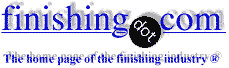
-----
Chrome plating of long small bores
Q. My name is Bob Brigden, we manufacture HV insulators in South Africa. For the cores we pulltrude glass fibre/ epoxy rods, we now want to manufacture our own dies which have to be chrome plated internally.We have a small plating bath but I am not sure how to plate a 14 dia internal bore 700 mm long. Shall I use a straight anode through the center of the bore, then my anode area will be less than the area of the bore. Use a mesh type anode, or coil an anode around a small fibre glass rod and tension the ends.
Help would be greatly appreciated
Tooling consultant - Kwazulu Natal South Africa
March 2, 2011
A. One of several approaches would be to lead solder plate an appropriate steel rod. Use locater pieces on the end to have it dead center in the bore and keep it there as the temperature rises. The ends need to be mostly open to allow gas to escape and solution to flush thru. Cover the rod with craft paper when inserting it into the bore so that you do not touch the part. Remove the paper as possible. You probably will need to tape off a fraction of an inch of the top and bottom of the rod to prevent a high build up on the ends.
James Watts- Navarre, Florida
March 3, 2011
A. This is the method to chrome inside rifle barrels.
I would go along with James except to use copper or brass rod to minimise the voltage drop along the bore. You can plate the rod with pure lead or tin/lead if you want it harder.
Jig the parts vertically to get some solution movement in the bore or best pump the solution (a small bleed pipe off the filter pump)
If using heavy current, it is useful to incorporate a spring to tension the anode and feed current from both ends.
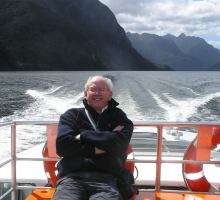
Geoff Smith
Hampshire, England
March 8, 2011
I like Goeff's comments and would definitely use brass rather than copper. Conductivity is adequate and is a lot stiffer.
- Navarre, Florida
Q, A, or Comment on THIS thread -or- Start a NEW Thread