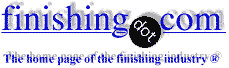
-----
Optimum time for acid pickling before galvanizing
Q. Hi,
I want to know how long steel should be in acid to get better surface and have better galvanized steel.
I want to know the time which steel fabrications must be in kettle to get optimum zinc coating.
What is the speed?
What are the parameters that affect zinc coating?
employee, master student - Shiraz, Iran
March 9, 2011
March 9, 2011
A. There is no single answer to this open question.
The influencing factors that you didn't mention include:
acid type?
acid strength?
acid temperature?
Fe content of acid?
temperature of steel?
degree of rusting on steel?
presence of mill scale on steel?
amount of free acid liquor round item (how closely packed)?
hollow steel or solid?
depth of immersion?
acid agitation or not?
You can see that so many things influence how long steel should be pickled, and so without knowing these, definitively, then there is no answer.
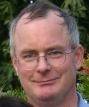
Geoff Crowley
Crithwood Ltd.
Westfield, Scotland, UK
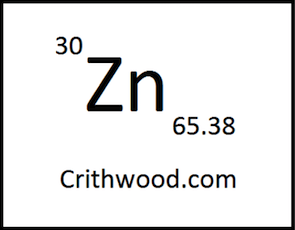
March 13, 2011
Q. Dear Sir,
acid type: HCl
acid strength: in initial stage it is 15%
acid temperature: room temperature
Fe content of acid: I cannot measure, I do not know the exact way.
temperature of steel: steel immersed in hot water about 65° C
degree of rusting on steel: I do not know how to say but it is not varying
amount of free acid liquor around item (how closely packed): steels packed in a way that acid can flow on its surface
hollow steel or solid: the steels are most beam and pipe
depth of immersion: full immersion
acid agitation or not: no agitation
Thank for your attention
- Shiraz, Iran
A. Given the info provided (and the pickle time is still depending on the other unanswered factors), then pickle time could be anything from 20 minutes to 3 hours.
Depth of immersion is not whether or not the steel is fully immersed (it must be), but how deep in the acid it is immersed.
Acid strength has some bearing, but not as much as Fe concentration. When the acid gets closer to saturated with Fe, it will not pickle, even with higher concentration HCl.
If you don't know a way to measure (or approximate) the Fe, you need to find out. It's common to measure HCl and density, and assume the rest of the density is attributable to iron chloride, and so estimate it from that.
Free acid is important. If you have 5 mm free acid from every surface, it might take twice as long to pickle as if you had 100 mm between items.
Agitation can reduce pickle time, but be wary of some means of agitation that remove HCl to atmosphere (such as bubbling air through). You don't need your HCl in the shop, you need it in the tank!
Very rusty steel (thick enough to remove rust flakes by hand) can take 6 hours. Very clean fresh made steel with light mill scale can take 30 mins in the same conditions, so this is an important factor.
Its unlikely that anyone could give a formula for estimating acid pickle time given the large number of variables, some of which are subjective.
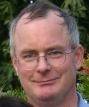
Geoff Crowley
Crithwood Ltd.
Westfield, Scotland, UK
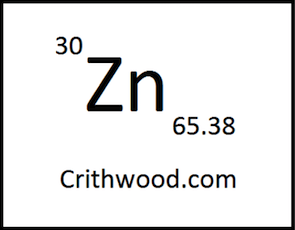
Q. Thank for your answer sir...
Can you advise me some ways to reduce zinc consumption in production line?
our zinc consumption is about 5-6%.
Such as flux formula, temperature of pre-heating, the chemical composition of kettle.
I want to get optimum zinc coating thickness on steels.
- Shiraz, Iran
March 25, 2011
A. This is a very broad (wide) question, and answers are quite specific to each location, operation, etc.
The question is a bit like asking "how can I get better economy in my car?".
The general answer is "slow down".
But on zinc: depending on your situation, 5-6% might be good, might be bad.
It will depend on material type, & variability.
Flux composition that's best depends on material type, and heated drying or not.
Zinc composition depends on material type and flux type.
Temperature depends on material type.
All depends on process type? Continuous strip galvanizing or post fabrication hot dip jobbing galvanizing?
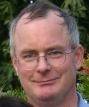
Geoff Crowley
Crithwood Ltd.
