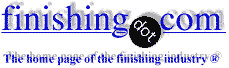
-----
Question about Nickel Dragout
We have been having issues with our dragout becoming too concentrated, and I am trying to write a short instructable type document for our plating guys. I have got a small portable EC/TDS meter to measure contamination but am not sure what levels to set as a maximum for contamination. The idea is to try an save money on water usage, by stopping the guys running the weir system all the time. I'm hoping this way they will only add water when it is needed rather than constantly. So, what should I set as a limit for contamination?
Mark McKinnonPlating Technician - Rugby, UK
January 31, 2011
First of two simultaneous responses -- February 2, 2011
The answer to this question depends upon several factors.
First, the number of rinse tanks that you have. Most platers have a dragout rinse that is used to replenish evaporation from the plating tank. Usually, this stays well below 50% of the bath strength. You need to control the conductivity in the last rinse after nickel plating.
The second important factor is what the next step will be. If nickel plating is the final step and you want a spot-free rinse, then the conductivity will have to be very low in the final rinse. On the other hand, if the next step is chromium plating, you only need to be sure that the nickel, chloride and boric acid concentrations are low enough to avoid problems in the chromium plating.
Some platers would argue for allowing a higher level of contamination, but, for most platers, the conductivity in the last rinse before another plating operation should be the conductivity of your water plus another 400-800 microsiemens which on a TDS meter would be 250-500 mg/L above the meter reading on the water feeding the rinse.
Lyle Kirman
consultant - Cleveland Heights, Ohio
There is no universal answer to your question. Most likely you will need to make a correlation between TDS and a nickel concentration that is acceptable for your effluent to waste treatment and then add a safety margin before determining your TDS setpoint. If drag-in to the next process is the main problem, you'd have to make a similar correlation to determine your TDS setpoint. To reduce water consumption though, nothing will be as effective as adding at least a drag out rinse that you can recover back to the tank followed by a counterflowing rinse. If you don't have any room in your line for more rinses, then consider spray rinsing the parts above the process tank before entering the rinse. This will cut down on the required water flow by 50% or more depending on the part geometry. Good luck.

Jon Barrows, MSF, EHSSC
Kansas City
Second of two simultaneous responses -- February 2, 2011
Mark,
I get a feeling that you are going to cause yourself all sorts of problems by reducing the water flow on the rinse tanks.
The first thing you must do is check the specifications you are working against to see if there are any conductivity/TDS limits that you must meet. If there are you can continue to reduce your rinse water flow until you are just under the upper limit, although I would suggest that you don't go any closer than 10% of the upper limit, to allow for variations that will naturally occur in conductivity/TDS.
If there are no limits you have to ensure that the level of contamination is not going to affect any further processes or the final product if it is the last stage.
I have been involved with many a plating shop that has tried to reduce costs by reducing the water usage in the rinses and almost always the result is an increase in plating problems. Just be careful with your approach and make sure you are not going to create more problems than you solve for the want of saving a few pennies.
Aerospace - Yeovil, Somerset, UK
First of two simultaneous responses -- February 3, 2011
Thanks guys! After our nickel plate the parts go through a dragout tank, two rinse tanks, then a final hot rinse before drying. Is it just the final hot rinse I should be monitoring to ensure a spot free finish? Apologies for the probably very stupid questions, Still fairly new to this job!
Mark McKinnon- Rugby, United Kingdom
Second of two simultaneous responses -- February 3, 2011
Assuming that the hot rinse counterflows back to the other two, then certainly. When you monitor the TDS in that tank, you are taking care of all 3. If the waste water from the final rinse does not flow back up the line, then I would make the change so that it does. It would work something like this---
Monitor the hot rinse for TDS. When the TDS is exceeded, a solenoid opens up that puts in fresh water to the hot rinse (RO/DI is my preference). The hot rinse overflow (discharge) is directed to the 2nd flowing rinse as make-up. In turn the overflow from that rinse is directed to the first flowing rinse as makeup. The overflow from that first rinse (the dirtiest one) goes to waste treatment. The dragout rinse remains separate from that counterflow chain, but you should use it to replenish evaporation from the process tank. As liquid level falls in the dragout tank, you'll need to replenish it with RO or DI water since it ends up back in the process tank. That can easily be done automatically with two level controls, a solenoid and a small pump. This scheme uses a very small amount of water compared to flowing rinses, but the downside is that your waste treatment plant gets slugs that are many times more concentrated than they were before. This can sometimes be a big problem so you will need to consider the impact on waste treatment before making any change that will alter your normal gpm flow of waste water. Good luck.

Jon Barrows, MSF, EHSSC
Kansas City
February 3, 2011
Q, A, or Comment on THIS thread -or- Start a NEW Thread