with ASTM B244 using an Eddy Current device. If he does not have such a device, check with another finishing supplier. It is a relatively quick check to compare the thicknesses.
- Colorado Springs, Colorado
May 10, 2012
! Thank you so much for your help. Your feedback and analysis is very logical. I will work with my supplier and measure the thickness.
Richard
- Goleta, California
May 17, 2012
Q, A, or Comment on THIS thread -or- Start a NEW Thread