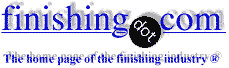
-----
Corrosion resistance of Galvanized vs. Media Blast Steel?
July 21, 2011
Currently powder coating over steel tubes- galvanized with clear coat lacquer.
Looking to media blast to solve a surface contamination defect.
Looking for data regarding galvanized tube salt fog hours versus media blasted steel?
Engineer - Plymouth
July 24, 2011
Dear Matt,
I note from private correspondence that your company offers a 15 year warranty for steel by using galvanized metal. By substituting this with a shot-blast substrate without a phosphate pre-treatment you would have to reduce your warranty if superficial damage to the top coat is anticipated to close on 2 years. In my opinion, by incorporating an iron phos you would still not be able to increase the warranty time. Alternatively, by substituting zinc phos you may be able to offer a 10 year warranty.
I understand that sources have come to the conclusion that the defects you are experiencing are due to out-gassing, the cause of which are the capillaries or dendrites that are being formed at the galvanizing stage. This is normally due to the lack of rapid cooling of the galvanized items at the final stage of processing. This slow cooling process allows the formation of chimney's (dendrites) that go all the way to the surface. Unfortunately, as you are aware, unless you take some form of preventative measures, surface defects will appear in the top-coat after the baking process. I gather that you have been advised not to pre-heat prior to applying the powder as this pushes any formed dendrites that are not close to the surface further towards the upper surface of the galvanized item.
I believe that you have several other options worthy of your evaluation that still allow you to use a galvanized substrate -
a) Add an anti-gassing agent to your polyester powder.
b) Use of a specifically formulated anti-gassing epoxy powder primer where coloured powders are used.
Note - most primers are formulated for their anti corrosive properties.
c) Evaluate an alternative galv tube supplier whose process incorporates a quick quench operation.
This is the most important point for, as I understand, the aforementioned capillaries in some cases protrude above the surface of the galvanized surface requiring you to hand sand the galv in an effort to eliminate the surface defects.
I will contact you direct with some images to illustrate the importance of pre-treatments.
Birmingham, United Kingdom
September 23, 2011
Hello Terry,
Our company (powder coating) is experiencing many problems due to the outgassing of galvanised items. I was able to observe by means of a metallographic microscope the cross section of one of this pieces, and I saw this huge dendrites (up to 300-microns!) grown to the surface with little or no pure zinc phase visible. We tried and preheat the pieces (180-200ØÌÛ) before powder coating them, but without results. I read from your previous answer that preheating such pieces could actually led to a worsening of the situation, did I get that right?
Thank you very much
Anna
Engineer - Berlin, Germany
September 27, 2011
Dear Anna,
It my understanding that contrary to most powder applicators use of pre-heating in an effort to overcome out-gassing, it has a tendency to exacerbate the problem. Please contact me direct for a possible solution to your problem.
Terry
Birmingham, United Kingdom
First of two simultaneous responses -- September 28, 2011
Removing layers of cured powder I started to see a trend of discoloration under the defect areas. Usually a black and or reddish brown.
This directed my attention towards a mechanical surface prep to determine if I could remove this substance before painting. My initial (small sample size)test was successful. Blasting is tricky because, as you mentioned in your response, that we have 3 layers on our tubes. Removing the 1st 2 should be ok but I do not know how much of the galv can be removed before our longterm corrosion protection is compromised. What I am experimenting with is more of a brush blast than a full 2 mil profile blast.
Just looking for anyone who had some experience with salt fog data on this subject as I submit my samples to be tested this week.
- Delano, Minnesota, USA
Second of two simultaneous responses -- September 28, 2011
I would be extremely interested in Geoff Crowley's comments on this thread.
Traditionally, Powdercoaters have always used an outgassing pre-cook usually about 20 °C above cure temp to drive gasses out prior to cool, pretreat, coat & cure.
I agree it does not always work.
I do take issue with the recommendation to "quick quench" prior to powdercoat.
We are all here to learn however, especially me.
My ears are very keen on this subject.
My understanding is that most Galvanisers use a dilute Sodium Di-Chromate solution to "quick quench" thus providing some short term protection against white rust.
This same solution is an absolute p..n i. t.e a.s for Powdercoaters.
In my Country, several of the Galv Tube Suppliers attempted to introduce clear coated galvanised tubing for on-processing by Powdercoaters.
Each and every-one failed.
They simply failed to understand that it is essential to hit the Gal surface with an appropriate Chemical pre-treat prior to Powdercoat.
Their clear coats simply impeded this process.
Again, I really am anxious for Geoff's comments on this thread.
Regards,
Bill
Trainer - Salamander Bay, Australia
September 28, 2011
I think my original response is not clear re "quick quench". My understanding is "quick quench" refers to the time lag between the galvanising process and reducing that item back down to a temperature for safe handling. This, in theory prevents any further defects being created as the galvanised inner core has been made immobile whereas a slower reduction in temp will allow the formation of defects to continue.
I agree with the point that sealing by the galvanizing company prior to PC can be a problem that is why I suggested a powder primer that stays open during the initial PC bake to allow the gases to escape-- most powder primers are formulated for their anti corrosion properties and not for prevention of out-gassing. The primer I am thinking of was developed for the alloy wheel industry but has found favour due to its anti gassing properties when used in conjunction with galv metals. A waterborne primer will give similar results.
Birmingham, United Kingdom
Q, A, or Comment on THIS thread -or- Start a NEW Thread