Westfield, Scotland, UK
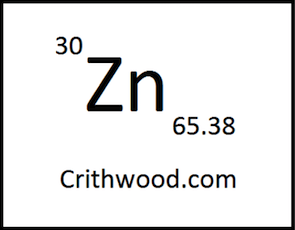
Q. Hi.
It is post fabrication hot dip jobbing galvanizing, we galvanize every piece that may have use in electricity line (power station).
Our steels are most ST57 and ST32.
We try to dry steels before dipping in bath.
My other question is where can I find a good catalog for a good drying machine.
Thank for your attention.
- Shiraz, Iran
April 7, 2011
Q. Dear Sir,
Continuing the discussion, I would like to know the following for a pickling tank of 7 meter (L) x 1 meter (W) x 1 meter (H):
1. What is optimum quantity of steel to immerse at a time in a tank for best pickling quality & lowest time?
2. Is any gap required to keep between two components to pass the acid in proper way? if yes, what should it be?
(Components are 4 to 6 meter L angle sections).
Please reply
- India
March 26, 2012
Q. Dear Sir
We are using HCl acid for pickling steel items for hot dip galvanizing.Despite of keeping the parameters in range, it takes acid too much time to pickle the material. Material is first degreased in an acid degreasing tank with a pH about 1.8.What other factors can control and reduce the pickling time of the material as it badly affects our daily production.
(HCl Parameters kept as:
% Concentration from 10-25, Degree baumé 10-33), Iron content <80 g/l)
- Dammam, Saudi Arabia
July 15, 2012
A. All of the following can cause slow pickling in HCl:
Too low of acid concentration.
Too low of iron (Fe+2) in the HCl.
Too high of inhibitor concentration (typically inhibitor companies recommend too much inhibitor). Bad inhibitor.
Too high of zinc (Zn+2) in the HCl.
Too low of temperature in the HCl.
Improper acid degrease.
Regards,
Galvanizing Consultant - Hot Springs, South Dakota, USA
A. Purpose of Pickling is to clean the surface, free from all rust etc,
Naturally Pickling time depends on the surface condition of work to be Galvanize.
It is recommended: Go for sand / short blasting if the surface is badly rusty.
- Check the Acid should be wax free.
- Rest all your parameters are OK.
Self - Mumbai, India
July 23, 2012
Q. Thanks for replies.
Okay, I understand. So what should be the standard limit for the Iron content? I read in an answer that too low iron content also effect pickling time? And for HCl what's your suggestion about temperature as we are not doing any external heating, etc.?
We were again putting the jigs in pickling baths for re galvanizing/cleaning and the jigs had zinc all over the surface. Maybe that caused us trouble. Now avoiding that.
And, yes, one thing more -- can we refresh acid by putting calculated amount (considering volume and concentration factor) of new concentrated acid in baths?
Thanks for your help! You people are really helping us all.
- Dammam, Saudi Arabia
July 25, 2012
A. Dear Mr. Jafar Orangi
It seems that you are dealing with structural Galvanizing. Trust you are using 15 - 20% HCl for Pickling at ambient temp.
- It is almost difficult to predict duration of Acid pickling. It is basically depends on the rust contamination on work.
Normally in case the work is new it takes 20 minutes. For good Galvanizing I recommend sand blasting the job before pickling.
- Dipping Time: Again it depends on the size of work to be Galvanized. But in layman language, after dipping the prepared work in Zinc bath, look on the surface of bath, keep the work in the bath as long as the bubbles are coming out. Keep the work shaking in the bath.
- Speed of extraction. It should be reasonably slow so that all extra Zinc can be drawn out.
- Parameters affecting the Plating thickness: Zinc bath Temp., Chemistry of work to be Galvanized and dipping time.
Hope it will meet your requirements.
Self - Mumbai, India
Q. Hi,
I work for galvanizing Company in Jeddah. Recently, we start applying Kleingarn's to control pickling tanks. I'd like to know, if the presence of Zinc chloride at the pickling tank would affect the performance of Pickling Hydrochloric.
- Jeddah, Saudi Arabia
October 8, 2013
A. Yes, zinc chloride will depress the effect of pickling in HCl.
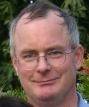
Geoff Crowley
Crithwood Ltd.
