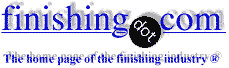
-----
Improving sheeting action of Deionized water
What chemicals are safe to add to a DI water rinse to improve the sheeting action of the water to prevent water spots that may contain residual minerals such as phosphorous and chlorides. The system contains a detergent wash, clear water rinse, and 3 DI tanks with the final tank being maintained at 10 microsiemens. Parts are blown off with air before drying. Is there a simple way to detect the presence of the residual minerals.
Richard ParisPlant Engineer - Cumming, Georgia
May 11, 2011
May 13, 2011
Hi, Richard. I don't think you can add anything to a recirculating D.I. rinse because the ion exchange will remove it or it will contaminate the resin.
I suppose you could use just the first two rinses for the recirculating D.I. rinse and add some wetter into a stagnant 3rd rinse, but I haven't seen it.
If you still can't get total freedom from spotting, the only remaining option that I know of is a vapor dryer. This is the same thing as a vapor degreasing unit except you are using it to wash away water and its spots instead of grease (this results in the formation of a lot of HCl, which is very tough on a stainless steel degreasing unit).
Regards,
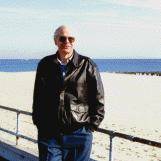
Ted Mooney, P.E.
Striving to live Aloha
(Ted can offer longterm or instant help)
finishing.com - Pine Beach, New Jersey
May 16, 2011
The conductivity is a direct indication of the presence of mineral contamination of the water. DI water with a conductivity of 10 microsiemens is usually clean enough to prevent water spots. However, it is not the conductivity of the water feeding the rinse that is most important. What is most important is the purity of the water that dries on the parts, and this may be much higher than 10 microsiemens.
I recommend that you catch the drippings from the parts after the final rinse, and check the conductivity of this water. If it is high, then you will need to improve the rinsing. The easiest way to do this is to increase the flow rate in the rinse, but some agitation may also help if the dwell time in the rinse is short.
consultant - Cleveland Heights, Ohio
May 18, 2011
Thanks for the advice. Currently the rinse tanks are stagnant. Our DI system is capapable of supplying 1 or better purity to the tanks. We are investigating adding reciculation to the rinse and filtering this water and maintain it closer to 1 microseimen. The idea being the combination of the movement will aid in the rinsing action
and the higher purity will insure a spot free rinse.
We feel the phosphates and the chlorides are coming from the cleaning agent and the use of tap water in the first rinse.
- Cumming, Georgia, USA
Q, A, or Comment on THIS thread -or- Start a NEW Thread