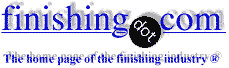
-----
Avoiding tin-embrittlement of steel through coating or material selection
First off, thank you to the contributors and editors of this forum and website. It is a valuable resource that I've reviewed periodically for several years. And now to my question:
Our group at the university offers no-cost assistance to manufacturers in the state, and I am currently fielding a question from a local company who uses formed and welded 12-gauge mild steel as a cover over the top of a float glass operation. This cover regularly requires replacement, and replacement costs are prohibitively high. I am seeking ideas on an alternative material, or a coating that would help.
In their application hot glass floats on a bath of liquid tin and this steel cover is mainly used to maintain a protective atmosphere for the tin, but also to keep debris (including tin droplets) off of the glass. Over time (10-12 months) the steel becomes quite brittle and requires a change-out, which is quite expensive because operation is interrupted.
The environment within the chamber is an elevated temperature mixture of nitrogen, hydrogen (5%), along with some hydrogen sulfide, tin sulfide, and water vapor. Chlorine is periodically introduced into the system with a duration and frequency of 1 hour every few months (not clear on a reason for this step). The cover is ~5" above the glass (which itself is 600 - 700° C), but it is somewhat protected by a heat exchanger and a 1" thick ceramic board shield. Portions of the steel cover are still expected to reach 500° C.
Analysis isn't yet complete, but an early hypothesis is that liquid/solid metal embrittlement is leading to the degradation of the steel. Fracture faces show that the fracture mode is intergranular, energy dispersive spectroscopy shows a high (over 1%) concentration of tin on the fracture face along with isolated iron-tin intermetallics situated at triple-points (where 3 steel grains meet), and x-ray fluorescence shows a very high concentration of tin on both the inner and outer surfaces of the steel cover. Polished cross-sections reveal the presence of a Mn-S intermetallic (below the general oxide layer) that seems to penetrate the steel at external grain boundaries (to a depth of 40 microns in some areas), and some localized areas where this Mn-S penetration is much deeper. I haven't yet determined if this Mn-S near the surface is formed by a reaction with hydrogen sulfide (thoughts?).
In reviewing information and papers on embrittlement by tin it seems that most steels would be considered susceptible. The end goal would be an economical alternate material, or a coating, that would avoid liquid metal embrittlement by tin, while also dealing well with the other environmental conditions. Some ideas I've considered were chrome plating the steel, or using copper sheet instead of steel. Neither of these ideas seem terribly economical, and copper would not likely deal well with hydrogen sulfide or chlorine. I am curious if anyone has better ideas.
Many thanks!
- Ames, Iowa, USA
March 29, 2011
April 20, 2011
Sir:
In my basement I have a book, the title being something like "Corrosion and Corrosion Protection Handbook," which I purchased several years ago. It addresses the very types of problem(s) you describe. Unfortunately my basement is not well organized, and searching this book is very time consuming.
Regards, Dr. Thomas H. Cook, Hot Springs, South Dakota, USA
Galvanizing Consultant - Hot Springs, South Dakota, USA
Dear Mr Rick,
Hello !
In my view (not sure) but I guess using stainless steel having composition of nickel, would solve your problem as its stain proof sheets.
Thanks
- JODHPUR, RAJASTHAN, India
April 22, 2011
<
![]() |
Titanium-aluminum-tin is a common alloy of titanium. I have only used CP (commercially pure) Ti, but this might be worth a try. There is (I hope still) an outfit in Oregon, B-J, that fabricates Ti by spinning and maybe other processes. Their crucibles were very rugged. The temperature in your app is well under 800° C, so it should not have transus problems. Brian Fitzpatrick- Peekskill, New York, USA If I understand you correctly, the steel plate covers the molten tin bath and comes into contact with it. If this is the case, your problem is almost certainly caused by the molten tin diffusing into the steel to form an iron-tin intermetallic (FeSn2). This is characteristically grey in colour. The only way to prevent intermetallics forming is to use a system that doesn't form them. Off hand I cannot think of a suitable cheap metal sheet that will fit this criterion, but if you look in the Metals Handbook, I am sure you will find some. Using stainless steel will reduce the rate of intermetallic formation, but will not stop it. ![]() Trevor Crichton R&D practical scientist Chesham, Bucks, UK |
Q, A, or Comment on THIS thread -or- Start a NEW Thread