Westfield, Scotland, UK
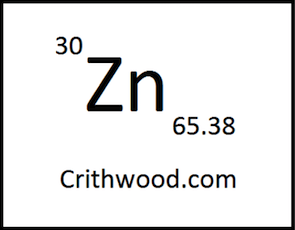
October 11, 2013
Pickling Time and Hot Dip Galvanize Coating
Q. I have a question about what are the relations between pickling (HCl acid) time and galvanize coating thickness in hot dip galvanizing.
Amila RuwanpathiranaProject for Reduction Galvanize Coating - Colombo, Srilanka
December 27, 2018
A. If the work is not pickled long enough, then oxides will not be removed and galvanized coating will not be continuous, there will be "bare patches".
If it is too long, then the steel starts to dissolve in the acid, becomes "etched", the surface is re-profiled and that extra surface area will attract more zinc, and a thicker coating will result.
But that isn't very precise...
The answer though lies in the many variables involved.
* Rust level/thickness on steel
* Millscale thickness
* acid concentration
* acid temperature
* acid contamination (concentration of zinc chloride for example)
* time between acid and rinse
* chemistry of rinse
* many more factors
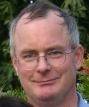
Geoff Crowley
Crithwood Ltd.
Westfield, Scotland, UK
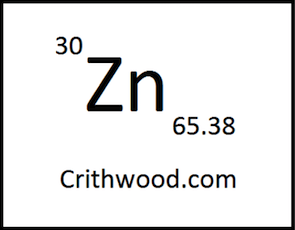
Q. A very useful discussion, indeed!
If I can step in this intense discussion about pickling, I would like to ask why over-pickling can cause an excessively thick galvanized coating, according to what is commonly reported in the technical manual about the subject. This point is quite obscure to me, although have clear that over-pickling causes an increase in roughness and a spoiling of the dimensional tolerances. Many thanks.
- napoli, italy
February 15, 2019
A. Umberto,
The surface of the steel gets a different surface profile with over-pickling. The acid doesn't etch all parts of the steel at the same rate, and it ends up "rough" in a similar way to how shotblasting leaves the steel surface.
If your customer asked for a thicker than usual coating (for example ISO 1461 asks for min 85 µm on steel >6 mm thick, perhaps customer asks for 140 µm), then how will you achieve this? Most common way is to shotblast the steel prior to processing. If you shotblast to say SA2.5 (standard), then you would probably get 140 µm. The reason that the coating thickness is higher in the shotblast situation is because the steel has been re-profiled. It now has effectively greater surface area to alloy with the zinc. Over-pickling does the same, causes a greater actual surface area of steel per m2 (ft2 for USA :) ) for reaction with zinc.
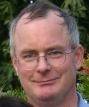
Geoff Crowley
Crithwood Ltd.
Westfield, Scotland, UK
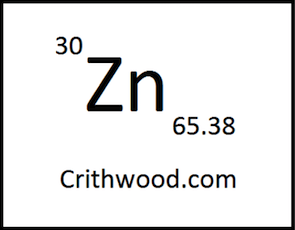
February 19, 2019
Q. Many thanks, Geoff.
Then, in case of over-pickling, I get a thicker Zn coating, but will this coating have a different microstructure in terms of size and morphology of the classical phases which develop in hot dip zinc coating, namely the zinc saturated alpha iron, the gamma, the gamma1, the delta and zeta layers?
- napoli, italy
February 21, 2019
A. Umberto,
The alloy phases you mention are good theory, and in classical cases are visible.
But in practice it is sometimes only possible to distinguish one layer of alloy, and the "pure" zinc that overcoats it.
So to state that over-pickling presents variation in these layers is optimistic.
The additional thickness in the coating is most often increased alloy thickness, but with the rough surface of the steel, it isn't in nice layers as the classical photomicrographs show, more like looking at a cross section of a haystack!
The pile of alloy crystals also "holds" (retains) more free zinc, and so this part is thicker too. That means the whole coating is thicker, roughly in proportion to an ordinary one, but with less defined boundaries between the layers.
In severest over-pickling, surface roughness of the coating is apparent at millimeter visual level.
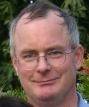
Geoff Crowley
Crithwood Ltd.
Westfield, Scotland, UK
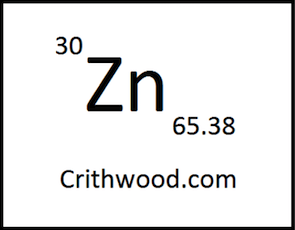
February 21, 2019
Q, A, or Comment on THIS thread -or- Start a NEW Thread