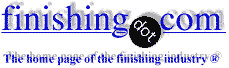
-----
Removing heat treated electroless nickel
October 4, 2011
BIG PROBLEM!!!
We had A-2 tool steel hardened to 58 Rc then E.N. plated. Found two 4-40 holes that weren't tapped. We annealed the parts, with the plating still on. When we got them back the parts were grey so I thought the plating burned off. We then tapped the two holes and had the parts re hardened. When we got them back they were once again shiny and I could tell the plating was still on, plus when at tempering temperature I think the plating liquified and ran into some 4-40 tapped holes. The plater thought he could chemically strip the plating, however it had no effect on the plating. He thinks it was due to the heat treating, he said the chemical stripping always works.
If I send them back through an anneal process will it soften the plating to the point that it can be removed, or has it now become part of the parent material with no chance of removing it? I really don't want to remake these 19 pieces, it will become a few thousand dollar loss, which we can't afford.
machine shop foreman - Lansdale, Pennsylvania, USA
October 7, 2011
Annealing will not soften the plating, on the contrary. EN hardens by a process called precipitation, which is the formation at high temperature of hard particles (nickel phosphide) from a previous softer matrix of phosphorous and nickel. This is actually the reverse process that softens steel during annealing, which dissolves hard carbide particles back to the original soup of iron, carbon, chrome, etc.
Something else, the melting point of EN is close to 1,000° C (1,832° F). If you reach this temperature it will not sweat and drip, instead, diffusion will take place and it will penetrate into your parts.
Your chances are to use a TiN coated tap or insist on the chemical stripper giving it a brief reverse current strike with hydrochloric acid. This may help leave a strippable plate. Good luck,
Guillermo (Bill) Marrufo-Mexico
Monterrey, NL, Mexico
I have seen this problem many times on high phos electroless nickel applied to jet engine parts. It can take days to strip the high temp baked electroless nickel in a standard cyanide or alkaline non-cyanide nickel stripper. However, there is an electrolytic chromated stripper called END Plate that strips electroless nickel at 3 mils per hour and eliminates regular tank solution disposal costs. The stripper is made by a small company in Phoenix, AZ called ACRA+.
Don Davis- Tulsa, Oklahoma, USA
November 3, 2011
Thanks, Don.
I understand the comment on stripping, but don't quite know what you mean about "eliminates regular tank solution disposal . . ."
Regards,
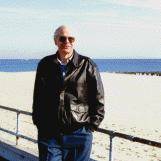
Ted Mooney, P.E.
Striving to live Aloha
(Ted can offer longterm or instant help)
finishing.com - Pine Beach, New Jersey
November 3, 2011
First of two simultaneous responses -- November 4, 2011
Don,
do you have any more information on the "end plate"? I have not been able to find that acra+ company anywhere.
Thanks, Chris
Plating - York, Pennsylvania
----
Ed. note: Use "Acra Plus Phoenix" in your search engine, folks.
Cyanide nickel strip and eco-friendly non-cyanide nickel strips have relatively short lives. If you run the bath 24/7 you are looking at 3 months to a year depending on temperature and the loading. Then you have make up a new tank and dispose of the dead solution. At this point in time, I don't know if the END Plate solution ever has to be replaced. The only down side of the stripper is it's chromated and can only be used by shops set up for a with a chrome capture system.
Don Davis- Tulsa, Oklahoma, USA
Second of two simultaneous responses -- November 4, 2011
Q, A, or Comment on THIS thread -or- Start a NEW Thread