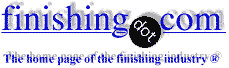
-----
Blue or Black Chrome
I am restoring my motorcycle and would like to make it distinctive at the same time. I plan to have all the chrome on the bike redone but I would like to have it done with either a blue or black finish to it, similar to the effect that bluing causes in chrome. I have had difficulty finding any companies that do this and am not sure that it is possible, can you please point me in the correct direction or tell me how else I could achieve this effect. Thank you.
Ashley Jaimison Sanders- Yellowknife, NT, Canada
2000
2000
Ashley:
As you know decorative chromium plating is a silver color but it has a nice bluish cast to it. It is only about 0.003 to 2.5 microns in thickness, which is to say that it is a really thin coating. It's durability and hardness is attributed to the fact that it has an extremely hard oxide layer which forms on it protecting the metal. Now, if you're wondering about a durable coating which is more blue than what you'd normally see on chrome I'm at a loss. I only know a few ways this can be done, but they are not practiced commercially:
1). Heating the actual chrome plated part will impart a bluish cast. You'll often see this look on the side-pipes of motorcycles. (It's not very attractive). But perhaps putting a part in a kiln would get better results since the item would not be subject to such intermittent heating & cooling.
2) If when plating the chrome the temperature of the bath is raised a blue hazy look develops. Yuck!
3) Use of a chromium substitute, e.g. Zartan which is a cobalt and tin alloy deposit. There are two problems with this: First, it's softer and not as durable and second the process was discontinued. Perhaps there are other chrome substitutes out on the market. I'm not sure. The reason why there ought to be more chrome substitutes out there is because of environmental and occupational health issues. Also, in industrial applications such as the barrel plating of small screws or rivets chrome can not be used since it turns an unsightly white color when it makes intermittent electrical contact. Incidentally, I'd very much like to see a new "thread" of discussion devoted to CHROMIUM PLATING SUBSTITUTES by the experts on this website.
Black chrome is a mixture of other chemicals with chromic acid. When it was first introduced on the market it had a tendency to fade,
(probably from ultraviolet light). I understand that black chrome doesn't have the wear resistance of regular decorative chrome. I think that the quality of commercial baths have improved over the years, so if you like this look it might be the thing to go with.
All you need have to know is that you should care for chrome plated articles, regardless of color, by gentle cleaning with a very mild soap or diluted glass cleaner. Then you might even apply beeswax
⇦ on
eBay
or
Amazon [affil link]
if you want to give it more longevity. Abrasive chrome polish is O.K. if used sparingly or very occasionally.
You can check the jobshop directory on this website. Now as for choosing a jobshop you might want to find out if they do copper plating. I'll quickly give you an overview on how "show chrome" as it is called in consumer vernacular is processed:
Normally the motorcycle parts are stripped down to the basis metal (usually steel), and then they are polished and buffed to a mirror-like finish. All blemishes in the metal are removed. This can be quite elaborate. The worker is truly a craftsman. Sometime parts are block sanded by hand in order to remove ripples, this type of work is very labor intensive and expensive. Usually machinery can be used to accomplish the abrasive operations for a motorcycle order. The more elaborate work is for damaged parts or for parts where the original manufacturing of the part caused waves in the steel. The next step which is optional, but which gives a finer quality is a two part plating process whereby copper is deposited on the steel. First a strike coating of alkaline copper which allows for acid copper to be deposited. The best quality comes from buffing or polishing these parts. When the buffer works on these parts the small pits can be removed. Now, in the case of die-cast zinc pot there may be many pits. Often the shop will copper plate and polish repetitively until the blemishes are removed. Lead solder may be employed to fill the pits. Once the coppered part is ready it is nickel plated, rinsed and immediately chrome plated. Then the part is thoroughly rinsed and inspected. The things to look for are "misplates" where the yellow cast of nickel shows. This situation is caused by the poor current efficiency inherent with chrome plating. It takes a very skilled plater to figure out just how to "zap" the part with electrical voltage. In custom work, it is all based on experience and the workman uses his best guesstimate. If he's really a genius I guess he'd figure out the surface area and calculate the amperage per square foot and all that, but I think most custom platers just shoot from the hip. Also there may be what are called "chrome burns" on the tips and high areas of the part. These are unsightly white or grayish areas that, fortunately, can be polished to chrome brightness. The only sacrifice is that there might be noticeable buffing lines in the part. It's all a matter of judgment, if the plater's guesstimate is way off the part will either look matte gray or yellowish (nickel), he will then strip the chrome, which luckily doesn't [usually] hurt the nickel plating underneath and replate it.
Another option would be to have a color anodize placed on the aluminum motorcycle parts. You'll have to find a shop that does custom anodizing. Its not as brilliant at chrome. Although, chrome can be plated on aluminum but this requires special knowledge on the part of the plater on how to treat the metal in order for it to accept plating. (The oxide layer is removed and it is quickly zincated; but it's actually a difficult and involved process).
Regards,
- Tecumseh, Michigan
Q, A, or Comment on THIS thread -or- Start a NEW Thread