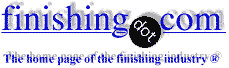
-----
Abnormal Happening on GI Sheets
January 30, 2011
I work in dry type hot dip galvanizing line. We use zinc about 100 mt and lead about 30 mt in kettle and add zinc-aluminium alloy instead of pure aluminium slab, by calculating aluminium about 0.3% on total zinc usage. Zinc bath temperature for production is 470 °C ~ 475 C and production line speed is about 50 m/min. Air knife air pressure is about 20 kPa and Air knife slot is 200 mm above the zinc level.
At that condition, zinc coating weight on GI sheets is about 150 gm/m2 and some very fine zinc or zinc dross particles are stuck on the upper surface of GI Sheets and also some shining tiny spots (sparklers) are spread on both surfaces of GI sheets.
So , I would like to know-
-whether our zinc coating weight is abnormal or not?
-How is the possible way to reduce zinc coating weight in our line conditions?
-Why fine zinc particles are stuck on the upper surface of GI sheets?
-Why shining tiny spots are appeared on the surfaces of GI Sheets?
-How can we prevent such things from happening?
Please, somebody kindly advise me.
Plant Manager - Yangon, Union of Myanmar
Dear Mr. Geoff and Dr. Cook,
I would like to request, please kindly advise me upon above mentioned galvanizing problems.
Fine zinc or zinc dross particles were stuck on the upper surface of
GI sheets even soon after drossing.
Thank you so much for your help and previous advice.
- Yangon, Union of Myanmar.
March 3, 2011
March 8, 2011
Ye,
Its nearly 30 years since I had anything to do with continuous strip galvanizing of sheet, so I'm well out of date in that technology.
But zinc is zinc, and dross is similar in most molten zinc.
I wonder if your dross isn't heavy enough (not enough density), and is that caused by low Pb levels.
With very low Pb, there can be a tendency for dross to become suspended in the zinc. By low I mean <0.3%.
At levels between 0.5 and 1% Pb, some of the dissolved Pb seems to be attracted to dross in suspension, increasing its density and causing it to sink to the kettle floor.
But this isn't my field really, and your higher Al levels might make what I've said invalid.
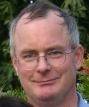
Geoff Crowley
Crithwood Ltd.
Westfield, Scotland, UK
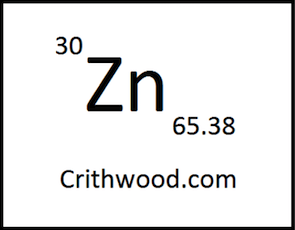
Q, A, or Comment on THIS thread -or- Start a NEW Thread