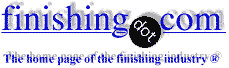
-----
Rust spots on nitric acid passivated stainless steel
I have a problem arising at my job where with use nitric acid to passivate stainless steel. We passivate nothing but stainless steel with a chromium level higher than 16%. I need to know if our nitric acid bath which stays between 20 and 25% by volume can be contaminated somehow and cause small rust spots on the surface of these SS parts. The spots usually don't show up until after they leave our shop. Please, I need some info.
Ryan RoyPlant Mager - Bristol, Connecticut, USA
January 14, 2011
![]() |
First be sure the organic soil is completely removed and not re-deposited as floating in the rinse. Then be sure the passivation solution is below 2%/weight dissolved iron. Then be sure the particular passivation solution is approved for the alloy that is rusting. ![]() Robert H Probert Robert H Probert Technical Services ![]() Garner, North Carolina ![]() Ryan, ![]() Ray Kremer Stellar Solutions, Inc. ![]() McHenry, Illinois ![]() If there are hundreds of tiny rust spots, It quite probably was because the customer ran the parts on a rotary brush that was made of 410SS. There is enough iron in 410 to rust. If there are tiny pieces of 410 stuck in the metal, in my experience, there is no amount of cleaning / passivization that will allow it to pass the salt spray test. - Navarre, Florida Do a search on this forum, this question comes up again and again. - UK |
Ryan
Do you perform a high-humidity or water-immersion test on your parts before you ship them? If not, you can pick up a used scientific incubator cheap that will do the trick. Some CO2 incubators (Forma Scientific 3033) will control the humidity to 97% and are a cost effective alternative to environmental chambers for this application. With testing your product, your customer shouldn't get any surprises.
- Colorado Springs, Colorado
January 18, 2011
Q, A, or Comment on THIS thread -or- Start a NEW Thread