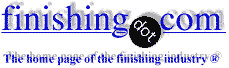
-----
PASSIVATION PROBLEM
June 9, 2011
My name is Aaron Stinson. I am the Quality Manager and NDT Level III at a metal finishing shop in Vonore TN. We are currently trying passivation using 20% Nitric + 2% hydrofluoric on stainless (440)tanks. The smooth parts of the tank look very good and pass copper sulphate
⇦ on
eBay or
Amazon [affil link] testing however the welds that bond the top and bottom of the tank appear black and smutty. I could really use some advice on this issue as our customer is awaiting verification of successful processing. Here is the process we are using:
Alkaline clean 130 degrees/10 mins
rinse 9(GRAY)
rinse (clean)
pickle 20% HNO3 + 2% HF at 100 degrees for 120 MINS (ASTM A967-05 AND ASTM A380
-06)
rinse
rinse
spray fresh rinse
Any help is greatly appreciated !!!!
Quality Manager/NDT Level III - Vonore, Tennessee, USA
Hi, Aaron.
To my knowledge, pickling and passivation are not the same thing and cannot be done simultaneously. Again to my knowledge HF has no role in passivation except to mess it up :-) Are you sure that ASTM A967 permits HF in the passivation solutions?
Regards,
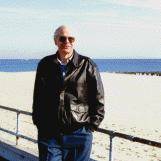
Ted Mooney, P.E.
Striving to live Aloha
(Ted is available for instant or longterm help)
finishing.com - Pine Beach, New Jersey
June 10, 2011
![]() |
Ted, nitric/HF pickling of stainless steel is useful as an alternative to nitric passivation for welded parts. The HF in the mix does aid in cleaning the weld scale much better than nitric alone. Aaron, the fact of the matter is that welded areas are just tougher to passivate. You can try increasing your time or processing twice. Even better would be to grit blast, mechanically polish, or apply pickling paste to the weld scale areas before you do the chem processing. After that, you'll have a nicely passive part. There may be some citric acid alternatives, but I would defer to Ray Kremer at Stellar Solutions [a finishing.com supporting advertiser] for that advice. ![]() Jon Barrows, MSF, EHSSC Kansas City June 10, 2011 Yes and actually says that is the most common solution for for stainless. It also has a table with times, percentages, and temperature specifically for nitric/ hydrofluoric. I'm at a loss now? Aaron Stinson- Vonore Tennessee USA June 13, 2011 |
June 14, 2011
Jon gave you the right advice how to clean the welding area first before passivating/cleaning the whole tank. However there is a danger that by grinding, sandblasting the only welded areas, you can damage the polished surface of the tank.
The problem with smutty areas may be also in not enough duration of treatment. Maybe those spots indicate that not all oxides are removed from the welded area.
Also it is a good idea to separate etching step from passivating step when you have problem areas. Rinsing with nitric acid solution afterwards is a god idea.
However there is a danger that the passivating solution you are using, does not have enough passivating strength on that particular areas after welding. This is because the stainless steel changes in structure and composition of the heat-treated places may cause such effects, that welded areas behave more like high-carbon steel (that is why you may see the dark spots where more etching than passivating takes place). In this case change the composition of the solution by decreasing HF percentage. How much HF reduction should be - is hard to predict - do testing on a small area.
Another way to avoid such problem is to use electrolytes that are more passivator with milder etching agent. Such solutions work longer, however they never etch the surface, but only remove metal oxides. But in each particular case testing is required.
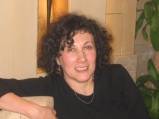
Anna Berkovich
Russamer Lab

Pittsburgh, Pennsylvania
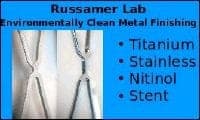
Hi Aaron
I would also check out the weld. Was it MIG. TIG, arc etc? Was the filler rod of the correct type?
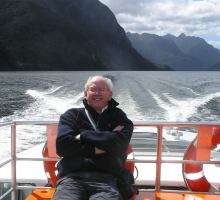
Geoff Smith
Hampshire, England
June 17, 2011
June 29, 2011
Hello Aaron,
We use a weld cleaning machine that cleans and passivates the welds prior to passivating the whole piece. This seems to do the job for us and makes our pieces look great.
If you are interested in knowing the manufacturer ask Ted for my contact information.
Sincerely,
- Rincon, Georgia
In my experience this sort of thing depends on the quality of the weld. If your chemical treatment isn't getting you what you need then you might want to consider grinding it or using an electrochemical cleaning method to get it looking nice prior to your acid bath.
This is of course always necessary when passivating with citric acid as you don't get any pickling action at all. With a nitric passivation bath you do get some pickling effect, enough to chew off most weld and heat treat discolorations.
As for counting on a nitric/HF pickle bath for passivation, I'm sure it's better than nothing, but Ted is correct, traditional nitric passivation baths do not use HF. It would be interesting to see a study comparing the passivation effects of a nitric/HF pickle bath versus an A967 nitric passivation bath. Probably the HF etches the surface, undermining the passivation, but then the nitric acid itself does so also to some extent.
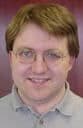
Ray Kremer
Stellar Solutions, Inc.

McHenry, Illinois
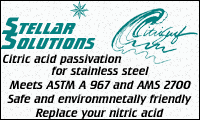
July 6, 2011

this text gets replaced with bannerText
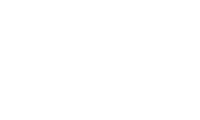
Q, A, or Comment on THIS thread -or- Start a NEW Thread