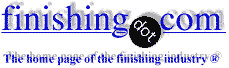
-----
Oil mark issue in satin nickel plating

Q. Hi everyone.
I need some help and advise on oil mark problem in satin nickel plating.
We plate a small ABS plastic part. After plating in satin nickel, we found that a lot of oil mark NC.
Base on our experience & know-how about satin nickel, we have done few step/counter measure to eliminate this problem like do carbon treatment & peroxide treatment on satin-Ni solution to remove aging additive, adjust the satin additive dilution factor, clean plating tank & water rinse tank with special chemical and do an additional filtration/treatment with filter aid to the satin nickel bath. But this matter still unresolved.
Please give some idea on the other things that are possible to look into or maybe I can't see to solve this matter. Thank you.
- Malaysia
February 21, 2012
A. If you feel that you are not getting oil from the plating tank, take a very hard look at the tanks ahead of the plating tanks. It is not uncommon to have an oil slick on one or more and it will carry over to follow on tanks.
James Watts- Navarre, Florida
A. As per my experience of Satin nickel process, the excess of brightener in addition to non removal of satinizer are the two causes of oily satin marks & Bright star pits.
To remove the excess, follow the below process:
1. Decant the solution & clean the tank & anode bags by leaching using H2SO4 diluted solution.
2. Do activated carbon filter pack for 6 hours twice one after another.
3. Do H2O2 treatment with agitation & remove excess by evaporation at 60 °C
4. Adjust pH & other constituents by addition & run filter again.
5. Do Hull Cell
⇦ huh?
analysis to find out if any broken down satinizer is left or not.
6. If OK, the panel must be brighter, add satinizer off line in a vessel containing satin nickel electrolytic solution and mix by using electrical stirrer for 45 min.
7. Now add stirred solution to satin bath with movement of solution largely to make it homogeneous.
8. Keep it silent or in rest for 15 min and use it for plating
9. Now add stirred satinizer
- Noida India
February 25, 2024
A. You have to do hydrogen peroxide treatment at 140-150 °F temperature; you can use 1 gal hydrogen peroxide per 1000 gal tank solution. After hydrogen peroxide addition, air agitation 30-40 minutes.
Need to do full carbon treatment of your nickel bath after hydrogen peroxide treatment. Find the source oil is coming from (automatic hoist system wheel lubrication with grease? sometimes grease goes into process tank.
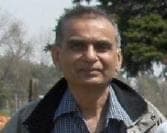
Popatbhai B. Patel
electroplating consultant - Roseville, Michigan
April 4, 2024
Q, A, or Comment on THIS thread -or- Start a NEW Thread