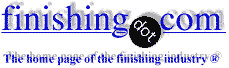
-----
Looking for best corrosion resistant finish for aluminum
My business builds prototypes. In this case, an aluminum tower for marine use, made of 6063 alloy pipe. We are considering finish processes, and find the on-line information confusing, often obviously biased according to what the company sells. Our primary concern is corrosion resistance in a salt-spray environment. We need a uniform appearance, reasonable abrasion resistance, UV stability and reasonable chemical resistance (normal cleaning) but primarily a long-term salt corrosion resistance. This tower bolts to a deck. It is never underwater, but always subject to spray.
At this point we assume anodizing is the best process, powder-coat the second best, and a topical process the third. Problem is that all have a variety of options and little consensus on what really works.
We have found that cleaning processes with fluoride content are consistently endorsed, but little else seems like reliable information.
Any help for a process that would be reliable and reasonable to do and any product or service company that could provide them would be appreciated!
Thanks-
Call me spiritgide...
Prototype design/builder - Wichita Kansas USA
August 22, 2011
Hi Don,
Personally I would go with a sulfuric acid anodise (check out MIL-A-8625 Type II for details) followed by a primer and topcoat paint, probably a polyurethane. This way you can colour match (check out FED-STD-595, lots of colours to choose from in gloss, semi-gloss and matt) and have good corrosion resistance.
Aerospace - Yeovil, Somerset, UK
August 23, 2011
August 24, 2011
Hi Don
As Brian stated, anodise, prime and polyurethane finish.
Chromic acid anodising is a possible alternative to the type II in Mil A 8625. Really depends on the service conditions for the parts involved. Both offer excellent corrosion resistance.
The sulfuric process gives a thicker coating but is less flexible than its chromic counterpart and can give rise to micro-cracks if the component moves too much in service. something to bear in mind.
- Chelmsford, Essex, United Kingdom
Alodine EC2 would be a suitable protective coating having excellent corrosion performance to salt water.
John Farrow- New Zealand
October 11, 2011
----
Ed. note: Readers -- please offer generic names and descriptions of processes, not trade names for proprietary formulas. This site is for technical education and camaraderie and is made possible by supporting advertisers.
Q, A, or Comment on THIS thread -or- Start a NEW Thread