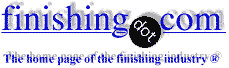
-----
Need a high friction coating

Q. I am looking for a way to increase the friction coefficient of steel or stainless steel washers. The hardness of the parts is about 40Rc. My current parts have a coeff. of about 0.2 and I would like to increase this by as much as possible. 0.4 or 0.5 would be ideal.
Ideally, this will be a relatively low cost mass finishing process. Parts will range in diameter from about 0.50 to 3.00 in.
Is there a plating, surface treatment, or conversion coating that can be used to achieve high friction?
- Cleveland, Ohio
September 30, 2022
Tip: This forum was created to help build camaraderie through sharing tips, opinions, pics & personalities.
The operator & those readers who want that might not engage with anonymous posters.
A. We appended your inquiry to a thread which offers lots of good ideas ranging from simple mechanical finishing to more exotic coating with diamond-impregnated nickel plating where the diamond dust digs into the opposing surface for very high friction. Feel free to follow up with more detailed questions about these proposed solutions.
Luck & Regards,
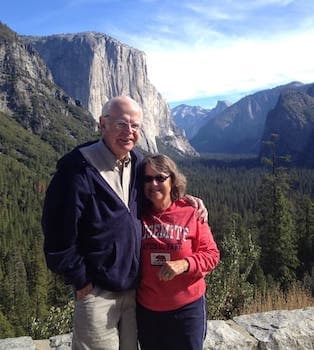
Ted Mooney, P.E. RET
Striving to live Aloha
(Ted can offer longterm or instant help)
finishing.com - Pine Beach, New Jersey
⇩ Related postings, oldest first ⇩
Q. I am looking for some material with high friction coefficient with some finishes metal surfaces like car bodies. Could you give me some suggestions? The material needs to be easy to find and low cost and hopefully can hold the friction well under wet conditions (say 60%+). How high the coefficient can go? (the higher the better). I am hoping somewhere higher than 0.5 under dry condition.
Thanks ahead!
Robert Yuchemical machinery mfgr. - San Jose, California, USA
2003
A. Rubber or similar.
Guillermo MarrufoMonterrey, NL, Mexico
A. Consider, $ lowest to highest, Polyethylene, Polypropylene, Teflon
Jeremy Gray- Melbourne, Australia
Ed. note: We think Jeremy has misread the question.
Multiple threads merged: please forgive chronology errors and repetition 🙂
Q. I need to increase the surface friction between a stack of stainless spacers. I am applying a compression force to the stack and relying on surface friction to hold them. I have called out a sand blast finish but this quickly became smooth and allowed the spacers to move. I also need to maintain a tolerance of .005 on the thickness of the spacers. Any suggestions for a repeatable finish specification?
George Fowlerdesigner - Jackson, Tennessee
September 14, 2009
A. If sand blast did not work, you might try a knurled-fine -finish and have it on the high side so that you would eventually end up on the low side as it wore down.
Are "star" washers a possibility?
- Navarre, Florida
A. Heavy compression causes twinning of the metal. This makes the material stronger, but also smoother.
Annealing them will soften them up, and provide you with a bit more friction.
If you can choose another metal, I would lean towards aluminum or an aluminum coating. The coefficient of friction between two pieces of raw aluminum is greater than one.
- Toledo, Ohio
Multiple threads merged: please forgive chronology errors and repetition 🙂
High friction, durable coating needed for 6000 and 7000 series aluminum alloys
Q. I need some help finding a surface treatment for aluminum alloys (specifically 6061-T6 and 7075-T73) that will provide high friction at the contact surface of a bolted joint. I had several recommendations to look into plasma spray processes for applying tungsten carbide or ceramic powders, but these coatings don't appear to be very durable and are prone to chipping during handling (bumping things around when moving bolted assemblies into place).
Does anyone have a suggestion for a durable surface finish that will provide a consistent high friction value? I'm interested in chemical treatments that increase surface roughness, penetrating stable surface oxides like anodizing, deposited finishes like plasma spray...pretty much anything. I'd even be interested in mechanically prepared surfaces that provide high surface texture as long as the raised material won't crush under bolt pressure.
In order of preference these are the behaviors I'm interested in:
1. High Friction (above 0.3 dry static friction coefficient, higher preferred). Many published materials have a static coefficient higher than this but I've found them to be inaccurate.
2. Durability. The surface finish needs to hold up to normal wear and tear without cracking or flaking and generating particles. Normal wear and tear would be bolting and unbolting two parts about a half dozen times.
