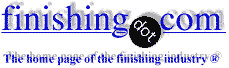
-----
Rust on 303 ss after passivation
Hi, my name is Jill and I am a Quality manager. We are seeing parts come back from the passivation process that are showing signs of rust within a day or two after passivation. What could be causing this?
Jill DechertQuality Manager - Reading, Pennsylvania, USA
August 31, 2011
Steel or iron embedded in the surface is the normal cause. Passivation will only remove a portion of it.
If you want a problem that can never be solved, use a 410 rotary brush on a quality SS. It will look like it has the measles in a few hours of salt spray. Yes, even on high nickel and 316LSS.
- Navarre, Florida
First of two simultaneous responses -- September 2, 2011
Jill,
Could you please share with us what passivation process you are using, including parameters such as immersion time, bath temperature, acid concentration, and any pretreatments you are doing?
Also be aware that 303 is a high sulfur grade (to improve machinability) and oftentimes the appearance of rust on the surface of parts is not iron oxide at all but actually sulfur bleeding out.
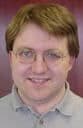
Ray Kremer
Stellar Solutions, Inc.

McHenry, Illinois
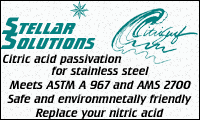
Second of two simultaneous responses -- September 2, 2011
September 7, 2011
Hi Ray, appreciate the feedback. Here is the process used by our outside passivator.
Cleaning Process:
Alkaline electroclean - Trimax279, 1-3 %volume 279, 3-9% by volume LC-B, 160-180 degrees F. 20-40 amps per square foot, 3-5 minute immersion.
RINSE - Ambient temperature, 1- 2 gallons per minute, 20 second - 1 minute immersion.
HYDROCHLORIC ACID - 40%, ambient temperature, 30 seconds -3 minute immersion time.
RINSE - Ambient temperature, 20 second - 1 minute immersion time.
RINSE - Ambient temperature, 20 second - 1 minute immersion time.
Passivate:
TYPE II & VI -20 -45% Nitric acid, 70-90 degrees F, 30 - 50 minute immersion
- Reading, Pennsylvania
September 29, 2011
Jill,
Alkaline pretreatment is good.
The grade vs. bath chart in QQ-P-35 assigns only type II, not type VI, to 303, but I suspect that type VI is probably okay. citric acid based passivation works well also.
I assume there are some rinses after the passivation bath that you just left off your list.
I don't recommend the use of hydrochloric acid on stainless steel.
All things considered this should be a decent process. I think you need to determine if you have an iron oxide problem or a sulfur problem. You can usually tell the difference under magnification, rust looks jagged while sulfur looks blobby. Or dip a part in alkaline cleaner (pH of 11 or so), if the brown stains go away, it is sulfur.
Let us know if we can help you.
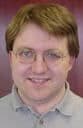
Ray Kremer
Stellar Solutions, Inc.

McHenry, Illinois
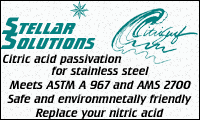
Q, A, or Comment on THIS thread -or- Start a NEW Thread