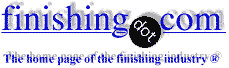
-----
Seeking Hard Anodized or other finish for R & D project
February 15, 2011
Here's a very rough idea of what were looking to get coated. We have the final project going through the patent process so the mock up must be unfortunately vague, sorry. The red portions are the areas needing a very durable hard coating that hopefully can have a unique look as well.
The recessed rails will be roughly 1/4 wide and from 2-3" long. The material will be a 7k series aluminium alloy, probably 7075. We will have product that is both cast and machined if that's a factor. Some of the factors I'm having to consider are.
1. Looks: We'd like to give our product a very striking look that's recognizable but functional.
2. Weathering: It will be in the elements and we'd like it to retain it's look even when exposed for years if possible.
3. Wear: There's the second component to the rail that will "click" into place and will be movable. We'd like it to be able to withstand the wear of it being moved and amplitude (i.e if were attached to a vehicle going down a dirt road bouncing around). Would it also be advantageous to coat both the base piece and the clip portion with the same coating or a different coating let us know about that as well.
4: Friction: With the mechanism it needs to be able to create enough friction to hold in place but when it's released still be slick enough to slide. Would having both items coated be too slick for instance?
5: Compatibility: The portion not coated will be anodized, possibly powder coated. Will this affect the coats you offer either applied first or after? Is there a masking process? And how does this affect cost? Can you do two different Anodizing on one piece and still be cost effective? I.E. say Type II with a dye on the primary portion then do a Type III Class I in the recess?
6: Price: Last but not least. Initially we need anywhere from one to ten samples coated that we can field test. When we go to production we'll need in the thousands done. If you can give me a couple different options of suggestions that would be great.
Any recommendations or information you have, as far as types of coatings you offer that would work for our purposes would be greatly appreciated. If you have any samples please send them to us . Thank you!
electronics - Saint George, Utah, USA
Q, A, or Comment on THIS thread -or- Start a NEW Thread