3. Corrosion resistance. Since I'm primarily interested in aluminum alloys, I need a minimum level of corrosion resistance. We typically use chemical conversion coating per MIL-DTL-5541
[⇦ this spec on DLA] Class 3 to get a minimum level of protection.
4. Low porosity. I would prefer low porosity to make it easier to clean the surfaces and reduce drying time.
5. Solvent compatibility. At a minimum it needs to be cleanable with isopropyl alcohol. If stronger solvents like acetone
⇦ on
eBay
or
Amazon
[affil link] Warning! Flammable!
or MEK work then that's even better.
I know it's a tall order, but I'm hoping for some help :o). This is for a commercial aerospace application with a fairly high volume of work if a suitable finish is found.
aerospace design engineer - Dulles, Virginia
February 17, 2010
A. Have you thought about hard anodizing type 3?
Leslie Naylor- Durban, South Africa
A. I suggest that you investigate EKagrip® friction shims, which is a product developed by ESK for this type of application. The shims are spring steel with an electroless nickel coating (diamond particles are suspended within the coating) that provide a high friction contact surface. You can find some technical information by Googling "EKagrip® friction shims".
Toby PadfieldAutomotive component supplier - Michigan, USA
I requested some additional information from ESK on their diamond/electroless nickel coating. That's exactly the type of coating I was looking for. If they can put it onto corrosion resistant steel instead of spring steel then it's an excellent match for what I'm looking for.
Thank you!
aerospace - Dulles, Virginia, USA
March 1, 2010
Q. Hello. My name is Mark. I'm a mechanical engineer for a plasma fusion research laboratory (government). I need a high friction coating for a stainless steel (316SS) to G10 bolted joint. The static coefficient of friction required is 0.5 or greater. This joint transmits high torque. The coating could be applied to either surface, but I'm assuming the stainless steel part will be coated. The average contact pressure is 25MPa. The operating environment is ambient air, room temperature, but all materials should be low in magnetic permeability (i.e. stainless steel).
Mark SmithDesign Engineer - Princeton, New Jersey
June 7, 2011
A. Hi, Mark.
I have recently learned of "friction shims". These are thin shims of metal plated on both sides with nickel or electroless nickel with imbedded diamonds or other hard particles. What apparently happens is the tiny hard particles dig into the opposing faces when you bolt up your joint, and give the plate a sort of mechanical interlock. You could plate one of the two surfaces with this material rather than use a friction shim, I suppose.
Regards,
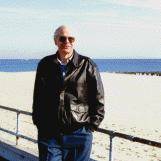
Ted Mooney, P.E.
Striving to live Aloha
(Ted can offer longterm or instant help)
finishing.com - Pine Beach, New Jersey
by William Safranek
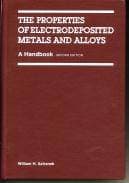
on eBay or Amazon
or AbeBooks
(affil link)
A. According to W. Safranek's book "Properties of Electrodeposited Metals and Alloys" ⇨
second edition, p. 536, electroless nickel coating on pin against ring of Cr steel had a coefficient of friction of 0.6-0.7. Test was determined by machine consisting on pin and rotating ring.
Monterrey, NL, Mexico
A. The coefficient of friction of electroless nickel composite coatings incorporated with hard particles is generally of the order of 0.60-0.75. This is mainly due to the increase in roughness of the surface following incorporation of these hard particles.
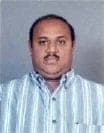
T.S.N. Sankara Narayanan
- Chennai, Tamilnadu, India
(ed.note: The good doctor offers a fascinating blog, "Advancement in Science" )
A. During skin pass, use different working rolls. Use higher roughness working rolls.
Davy Liu- Shanghai China
A. Hi Mark
I would take a look at some of the anerobic adhesives used for thread locking. The principle is the same. Cheap, easy to use, and magnetically invisible. Try
www.loctite.co.uk/cps/rde/xchg/SID-EAC475DA-AD267EF1/henkel_uke/hs.xsl/fullproduct-list-loctite-4995.htm?redDotUID=1000000I8TX ⇩
There will be similar products available in US.
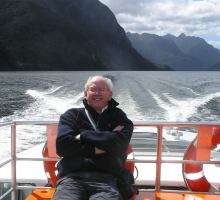
Geoff Smith
Hampshire, England
Ed. note: The loctite.uk site still exists, but not that specific page.
Q, A, or Comment on THIS thread -or- Start a NEW Thread