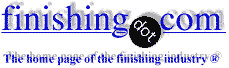
-----
Can't get chrome plating to adhere to sandblasted copper
Q. I HAVE TRIED SEVERAL TIMES TO SAND BLAST COPPER SURFACE TO ATTAIN CERTAIN SURFACE FINISH PRIOR TO CHROME PLATING, BUT AFTER SAND BLASTING THE CHROME DOES NOT ADHERE TO THE PLATING SURFACE.
IS THERE ANY SORT OF SILICA FILM FORMED ON SAND BLASTED SURFACE?
IS IT BETTER TO SHOT BLAST?
WHAT IS THE BEST ALTERNATIVE?
director production - KOLKATA, INDIA
January 25, 2012
Hi,
We've experienced adhesion problems with grit blasting as pretreatment on relatively soft 4140 steel. SEM analyses showed that over 20% of the surface showed embedded grit. We solved the problem by applying a 45% H2SO4 / 5% HF anodic etch after grit blasting, prior to e-nickel plating.
Embedded grit is most likely your problem as well.
Best regards,
Jeroen
- Geldrop, Netherlands
January 30, 2012
January 31, 2012
For ferrous metals, I have used aluminum oxide for blast material as most of the embedded material will dissolve in an alkaline cleaning solution, especially an electrolytic cleaner.
I do not like sand as it frequently is poorly sized, breaks down fast and in the USA causes precautions to prevent silicosis. EPA and OSHA are big on this. Cheaper material can have variable amounts of contaminants.
What is the level of copper in your tank?
- Navarre, Florida
February 1, 2012
Hello James,
We have done a lot of tests to find a way to get rid of embedded Al2O3. Alkaline did not solve this problem. Chemically seen it should dissolve, but corundum does not (at all), was our experience.
best regards,
Jeroen
- Geldrop, Netherlands
February 6, 2012
Hi ! The problem is that you incorporate silicon particles when you sandblast your surface, which causes the lack of adherence. 2 solutions :
1) You can remove the silicium by using an acid dip solution containing fluoride. You can use NH5F2 at a 100 g/L concentration
2) You can sandblast the surface with conducting particles. Best is to use bronze powder which will give you the same finish as sand.
Best regards ;)
- France
Q, A, or Comment on THIS thread -or- Start a NEW Thread