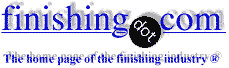
-----
Blisters develop when using old electroless nickel plating solution
hi my name its Lou Marin. I have a major problem with my electroless nickel, the problem is that after awhile using my electroless nickel I start getting these small blisters... well my question its what do do you guys recommend for fixing my problem thank you.
Lou Marinplating shop employee - Rialto, California, United States
June 19, 2011
Blisters generally come from two combined factors: a) insufficient adhesion and b) abnormal compressive stress in the plate. The sum of these produce the effect. Adhesion is dependent on correct pre-treatment more than anything else, but as I understand, the pre-treatment does not seem to be the culprit since you imply that the problems only appear with this bath. Of course, an old plating bath may also be contaminated with floating oil, metals, other organics or what have you, not only aged. This may leave undesirable residues on the parts during immersion. An aged bath may also take too long to react allowing the surfaces to re-passivate or immersion plate. On the other hand, stress is mainly due to the plating solution itself. A good EN bath renders almost zero stress. The only thing you can do yourself is filter, raise the A+B additives and temp to the maximum. Perhaps take some parts just a few moments after reaction starts to see if there is anything abnormal on the surface. Guillermo Marrufo- Monterrey, Mexico
Guillermo MarrufoMonterrey, NL, Mexico
First of two simultaneous responses -- June 27, 2011
Second of two simultaneous responses -- June 27, 2011
Assuming that all parameters are precise and in the range, EN solution age normally does not produce blisters. Typically, it slows down the plate rate or looses its brightness. It does affect the nickel plate phosphorous percentage on many formulations, but only a few platers can check that and few care.
The cleanliness and or activation has a lot more to do with it if it is on steel.
If it is on aluminum, then the zincate is the major factor and it really requires an alkaline EN strike to get a better plate and to prevent premature damage to the EN solution.
- Navarre, Florida
How old is the old solution? How many MTO?
Do you plate on steel or aluminum?
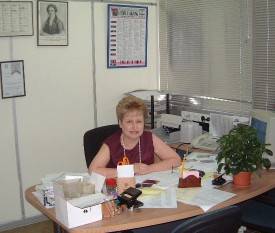

Sara Michaeli
Tel-Aviv-Yafo, Israel
July 5, 2011
I hate to disagree with James Watts, because it probably means I'm wrong, but I've often had blistering problems with EN over Al when the EN bath was old, say 8 MTOs. Even though the chemistry, plating rate and appearance were okay, the only remedy I've found is to replace the bath
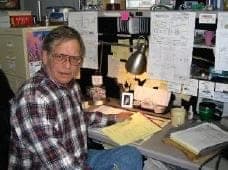
Jeffrey Holmes, CEF
Spartanburg, South Carolina
July 12, 2011
July 13, 2011
Hi Jeffrey,
For many platers, 8 MTO's is impossible to achieve because they abuse the solution. Typical is nothing in the tank over lunch or on start up, massive adds vs small ones, poor pre steps, excessive drag in and etc. Some have problems because it takes weeks to get 8 MTO's. Trash metal ions is another problem.Plate rate would normally be on the low end or compensated by an excess of reducer or high Ph or high temp. Aluminum is not as forgiving as steel and a lot of platers do not do a great job on the zincate step and do not use an alkaline stike.
Blisters will normally come from poor maintenance as much as turn overs.
Most platers can not complain if they get 8 MTO's, but the ones that take care of the tank and have a high thruput get more than 10.
- Navarre, Florida
8 MTO on Aluminum is very good.
The problem with Aluminum is the accumulation of zinc coming from the zincate.
Some supply houses have special additives which "mask" the effect of the zinc.
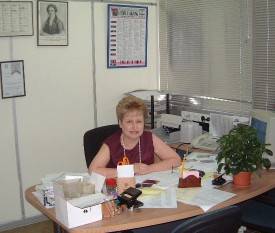

Sara Michaeli
Tel-Aviv-Yafo, Israel
July 18, 2011
Q, A, or Comment on THIS thread -or- Start a NEW Thread