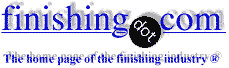
-----
Chrome on Nickel Blisters on Termination
Trying to plate chrome onto nickel sulphamate layer, which has, in turn been plated onto a heat-treated steel. The idea is that the nickel helps the chrome not to crack and fall off. However, after plating, approximately 75 per cent of the time the chrome has blistered/laminated on the nickel steel termination. I am beginning to think maybe its just luck - but there must be an explanation as sometimes it works and other times it does not. Prior to plating the items/ pins are anodically cleaned in an alkaline bath, then sulfuric etched and scoured, finally the pin is loaded live into a vat and struck. This process is repeated may times, but only very few appear to be successful
John Ford- Dursley, England
2000
Just a quick first question: you are rack plating these, not trying to barrel plate them, right?
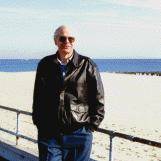
Ted Mooney, P.E.
Striving to live Aloha
(Ted can offer longterm or instant help)
finishing.com - Pine Beach, New Jersey
2000
Ted,
The items in question are pins, they are plated on 3 amps per square inch (approx.), and their sizes are approx 24 inches long with a diameter of 9 inches, so each one is hard chrome plated at approximately 1000 amps, I would mention that the process covers both the nickel and the steel, the steel being on each ends of the pin and of an area of approx. 1/2 an inch in area, we strike the pins on approximately 2000 amps and was wondering if, when the nickel is being plated with the power whether the gas (hydrogen), would be having a masking effect on the steel substrate? Thus causing a blister? This is the only explanation I can come up with. Would you think you need a strike on a pin mostly covered with nickel, with steel terminations at both ends, as these are high current density areas anyway thus no requirement for a strike?
- Dursley, England
2000
A lot of angels could dance on the head of those pins; now knowing their size, they obviously are not barrel plated.
Are you sure the reason for nickel striking them is to promote adhesion? I am not familiar with that at all. But chrome plating does not offer much corrosion resistance, so it would be understandable to nickel plate a part for corrosion protection.
My suspicion, if there is an adhesion problem along the steel-nickel interface, is that a machining operation that may be done there is the problem, or some remnant of masking is causing the problem.
Many people worry that hydrogen gas 'masks' plating, and I'm still not sure that I am properly visualizing the part, but I have never seen evolution of hydrogen gas 'mask' plating or contribute to a thinner plate, or anything like that. I still say I am not aware of this whole concept of nickel plating to promote adhesion, and I question it.
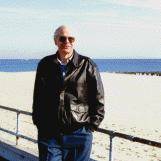
Ted Mooney, P.E.
Striving to live Aloha
(Ted can offer longterm or instant help)
finishing.com - Pine Beach, New Jersey
2000
Q, A, or Comment on THIS thread -or- Start a NEW Thread