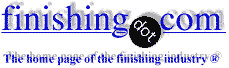
-----
Zinc-cobalt plating won't survive 96 hour salt spray without white rust
March 2, 2012
Q. Dear Sir,
We are in connectors manufacturing. We have a requirement of zinc-cobalt plating with 500 hrs of salt spray test. We are plating over aluminium, electroless nickel as base coat 4-5 microns, and zinc cobalt overcoat 12-14 microns, with olive green passivation. Aluminium grade 6061 T6
Specification: No white corrosion for 96 hrs and no base metal exposure after 500 hrs. Components should be heated to 150 degree for 1 hr prior to SST.
Components show white rust within 96 hrs of test. If we do not heat the component, the test passes. But during assembly line we will have to heat the component. Please give your valuable suggestions.
Thanks,
Manager Plating - PUNE, MAHARASTRA, INDIA
A. Hi, Kanlesh.
Please try to let the chromate cure for 24 hours before the heating and see what happens.
Regards,
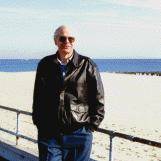
Ted Mooney, P.E.
Striving to live Aloha
(Ted can offer longterm or instant help)
finishing.com - Pine Beach, New Jersey
March 2, 2012
A. Hi
Added to Mr. Ted 's suggestion you can try introducing an inorganic sealant dip after passivation process and let allow for 24 hours to cure before heating the components.
(Of course, slight increase of cost will be there, but your problem can be solved)
Good Luck.
Vijendran
Pune, India
- Pune, India
First of two simultaneous responses -- March 10, 2012
Q. Dear Ted Mooney,
Thanks for reply. I have changed undercoat of high phos and submitted after 50 hrs of curing sample passes last week with 96 hrs. Same trials I am repeating and let you know. What is role of concentration of cobalt? We are maintaining 900 PPM. What is your suggestion for our requirement?
Thanks,
K.M.Bhatt.
- PUNE, MAHARASTRA, NDIA
Second of two simultaneous responses -- March 10, 2012
A. Hi, Kamlesh. I am not a formulator of plating baths and cannot answer your question. But I think you may be best served by sticking with proprietary electroless nickel baths as well.
Regards,
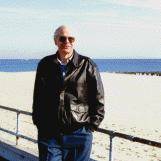
Ted Mooney, P.E.
Striving to live Aloha
(Ted can offer longterm or instant help)
finishing.com - Pine Beach, New Jersey
March 12, 2012
Dear Sir,
We have taken trials but results are not consistent. If we put for SST without heating it passes 350 hrs without any problem. But if we heat the components 150° then it may fail within 48 hrs. This components have another test of humidity with cyclic test.
Pl. suggest your comments.
Thanks,
K.M.Bhatt.
- PUNE/MAHARASTRA/INDIA
April 14, 2012
A. Hi, Kamlesh. It isn't clear whether you are saying that you have tried all the things that were suggested, and these are you new results, or whether you just blew it all off and posted the same question :-)
Please clarify which if any of the posted suggestions you have followed. Thanks!
Regards,
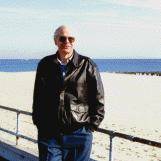
Ted Mooney, P.E.
Striving to live Aloha
(Ted can offer longterm or instant help)
finishing.com - Pine Beach, New Jersey
April 14, 2012
April 15, 2012
Dear Sir,
We have carried out SST after 48 hrs room temperature. Heating at 150 also after 48 hrs only. Generally after 48 hrs room temperature, how many hrs it should pass.
Thanks,
K.M.Bhatt.
- PUNE/MAHARASTRA/INDIA
A. Hi,Kamlesh. Your initially quoted spec of 96 hours to white rust and 500 hours to red rust sounds reasonable to me. Are you getting help from the process vendor who is supplying the zinc-cobalt process and the chromate? Generally, zinc alloy plating solutions require special chromates tailored to them rather than to plain zinc plating.
Regards,
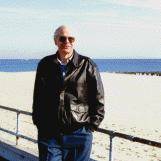
Ted Mooney, P.E.
Striving to live Aloha
(Ted can offer longterm or instant help)
finishing.com - Pine Beach, New Jersey
April 15, 2012
Q, A, or Comment on THIS thread -or- Start a NEW Thread