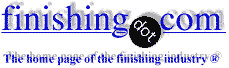
-----
How to Make or Buy Gold Glazed Mirrors.
I am a sculptor and need about 12 square feet of gold mirror float glass 2 mm thick (could use 4mm). I have had a potter working off and on for the past year to try and glaze gold onto window glass but she cannot obtain consistent results. Do you know of anyone who could supply this material and if not do you know how a potter could accomplish it - type of glass, gold glaze, firing temperature, etc? I wish to cut the gold glass into 2 cm square pieces and cement them on to a concrete sculpture as a mosaic. Hugh Cunningham.
Hugh Cunningham- Canada
2000
I have had some exposure to the craft of telescope making, in which reflectors are hand- (or machine-) ground and polished from glass (which I believe is usually quartz, but I don't think it matters), and afterward coated with metal to create a mirrored surface. The most common choice of metal is aluminum because it is highly reflective across the visible spectrum, but gold is also used by those who interested in infrared astronomy; other metals are also used for various specialized purposes. Whatever the choice of metal, the coating is always done by means of "sputtering." In brief, sputtering is done as follows:
First, the carefully cleaned glass is placed inside of a vacuum chamber, which is evacuated. Next, a small sample of the given metal is heated electrically in (a small "pot" within the vacuum chamber) to well within its liquid regime (i.e., above its melting point but below its boiling point in vacuum). The metal is held at this temperature, allowing some of the metal to evaporate. As the glass sits bathed in metal vapor, metal gradually condenses onto its surface (and all other exposed surfaces within the chamber) due to the fact that it is well below the temperature of the metal in the pot. The system is held in this state for a length of time determined by the desired thickness of the coating -- the longer the wait, the thicker the metallic layer becomes. At the end of the process, the heat is removed from the pot, the chamber is brought up to atmosphere and opened, and the mirror is removed.
This is such a specialized process that almost no one does it themselves. Rather, most small-volume telescope makers send out their reflectors (already ground and polished) to a company that specializes in silvering reflectors. An example of such a company is H. L. Clausing, there may be other companies closer to you, or you can ship your pieces to them.
Be aware that gold is a very soft metal, and a gold coating will be exceedingly easily scratched. You may want to consider another coating with gold-like coloration, or else have the piece overcoated with a protective layer. These are things you can discuss with the people at the coating company.
I hope this helps!
- Urbana, Illinois, USA
2002
Q, A, or Comment on THIS thread -or- Start a NEW Thread