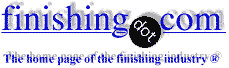
-----
Immersion Silver solderability issues
Q. This is a good one. We are experiencing non-wetting, de-wetting, and at large amount of voiding on our RF technology boards. the boards are 10 to twenty layers, RF typical topology lots of planes. lots of stitching vias for grounding. Lots of QFN and BTC components. We had success early in the project but after some process changes (unknown) we are dealing with the solderability issues.
We have done all of the typical surface contamination tests with negative results. the bare boards fail the straight j-std-003 solderability tests, but we get better results by preheating and increasing dwell times.
Unfortunately we are still seeing massive voids under the QFN packages and in lead joints as well as wide spread wetting issues.
We have tried measuring the profiles over various runs with limited positive results.
We observe the issues on boards from various manufacturers which leads me to believe it's not a surface contamination issue.
Any ideas
- Middetown, New Jersey
February 19, 2012
March 18, 2012
Hello John,
The company I now work for offers ImAg as a final finish on complex PCBs. There are a few questions you can ask your vendors. What is the thickness of the Ag deposit? There have been better solderability results with lower thicknesses of the Ag deposit. What works for us is 8-12 microinches thickness. We have also found that improved rinsing and panel rack vibration prior to and after the micro etch process. This helps in the release of entrapped organics or air bubbles. The Immersion Ag solution normally has a built-in anti tarnish component so shelf life of the board can be increased. Unfortunately there is not just one cause of this defect, I can only share info that has worked for us. Good Luck,
Engineering - Mesa, Arizona, USA
Q, A, or Comment on THIS thread -or- Start a NEW Thread